Bearing failure is a common issue in rotating equipment, leading to costly downtime and repairs.
While both bearing isolators and labyrinth seals aim to protect bearings, many are unsure about their key differences and which one to choose for their specific application.
In this blog post, we’ll dive into the distinct characteristics of bearing isolators and labyrinth seals, covering their primary functions, designs, contact types, materials, costs, and ideal applications, empowering you to make an informed decision for your machinery.
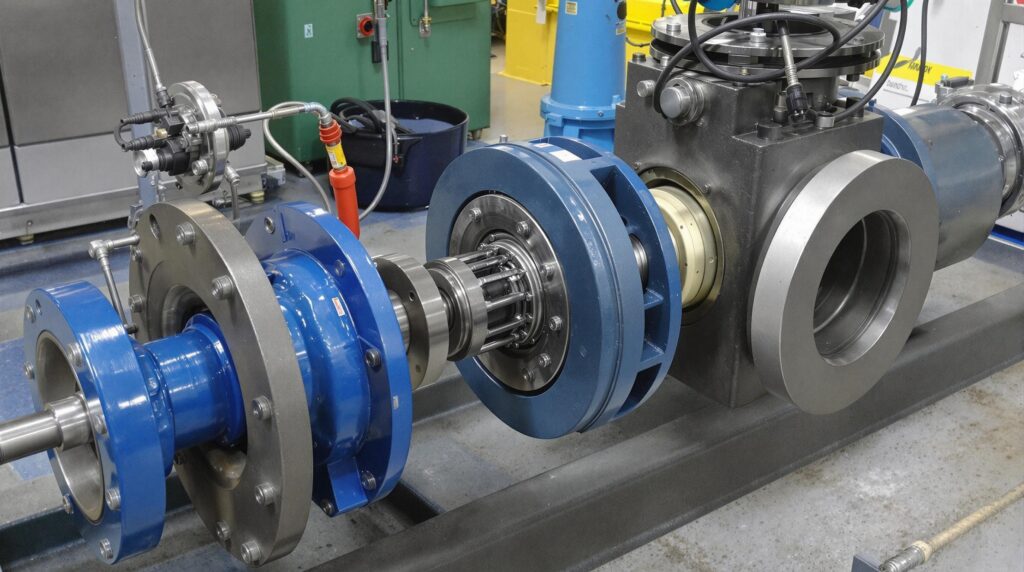
What Is Bearing Isolator
A bearing isolator is a specialized sealing device designed to protect bearings in rotating equipment from contamination and lubrication loss. It consists of a rotor and stator that operate without contact, creating a non-wearing seal. The rotor turns with the rotating shaft, while the stator remains stationary with the bearing housing.
Bearing isolators use centrifugal force and labyrinth paths to prevent contamination ingress and retain lubricant. As the rotor spins, any contamination or lubricant is expelled outwards through the labyrinth paths and drained away.
What Is Labyrinth Seal
A labyrinth seal is a type of mechanical seal that uses a complex maze-like path to prevent leakage or contamination ingress between two spaces. It consists of a series of grooves or chambers that create an extended and tortuous path for any fluids or particles to navigate. This labyrinth path makes it difficult for contamination to work its way through and helps retain lubricant on the desired side of the seal.
The Difference Between Bearing Isolator and Labyrinth Seal
Primary Function
The primary function of a bearing isolator is to protect bearings in rotating equipment from contamination and lubrication loss.
Labyrinth seals are more general purpose seals used to minimize leakage or prevent contamination ingress between any two spaces, not just bearing housings.
Design
Bearing isolators have a more specialized design tailored for bearing protection. They consist of two main parts – a rotor and stator – with the rotor having special features like expeller ports and labyrinth paths to centrifugally remove contamination and retain lubricant.
Labyrinth seals come in more varied configurations, but generally use a series of chambers or grooves to create an arduous path for contamination. Some labyrinth seals can have more basic designs without distinct rotor and stator components.
Contact
Bearing isolators are strictly non-contact seals, with the rotor spinning freely within the stator. This prevents wear, heat generation, and minimizes friction.
While some more advanced labyrinth seals are non-contact, others operate with slight rubbing contact between the maze features and the rotating component. This allows them to better withstand pressure differentials but can cause some wear over time.
Materials
Bearing isolators are typically constructed from metals like bronze, stainless steel, or aluminum to provide durability and chemical resistance.
Labyrinth seals can be made from a wider variety of materials including metals, but also non-metallic options like PTFE, thermoplastics, and elastomers.
Cost
Bearing isolators tend to have a higher upfront cost compared to simple labyrinth seals due to their more specialized design and construction. However, they generally provide a lower lifecycle cost by extending bearing life and reducing maintenance needs.
Basic labyrinth seals can be one of the most economical sealing options, but more advanced non-contact designs can have higher costs more comparable to bearing isolators. Labyrinth seals may require more frequent replacement in challenging environments.
Applications
Bearing isolators are used specifically on rotating equipment where bearing protection is required. This includes motors, pumps, gearboxes, fans, and more. They are commonly found in industries like power generation, oil & gas, food processing, mining, and wastewater treatment.
Labyrinth seals have a wider range of potential applications beyond just bearing protection. They are used for sealing rotating shafts, reciprocating rods, and in both liquid and gas services. Labyrinth seals are found in turbomachinery, compressors, hydraulic systems, and valve stems across many industries.