What is Seal Support Systems
Seal support systems are auxiliary systems that ensure the proper operation of mechanical seals. They maintain the optimum environment for the seal faces by controlling the fluid around them.
Seal support systems can include a wide range of components, such as barrier fluid reservoirs, gas panels, seal pots, and heat exchangers, all working together to maintain optimal conditions for the mechanical seals.
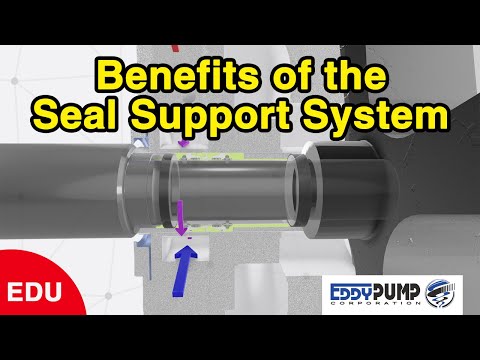
How Do Seal Support Systems Work
Seal support systems work by providing a controlled environment for the mechanical seals, ensuring proper lubrication, cooling, and pressure control. The system circulates a barrier fluid, such as oil, water, or gas, around the seals to keep them cool and lubricated. This barrier fluid also helps to maintain a positive pressure on the inboard seal, preventing process fluid from entering the seal chamber. In dual seal arrangements, the barrier fluid is used to separate the two seals, providing an additional layer of protection against leakage.
The seal support system also helps to remove heat generated by the mechanical seals’ frictional forces. This is typically achieved through the use of heat exchangers, which can be either water-cooled or air-cooled, depending on the application requirements. By maintaining a stable temperature and pressure, the seal support system helps to extend the life of the mechanical seals and prevent premature failure.
What Is the Purpose of Seal Support Systems
The primary purpose of seal support systems is to ensure the reliable and efficient operation of mechanical seals in various industrial applications. These systems help to:
- Prolong seal life by providing proper lubrication and cooling
- Prevent process fluid leakage by maintaining a positive pressure on the inboard seal
- Protect equipment from damage by preventing the ingress of contaminants
- Reduce maintenance costs by minimizing seal failures and extending the time between seal replacements
- Ensure compliance with environmental and safety regulations by controlling emissions and leakage
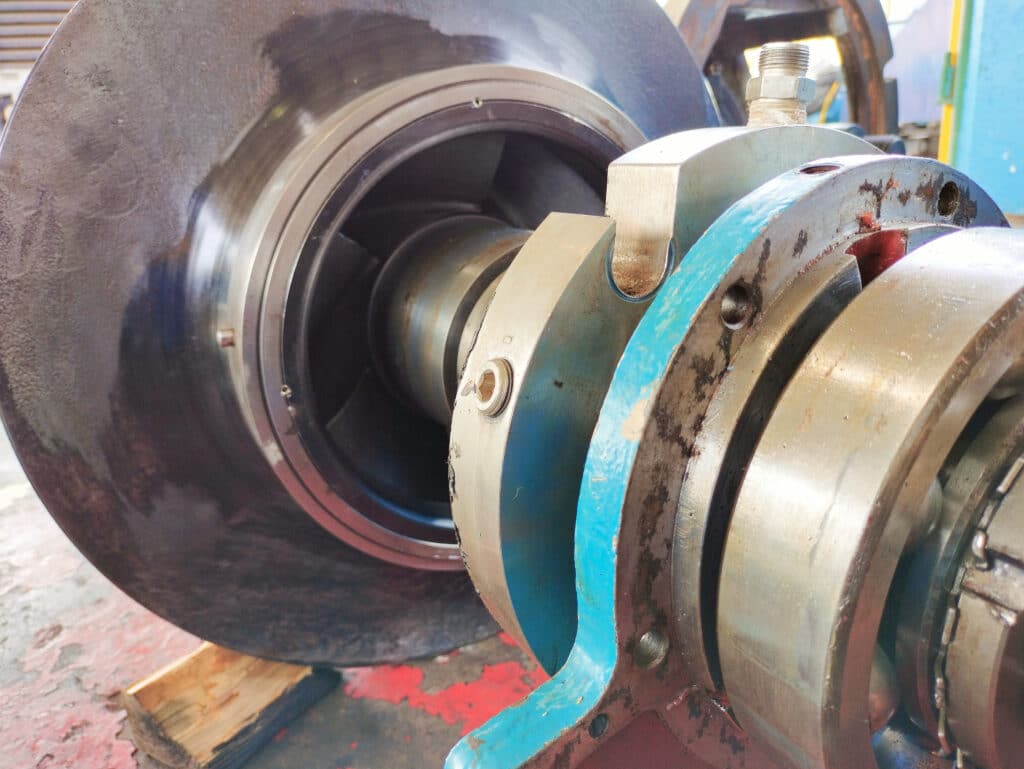
Types of Seal Piping Plans
Seal piping plans, also known as flush plans, are standardized arrangements of seal support systems that define the configuration of piping, instrumentation, and controls for mechanical seals. The American Petroleum Institute (API) has established a series of seal piping plans to provide consistency and reliability across various industries. Some common types of seal piping plans include:
- API Plan 11: This plan uses the process fluid itself to cool and lubricate the seal, with the fluid circulating from the pump discharge to the seal chamber and back to the pump suction.
- API Plan 21: In this plan, a clean, cool fluid from an external source is injected into the seal chamber to provide lubrication and cooling for the seal.
- API Plan 52: This plan utilizes a buffer or barrier fluid reservoir to provide a clean, compatible fluid to the seal chamber. The reservoir is typically pressurized to maintain a positive pressure on the inboard seal.
- API Plan 53A: Similar to Plan 52, this plan uses a barrier fluid reservoir but with the addition of a bladder accumulator to maintain a constant pressure on the barrier fluid.
- API Plan 54: This plan is used for dual seals and involves circulating a barrier fluid between the two seals to provide lubrication and cooling while preventing process fluid leakage.
Types of Flush Plans
Flush plans are critical components of seal support systems, ensuring the proper functioning and longevity of mechanical seals. These plans are designed to provide the necessary lubrication, cooling, and cleaning of the seals, preventing premature failure and leakage. Some common types of flush plans include:
API Plan 62: This plan is used for dual seals and involves injecting a clean buffer gas, such as nitrogen, into the space between the two seals. The gas helps to prevent process fluid leakage and provides a barrier between the seals and the atmosphere.
API Plan 01: In this plan, the process fluid itself is used to cool and flush the seal. The fluid is circulated through the seal chamber without any additional treatment or conditioning.
API Plan 02: This plan involves injecting a clean, external fluid into the seal chamber to provide lubrication and cooling. The fluid is typically supplied from a clean source, such as a plant seal water system.
API Plan 31: This plan uses a cyclone separator to remove particulates from the process fluid before it enters the seal chamber. The cleaned fluid is then used to lubricate and cool the seal.
API Plan 32: Similar to Plan 31, this plan uses a filter to remove contaminants from the process fluid before it is circulated through the seal chamber.