Lip seals and labyrinth seals are two popular sealing solutions in the machinery industry, but choosing the wrong type can lead to equipment failure, costly downtime and safety hazards. The differences between these seals – including friction, speed limits, temperature range, and contamination resistance – significantly impact their suitability for various applications.
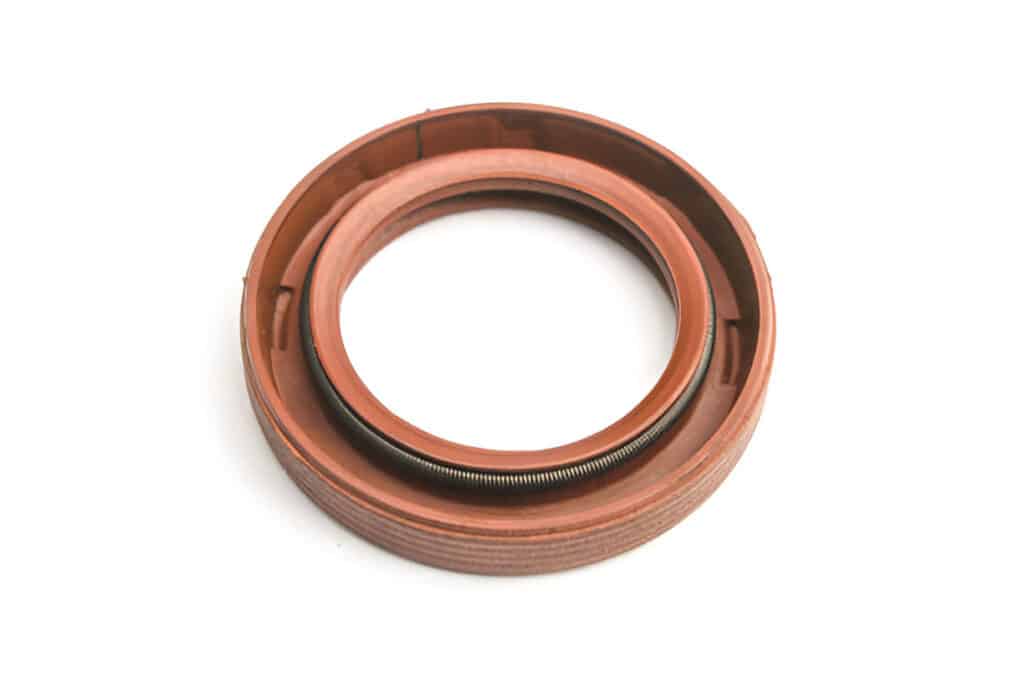
What is a Lip Seal
A lip seal is a type of dynamic shaft seal designed to prevent leakage between a rotating shaft and stationary housing. It consists of a flexible sealing element, typically made of elastomeric materials such as nitrile rubber, silicone, or polyurethane. The sealing element has a lip-shaped profile that maintains constant contact with the rotating shaft surface.
What is a Labyrinth Seal
A labyrinth seal is a non-contacting seal that uses a tortuous path to restrict leakage between rotating and stationary components. Unlike lip seals, labyrinth seals do not rely on physical contact with the shaft surface. Instead, they create a series of chambers and restrictions that make it difficult for the sealed fluid to escape.
Key Differences Between Lip Seals and Labyrinth Seals
Contact
Lip seals maintain direct contact between the sealing lip and the shaft surface to prevent leakage.
Labyrinth seals are non-contacting – they rely on a tight clearance between the labyrinth teeth and shaft to restrict flow without any physical contact.
Friction
The direct contact of lip seals results in higher friction compared to labyrinth seals. This friction can generate heat and lead to higher power consumption.
Labyrinth seals, being non-contacting, produce very minimal friction.
Wear
Due to the constant contact and friction, the sealing lip of lip seals will wear over time, eventually requiring replacement.
Labyrinth seals experience virtually no wear as there is no contact between the seal and shaft.
Speed Limit
Lip seals have a lower speed limit compared to labyrinth seals. High speeds can cause excessive heat generation and accelerated wear in lip seals.
Labyrinth seals are suitable for much higher speeds as they are non-contacting.
Life Expectancy
The life of lip seals is limited by wear of the sealing lip. Depending on operating conditions, lip seals may last from a few thousand to a few tens of thousands of hours.
Labyrinth seals have a much longer life expectancy, often lasting the lifetime of the equipment, as they do not experience wear.
Lubrication
Lip seals require lubrication to reduce friction and wear at the sealing lip. The lubricant also helps carry away heat.
Labyrinth seals do not require any lubrication for operation.
Temperature Range
Lip seals are typically limited to temperatures below 250°F (120°C) due to the limitations of common lip seal materials. Some specialized high-temperature lip seal materials can handle up to 450°F (230°C).
Labyrinth seals can operate at much higher temperatures, even exceeding 1000°F (540°C) with suitable materials.
Contamination Resistance
Lip seals provide excellent exclusion of outside contaminants as long as the sealing lip remains intact. However, lip seal leakage can allow ingress of contaminants.
Labyrinth seals are highly resistant to contamination. Their multiple labyrinth teeth create a tortuous path that effectively blocks contaminants.
Cost
Lip seals are usually lower in initial cost compared to labyrinth seals due to their simpler construction. However, labyrinth seals typically have a lower total cost of ownership considering their longer life and reduced maintenance requirements.
Maintenance
Lip seals require periodic inspection and replacement once the sealing lip wears out.
Labyrinth seals require minimal maintenance beyond ensuring the clearances remain within specification. Clearances may need to be adjusted if significant shaft wear occurs over a long operating period.