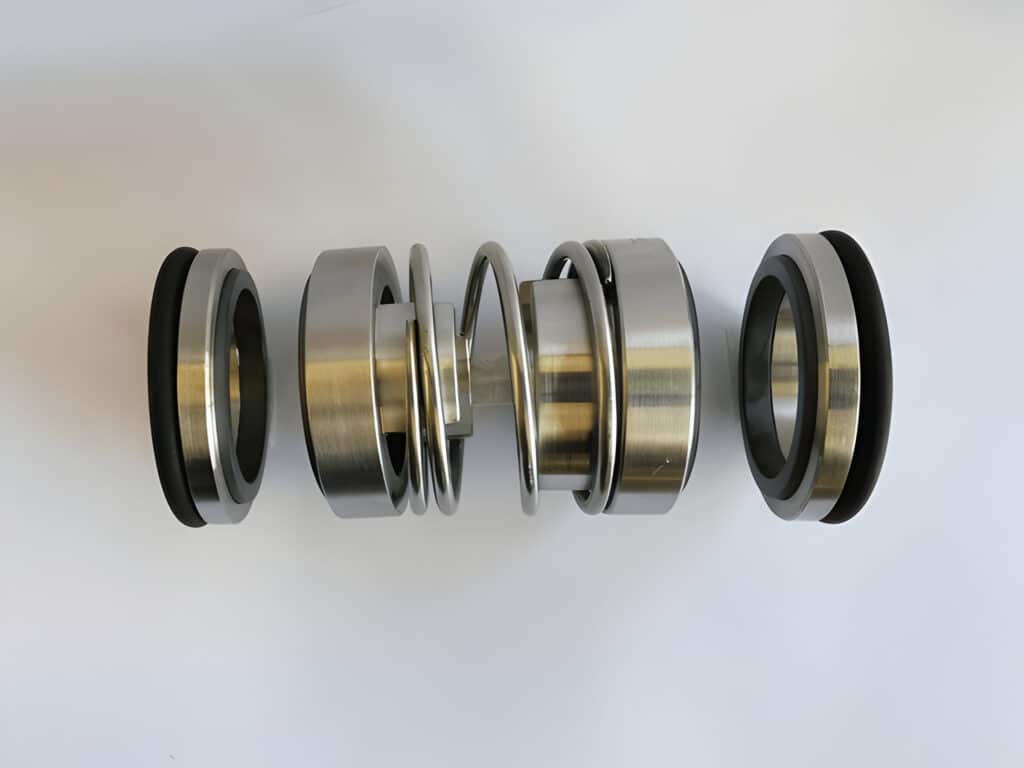
What is Mechanical Seal
A mechanical seal is an essential component in centrifugal pumps and other rotating equipment, providing a dynamic sealing solution between the rotating shaft and stationary housing. Mechanical seals consist of two flat faces, one stationary and one rotating, held together by spring pressure and the sealed fluid’s pressure. The sealing faces are lubricated by a thin liquid film, preventing leakage of fluids while allowing for shaft rotation.
Advantages of Mechanical Seal
- Effective sealing for a wide range of fluids, including hazardous and corrosive liquids
- Relatively simple design and easy to maintain compared to other sealing methods
- Can handle high pressures and temperatures when properly designed and maintained
- Readily available and cost-effective for most applications
- Suitable for a variety of centrifugal pumps and other rotating equipment
Disadvantages of Mechanical Seal
- Require a constant liquid film for lubrication and cooling, making them unsuitable for dry running conditions
- Limited life span due to wear and tear of sealing faces, requiring periodic maintenance and replacement
- Potential for leakage if not properly installed, maintained, or operated outside of design parameters
- May require external flush systems or barrier fluids for certain applications, increasing complexity and cost
- Heat generation due to friction can lead to seal damage and failure if not properly managed
When to Use Mechanical Seal
Mechanical seals are the preferred choice for sealing in most centrifugal pumps and other rotating equipment handling liquids. They are particularly suitable for:
- Applications involving clean, non-abrasive liquids
- Moderate to high-pressure systems
- Processes requiring minimal leakage and environmental impact
- Situations where simplicity and cost-effectiveness are prioritized over other factors
What is Dry Gas Seal
A dry gas seal is a non-contacting, dry-running seal designed specifically for use in centrifugal compressors and other gas processing equipment. Dry gas seals utilize a thin film of gas to create a seal between the rotating and stationary components, eliminating the need for liquid lubrication. The sealing faces feature spiral grooves that generate a lifting force, maintaining a minute gap between the faces and preventing contact during operation.
Advantages of Dry Gas Seal
- Non-contacting design eliminates wear and extends seal life compared to mechanical seals
- Suitable for dry running conditions and high-speed applications, such as in centrifugal compressors
- Significantly lower leakage rates compared to oil seals or other contacting seals
- Reduced maintenance requirements and associated costs over time
- Environmentally friendly, as they do not require oil or other lubricants that could potentially leak
- Can handle a wide range of process gases and operating conditions
Disadvantages of Dry Gas Seal
- Higher initial cost compared to mechanical seals due to more complex design and instrumentation
- Require clean, dry sealing gas for proper operation, which may necessitate additional gas conditioning equipment
- Limited ability to handle liquids or entrained solids in the process gas
- More sensitive to changes in operating conditions, such as pressure, temperature, and gas composition
- Require a more sophisticated seal support system, including buffer gas supply and monitoring equipment
When to Use Dry Gas Seal
Dry gas seals are the preferred sealing solution for centrifugal compressors and other high-speed, dry gas applications. They are particularly well-suited for:
- Natural gas processing, transmission, and storage
- Petrochemical and chemical processing industries
- Applications requiring minimal gas leakage and environmental impact
- High-pressure, high-speed compressor applications where oil contamination is unacceptable
- Situations where long seal life and reduced maintenance are prioritized
FAQs
If the pump is run dry for a few seconds, will it damage the mechanical seal?
Running a pump dry, even for a short period, can cause significant damage to a mechanical seal.
Mechanical seals rely on a thin liquid film between the sealing faces for lubrication and cooling. In the absence of this liquid film, the sealing faces will quickly overheat due to friction, leading to thermal stress, warping, and eventual seal failure. Dry running can also cause the sealing faces to contact each other directly, resulting in excessive wear and damage to the seal surfaces.