Have you ever wondered what slurry seal is and how it’s used in road maintenance? Slurry seal is a cost-effective method for extending the life of asphalt pavements.
It’s a mixture of aggregate (small rocks), asphalt emulsion, water, and additives that is applied to the surface of a road. Slurry seal helps to fill small cracks and protect the underlying pavement from further damage.
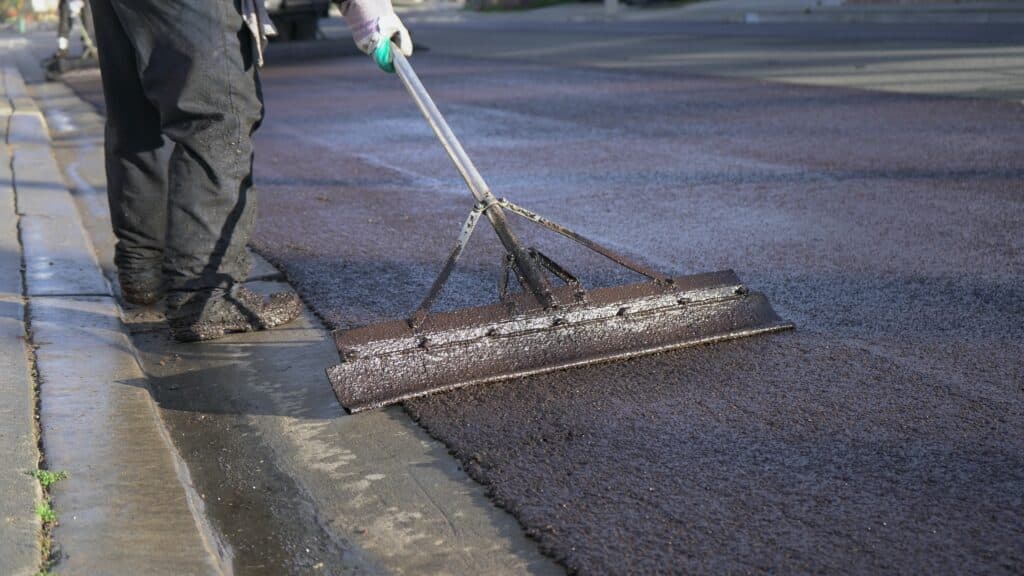
What is Slurry Seal
Slurry seal is a cost-effective pavement maintenance technique that involves applying a mixture of emulsified asphalt, water, aggregate, and additives to the surface of asphalt pavements. This thin, protective layer helps to seal minor cracks, improve skid resistance, and extend the life of the pavement.
Composition and Materials
Slurry seal is composed of several key materials:
- Asphalt emulsion: A mixture of asphalt cement, water, and an emulsifying agent, which serves as the binder for the slurry seal. The emulsion typically contains 6.0–7.0% medium-grade asphalt cement.
- Fine aggregates: Mineral aggregate, such as sand or crushed stone, is used to provide structure and skid resistance to the slurry seal. The aggregate is carefully selected based on its size, shape, and gradation.
- Water: Water is added to the mixture to achieve the desired consistency and to facilitate the mixing and application process.
- Additives and fillers: Various additives, such as advanced polymer additives and anti-oxidation additives, may be incorporated to enhance the performance and durability of the slurry seal. Mineral fillers, like cement or lime, are also used to improve the workability and consistency of the mixture.
Purpose of Slurry Seal
- Preserving and protecting underlying pavement: Forms a protective layer over the asphalt surface, shielding it from water, UV rays, and traffic wear. Extends pavement life by preventing structural damage.
- Sealing minor cracks and preventing water penetration: Fills and seals surface cracks, preventing water intrusion into the subbase. Maintains road integrity and reduces the need for extensive repairs.
- Restoring surface flexibility and texture: Contains asphalt emulsion, aggregate, and polymer additives to restore flexibility and improve texture. Enhances skid resistance for safer driving.
- Providing a new driving surface at lower costs than repaving: Offers a cost-effective alternative to repaving. Improves ride quality and extends pavement life, ideal for residential streets and parking lots.
Types of Slurry Seals
There are three main types of slurry seals: Type I, Type II, and Type III.
Type I (fine)
Type I slurry seal, also known as fine aggregate slurry seal, is a mixture of asphalt emulsion, fine aggregates, mineral filler, and water. This type of slurry seal is ideal for residential streets and parking lots with low traffic volume. The fine aggregates used in Type I slurry seal have a smaller particle size, typically passing through a #4 sieve (4.75 mm).
Type II (general)
Type II slurry seals are commonly used for residential streets and parking lots with low to moderate traffic volume. This slurry seal mixture consists of asphalt emulsion, mineral aggregate, mineral filler, and water, providing a cost-effective preventive maintenance solution.
Type III (coarse)
Type III slurry seal is a coarse mixture of emulsified asphalt, larger aggregate, mineral filler, and water, designed for high-traffic volume roads and streets. This slurry seal treatment provides a thicker protective layer, improving skid resistance and extending the life of the pavement surface.
The coarser aggregate used in Type III slurry seals allows for better resistance to abrasion and heavy traffic loads. Typically containing 6.0–7.0% medium-grade asphalt cement, this cost-effective preventive maintenance technique is ideal for primary and secondary roads, as well as parking lots and industrial areas.
Suitable Pavement Conditions
- Low to Moderate Distress Levels
- Narrow cracks and minor surface irregularities
- Residential Streets, Parking Lots, and Low-Volume Roads
- Not suitable for major structural issues, wide cracks, or severe rutting
Slurry Seal Process
1. Mixing the Slurry
The slurry seal process begins by mixing aggregate, asphalt emulsion, water, and additives in a specialized slurry mixing machine. The proportions of each component are carefully controlled to ensure the desired consistency and performance of the final product.
2. Applying the Slurry
Once the slurry mixture is prepared, it is evenly spread onto the road surface using a spreader box attached to the slurry mixing truck. The spreader box ensures a uniform application thickness, typically between 3/8 to 5/8 inches.
3. Curing and Setting
After application, the slurry seal is allowed to cure and set. This process involves the evaporation of water from the mixture, allowing the asphalt emulsion to break and the aggregate particles to bond together and adhere to the existing road surface.
4. Opening to Traffic
Depending on factors such as ambient temperature, humidity, and the specific slurry seal formulation used, the treated road surface can be opened to traffic within a few hours of application. The result is a renewed, protective layer that extends the life of the pavement.
FAQs
How long does a slurry seal last?
A slurry seal typically lasts 3-5 years. Factors like traffic volume and weather conditions can impact its lifespan.
What is the difference between slurry seal and seal coat?
Slurry seal is a mixture of asphalt emulsion, water, aggregate, and additives. It is thicker than a seal coat. A seal coat is a thin liquid layer of asphalt with little to no aggregate.
How long before you can drive on slurry seal?
Slurry seal usually needs 2-4 hours to cure before being driven on. Temperature and humidity affect curing time. Hotter, drier conditions speed up the process. It’s best to wait 24 hours for optimal results.
How much does slurry seal cost?
Slurry seal costs $0.10 to $0.25 per square foot on average. Factors like location, project size, and contractor rates influence the price. A 1,000-square-foot driveway may cost $100 to $250 to slurry seal.
Can slurry seal be applied in cold weather?
Slurry seal application is weather-dependent and should be applied when temperatures are above 50°F (10°C) and no rain is expected for at least 24 hours after application.
Is slurry seal environmentally friendly?
Slurry seal is considered an eco-friendly paving option as it reduces the need for new asphalt, minimizes waste, and has lower emissions compared to traditional hot-mix asphalt.
Can slurry seal be applied over cracks and potholes?
Slurry seal is not designed to fill large cracks or potholes. These should be repaired before applying the slurry seal to ensure a smooth and even surface.
In Conclusion
In conclusion, slurry seal is a cost-effective and efficient method for maintaining and extending the life of asphalt pavements. It provides a protective layer, fills minor cracks and voids, and improves skid resistance.
Slurry seal is an excellent choice for preserving roads, parking lots, and other asphalt surfaces in good condition.