In the world of mechanical seals, hydraulic balance is a fundamental concept that significantly impacts seal performance and longevity. This design principle involves carefully managing the forces acting on the seal faces to optimize pressure handling, minimize wear, and enhance reliability.
In this blog post, we will delve into the intricacies of hydraulic balance in mechanical seals, exploring its definition, the forces at play, and the balance ratio formula. We will also examine the differences between balanced and unbalanced seals, discuss the advantages and disadvantages of hydraulic balance, and explain how this critical balance is achieved in practice.
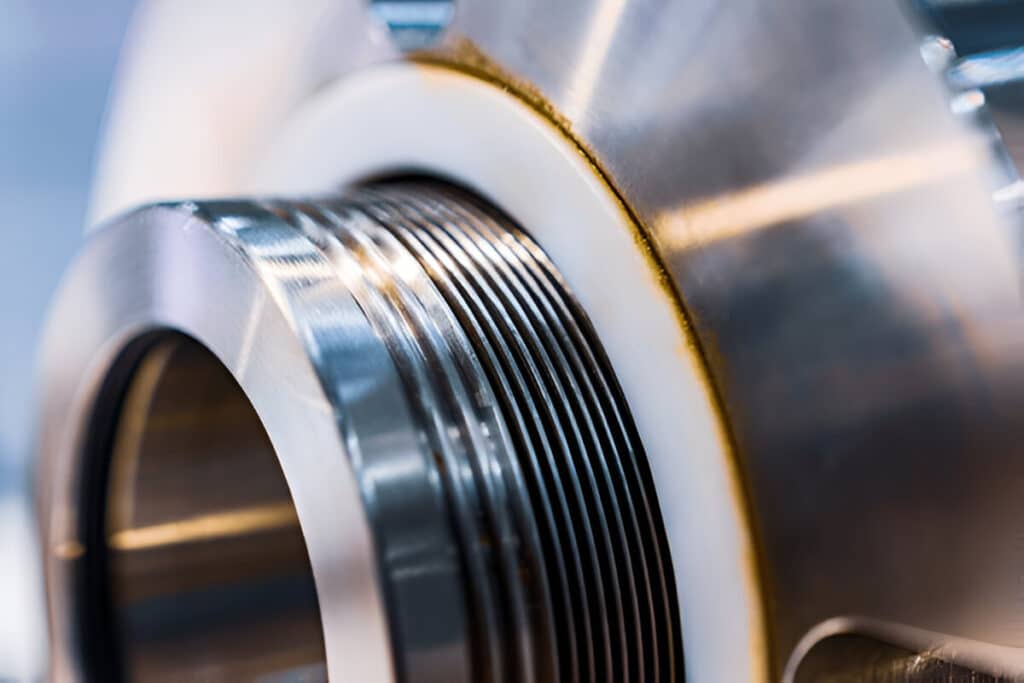
What Is Hydraulic Balance in Mechanical Seals
In a mechanical seal, hydraulic balance refers to the equilibrium between the closing and opening forces acting on the seal faces. This balance determines the contact pressure between the seal faces and influences factors such as wear, heat generation, and pressure handling capability.
Closing Forces
Closing forces in a mechanical seal are the forces that push the seal faces together, creating a tight seal and preventing leakage. The primary closing force is the spring force, which is generated by the mechanical springs behind the seal faces. Additionally, the hydraulic pressure acting on the backside of the seal faces contributes to the closing force. The higher the pressure, the greater the closing force.
Opening Forces
Opening forces in a mechanical seal are the forces that tend to separate the seal faces, counteracting the closing forces. The main opening force is the hydraulic pressure acting on the seal faces. As the sealed fluid pressure increases, it exerts a greater force on the seal faces, trying to push them apart. The seal face geometry and the balance ratio determine the magnitude of the opening force.
Balance Ratio Formula
The balance ratio is a key parameter that quantifies the hydraulic balance of a mechanical seal. It is defined as the ratio of the hydraulic closing force to the hydraulic opening force. The balance ratio can be calculated using the following formula:
Balance Ratio = (Ac – Ao) / Ac
Where:
- Ac is the area of the seal face exposed to the closing pressure
- Ao is the area of the seal face exposed to the opening pressure
A balance ratio of 1 indicates an unbalanced seal, while a ratio less than 1 represents a balanced seal. The lower the balance ratio, the more balanced the seal is.
Differentiation Between Balanced Seals and Unbalanced Seals
Parameter | Balanced Seals | Unbalanced Seals |
---|---|---|
Balance Ratio | < 1 | 1 |
Pressure Handling | High | Low |
Heat Generation | Low | High |
Seal Life | Long | Short |
Design Complexity | High | Low |
Cost | High | Low |
Advantages of Hydraulic Balance
Reducing Wear and Heat Generation
Hydraulically balanced mechanical seals offer significant advantages in terms of reduced wear and heat generation. By equalizing the hydraulic forces acting on the seal faces, the contact pressure between the faces is minimized. This reduction in contact pressure directly translates to less friction and wear, extending the life of the seal faces.
Handling Higher Pressures
Another key benefit of hydraulically balanced seals is their ability to handle higher pressures compared to unbalanced seals. The balanced design allows the seal to operate effectively under increased system pressures without compromising its sealing integrity.
Improving Reliability
Hydraulic balance contributes to the overall reliability and longevity of mechanical seals. By reducing wear, heat generation, and the impact of high pressures, balanced seals are less prone to failure and require less frequent maintenance.
Disadvantages of Hydraulic Balance
Increased Design Complexity
One drawback of hydraulically balanced seals is their increased design complexity compared to unbalanced seals.
This complexity can lead to longer development times and higher initial design costs.
Higher Manufacturing Costs
The increased design complexity of hydraulically balanced seals also translates to higher manufacturing costs. Additionally, balanced seals often incorporate multiple components, such as balance sleeves or hydraulic chambers, which add to the overall cost of the seal assembly.
How Hydraulic Balance Is Achieved
Hydraulic balance in mechanical seals is typically achieved through the use of a balance diameter or a balance chamber. The balance diameter is a carefully designed feature on the seal face that alters the pressure distribution across the face.
By selecting the appropriate balance diameter, the hydraulic forces acting to close the seal faces can be counteracted by the forces acting to open them. This balance of forces results in a net force close to zero, minimizing face contact pressure and wear.
Alternatively, hydraulic balance can be achieved using a balance chamber. In this design, a separate chamber is created behind the seal face, and the system pressure is introduced into this chamber. The pressure in the balance chamber counteracts the hydraulic closing force, effectively balancing the seal.