In the machinery industry, selecting the appropriate materials for seals and gaskets is critical for ensuring optimal performance and longevity. Two commonly used elastomers in this field are FPM (Fluoroelastomer) and EPDM (Ethylene Propylene Diene Monomer).
While both materials offer unique advantages, they differ in their chemical composition, temperature resistance, and compatibility with various media. This blog post will delve into the key distinctions between FPM and EPDM, providing insights to help professionals make informed decisions when choosing between these two elastomers.
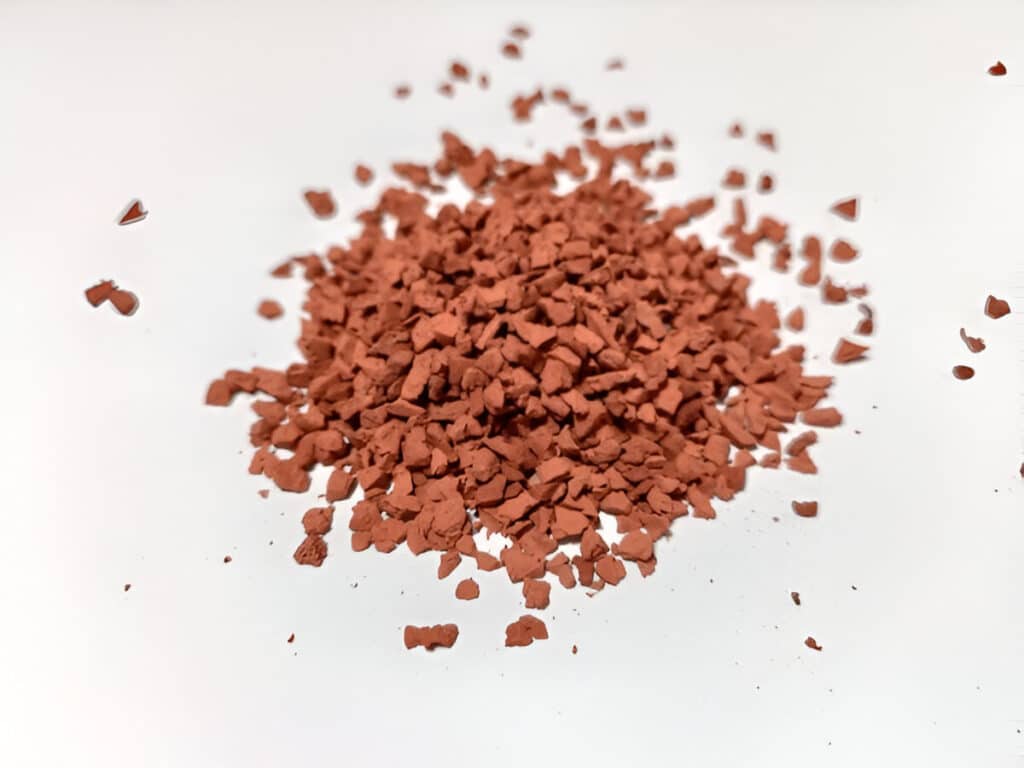
What Is EPDM
EPDM (Ethylene Propylene Diene Monomer) is a synthetic rubber widely used in various applications due to its excellent resistance to heat, ozone, and weather. This versatile elastomer offers a wide operating temperature range from -50°C to 150°C, making it suitable for both low-temperature and high-temperature environments.
The chemical composition of EPDM includes ethylene, propylene, and a diene monomer, which contribute to its unique properties. EPDM exhibits good resistance to polar substances such as water, acids, and bases, as well as steam. However, it has limited resistance to petroleum-based fluids and non-polar solvents.
EPDM finds extensive use in automotive applications, particularly in seals, hoses, and weatherstripping. Its exceptional weather resistance makes it an ideal choice for outdoor applications, such as roofing membranes and window seals. EPDM is also commonly used in the manufacturing of O-rings, static seals, and custom-made seals for various industries.
What Is FPM
FPM (Fluoroelastomer), also known as Viton or Fluoro Rubber, is a high-performance synthetic rubber renowned for its outstanding chemical resistance and thermal stability. Developed by DuPont Performance Elastomers, FPM contains fluorine, which contributes to its unique properties.
The chemical structure of FPM provides excellent resistance to a wide range of aggressive chemicals, including strong acids, bases, aromatic hydrocarbons, and chlorinated solvents. It also exhibits exceptional performance in high-temperature environments, with an operating temperature range from -20°C to 200°C.
FPM’s chemical resistance properties make it a preferred choice for applications in the chemical processing, automotive, and aerospace industries. It is commonly used in the production of O-rings, gaskets, and seals for fuel systems, brake fluids, and aggressive chemical environments.
Key Differences Between FPM and EPDM
Chemical Composition and Structure
FPM, also known as Viton or fluoroelastomer, is a fluorocarbon-based synthetic rubber. Its chemical structure consists of a carbon-fluorine backbone with various fluorinated monomers, such as vinylidene fluoride (VDF), hexafluoropropylene (HFP), and tetrafluoroethylene (TFE).
On the other hand, EPDM is a synthetic rubber composed of ethylene, propylene, and a diene monomer. The diene monomer introduces unsaturation sites in the polymer chain, allowing for vulcanization and improved mechanical properties. EPDM has a saturated backbone, which provides excellent resistance to heat, ozone, and weathering.
Learn more about Chemical resistance of polymers
Physical Properties
FPM exhibits excellent mechanical properties, including high tensile strength, tear resistance, and abrasion resistance. It has a wide operating temperature range, typically from -20°C to +200°C, making it suitable for both low and high-temperature applications. FPM also has low compression set and good elastic recovery, ensuring a tight seal even after prolonged use.
EPDM, in comparison, has good mechanical properties but lower tensile strength and tear resistance compared to FPM. However, EPDM has excellent flexibility, especially at low temperatures, with an operating temperature range from -50°C to +150°C. It also has outstanding resistance to ozone, UV radiation, and weathering, making it ideal for outdoor applications.
Chemical Resistance
One of the key strengths of FPM is its exceptional chemical resistance. It offers excellent resistance to a wide range of aggressive chemicals, including oils, fuels, and aromatic hydrocarbons. FPM also has good resistance to Strong acids, bases, and polar solvents, although its performance may vary depending on the specific chemical and temperature. FPM is a preferred choice for sealing applications in the chemical processing and petroleum industries.
EPDM, while not as chemically resistant as FPM, still offers good resistance to certain chemicals, particularly dilute acids, and bases. It has excellent resistance to alkalis, steam, and polar solvents. However, EPDM is not recommended for use with oils, fuels, and non-polar solvents, as it can swell and degrade over time.
Environmental Resistance
EPDM outperforms FPM in terms of environmental resistance. It has exceptional resistance to ozone, UV radiation, and weathering, making it suitable for extended outdoor use. EPDM can withstand prolonged exposure to sunlight without cracking or deteriorating. It also has excellent resistance to heat and cold, maintaining its flexibility and sealing properties over a wide temperature range.
FPM, while still having good heat resistance, is not as resilient to ozone, UV radiation, and weathering as EPDM. Prolonged exposure to these environmental factors can cause FPM to harden, crack, or lose its sealing properties over time.
Application Suitability
FPM is the preferred choice for sealing applications that involve exposure to aggressive chemicals, high temperatures, and hydrocarbons. It is commonly used in the chemical processing, petroleum, and automotive industries for seals, gaskets, and O-rings.
EPDM is suitable for applications that require excellent resistance to environmental factors, such as ozone, UV radiation, and weathering. It is widely used in the automotive, construction, and appliance industries for static seals, weatherstripping, and hoses. EPDM is also a cost-effective alternative to FPM for applications that do not require extreme chemical resistance.