Have you ever heard of a progressive cavity pump? It’s a type of positive displacement pump that is widely used in various industries.
A progressive cavity pump consists of a helical rotor that rotates inside a stator, creating cavities that progress from the suction to the discharge end of the pump. This unique design allows for efficient pumping of fluids with high viscosity or solids content.
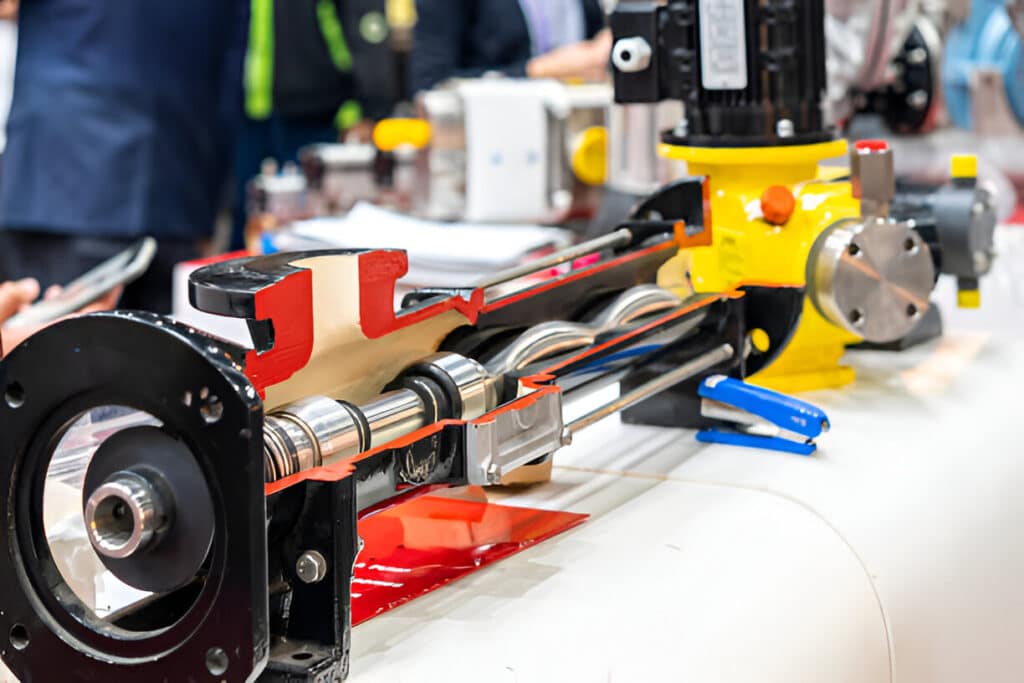
What Is Progressive Cavity Pump
A Progressive Cavity Pump (PCP) is a positive displacement pump that utilizes a helical rotor and a double-helix stator to transfer fluids. The rotor, typically made of metal, fits inside the elastomer-lined stator, forming a series of sealed cavities that progress along the pump as the rotor turns.
This unique design allows PCPs to handle a wide range of fluids, including those with high viscosity, abrasive solids, and varying consistencies. The pumping action is gentle and provides a constant flow rate, making it ideal for shear-sensitive materials and applications requiring precise dosing.
How Progressive Cavity Pumps Work
Progressive cavity pumps operate using a helical rotor that turns within a stationary stator. The rotor’s shape creates a series of sealed cavities along the pump’s length. As the rotor turns, these cavities progress from the suction end to the discharge end.
The continuous motion moves fluid through the pump in a smooth, pulsation-free flow. The cavities between the rotor and stator seal tightly, preventing backflow and maintaining consistent pressure.
Design of Progressive Cavity Pumps
- Rotor: Helical metal component rotating inside the stator, creating cavities for fluid movement.
- Stator: Double-helix elastomer-lined component surrounding the rotor. Forms cavities with rotor to move fluid.
- Drive Shaft: Connects rotor to motor, transmitting power.
- Suction and Discharge Ports: Allow fluid entry and exit.
- Seals and Gaskets: Prevent leaks and maintain pump integrity.
Advantages of Progressive Cavity Pumps
- Low Pulsation, Smooth Flow: Consistent flow, ideal for precise dosing or metering.
- Constant Flow Rate: Proportional to speed, easily controlled with variable frequency drives.
- High Viscosity Handling: Can process fluids up to 100,000+ centipoise.
- Low Shear: Gentle pumping action, suitable for shear-sensitive materials.
- Solids Handling: Can manage fluids with up to 10% solids by volume.
- Short Dry Run Capability: Can operate briefly without fluid without damage.
- Reversible Flow: Direction changes by reversing rotor rotation.
- High Suction Lift: Capable of lifting fluids up to 8.5 meters (25 feet).
Disadvantages of Progressive Cavity Pumps
- Seal flush requirement: For abrasive fluids to prevent damage and maintain performance.
- Mechanical seals or packing: Necessary to prevent leakage, costly and require maintenance.
- Stator wear: Quick wear with abrasive materials, reducing efficiency and increasing costs.
- Speed reducer: May be needed for high-viscosity fluids to ensure proper operation.
- Low operating speeds: 100-1000 rpm, limiting applications in some industries.
- Efficiency decline: Performance drops and energy consumption increases with wear.
- Solid particle limitations: Cannot handle large solids, risking blockages and damage.
- Temperature restrictions: Typically < 150°C, limiting use in high-temperature applications.
Applications of Progressive Cavity Pumps
- Versatile industrial applications: Used in chemical manufacturing, petroleum production, and environmental technology. Handles various fluids and slurries.
- Food industry: Transfers viscous products like sauces and dough. Provides precise flow control and maintains product integrity.
- Wastewater treatment: Pumps sludge and slurries. Handles abrasive solids with consistent flow.
- Oil and gas sector: Pumps crude oil and drilling mud. Offers reliable performance at high pressures.
- Pulp and paper industry: Transfers pulp slurries and abrasive materials. Ensures gentle pumping action to minimize product damage.
Specific Uses of Progressive Cavity Pumps
- Viscous fluids and slurries: Pumping materials with high solids content
- Chemical metering: High-accuracy dosing in manufacturing and industrial processes
- Shear-sensitive materials: Handling without damaging structure
- Abrasive fluids: Transferring in mining and industrial wastewater applications
- Petroleum products: Pumping oils in the oil and gas industry
- Precision dosing: Dispensing in food, pharmaceutical, and cosmetic manufacturing
- Environmental technology: Sludge and wastewater treatment applications
- Fragile solids: Pumping materials with larger-sized particles
- Constant flow rates: Maintaining regardless of viscosity or pressure changes
- Tough applications: Providing reliable service with minimal maintenance
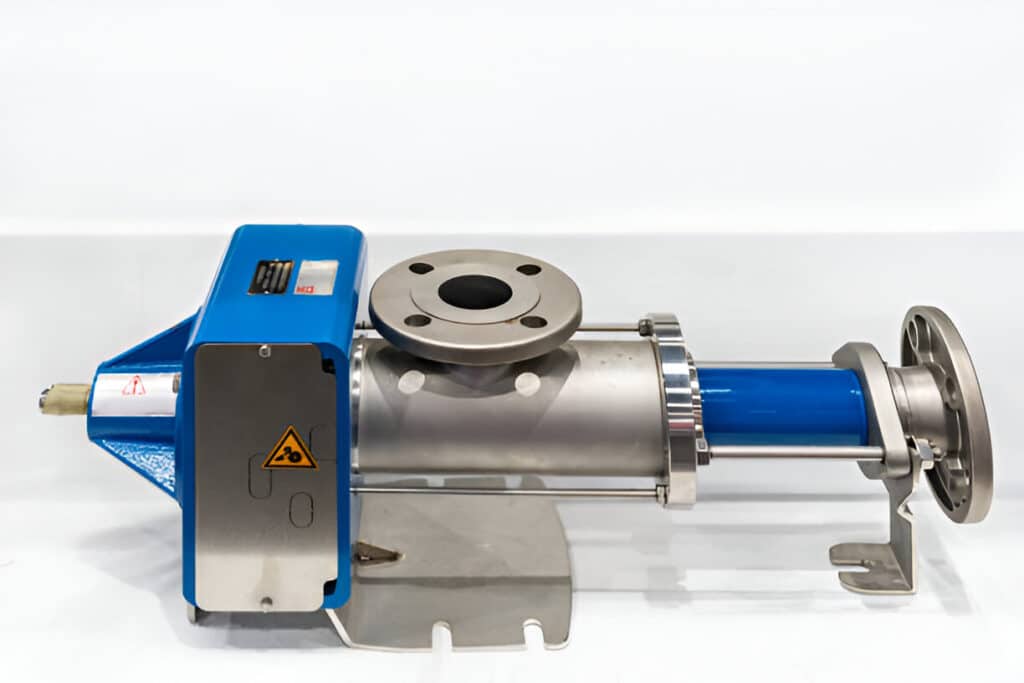
When to Use Progressive Cavity Pumps
Viscosity
Progressive cavity pumps are capable of handling fluids with a wide range of viscosities, from low to extremely high. The pump’s unique design allows it to maintain a consistent flow rate regardless of the fluid’s viscosity. This makes progressive cavity pumps ideal for applications involving viscous materials such as slurries, sludges, and thick oils.
The helical rotor and the stator work together to create sealed cavities that progress along the length of the pump, enabling the efficient transfer of viscous fluids without damaging shear-sensitive materials.
Varying Flow
Progressive cavity pumps offer a unique advantage in their ability to handle varying flow rates. The flow rate of a progressive cavity pump can be easily adjusted by changing the rotation speed of the rotor, which is typically controlled by a variable frequency drive.
This feature makes progressive cavity pumps ideal for applications that require precise dosing or metering of fluids. The ability to accurately control the flow rate also enables these pumps to handle shear-sensitive materials without causing damage to the product.
Moreover, the flow rate of a progressive cavity pump remains constant even when the viscosity of the fluid changes, making them suitable for pumping a wide range of fluids with varying consistencies.
Suction Conditions
Progressive cavity pumps are capable of handling a wide range of suction conditions, including fluids with high viscosity and slurries containing solids. These pumps can generate significant suction lift, allowing them to effectively pump materials from lower levels or even from underground sources.
The suction capabilities of progressive cavity pumps are largely independent of the fluid’s viscosity, making them suitable for applications involving varying viscosities. The unique design of the rotor and stator assembly enables the pump to maintain a consistent flow rate and pressure, even under challenging suction conditions.
Separating Fluids
Progressive cavity pumps excel at separating fluids with varying viscosities and solids content. The unique design of the helical rotor and double-helix stator allows for the efficient handling of challenging materials, such as slurries, sludges, and mixtures with high percentages of solids.
These pumps can effectively separate the liquid and solid components, making them ideal for applications in wastewater treatment, mining, and industrial processes. The progressive cavity pump’s ability to handle a wide range of fluids and maintain consistent flow rates, regardless of viscosity variations, ensures reliable and efficient separation performance.
Abrasive Solids
Progressive cavity pumps are well-suited for handling abrasive solids in fluids. The unique design of the rotor and stator allows for the effective pumping of slurries containing abrasive materials without causing excessive wear on the pump components.
The elastomeric stator provides a resilient surface that can withstand the impact of abrasive particles, while the helical rotor maintains a consistent flow rate even in the presence of solids.
The Difference Between Centrifugal and Progressive Cavity Pumps
Operating Principle
Centrifugal pumps: Centrifugal pumps use rotational energy. They create pressure through velocity.
Progressive cavity pumps: Progressive cavity pumps use positive displacement. They move fluid through cavities created by a rotor.
Flow Characteristics
Centrifugal pumps: Centrifugal pumps handle high flow rates.
Progressive cavity pumps: Progressive cavity pumps excel with viscous fluids.
FAQs
Can Progressive Cavity Pump Run Dry?
Progressive cavity pumps should not run dry as it can cause damage to the stator.
Is a Mono Pump a Progressive Cavity Pump?
Mono Pump is a brand name. It refers to progressive cavity pumps. All Mono Pumps are progressive cavity pumps. Not all progressive cavity pumps are Mono Pumps.
In Conclusion
In conclusion, progressive cavity pumps are versatile and efficient pumping solutions for various applications. Their unique design allows for smooth, pulsation-free flow and the ability to handle a wide range of fluids.
To learn more about how progressive cavity pumps can benefit your specific application, contact a trusted pump supplier today.