In mechanical seals, the seal faces are the primary sealing elements that prevent fluid leakage between rotating and stationary components. The materials, geometry, and surface characteristics of these faces directly impact the performance and longevity of the seal.
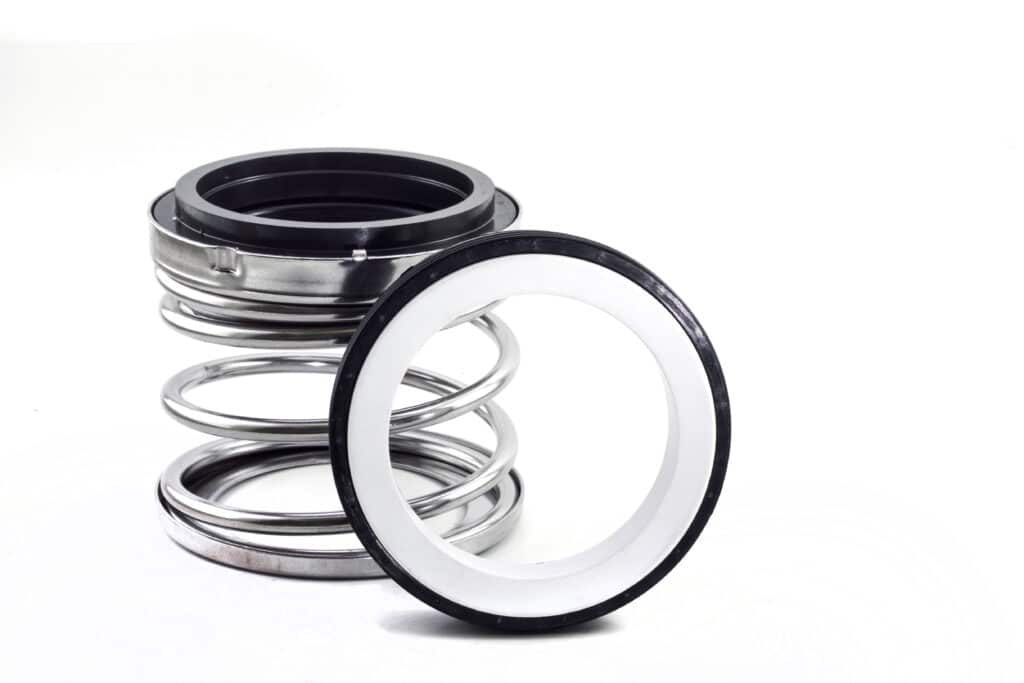
What is the Seal Face
In a mechanical seal assembly, two seal faces are positioned perpendicular to the shaft, with one face typically stationary and the other rotating with the shaft.
Seal faces are precision-manufactured components with highly polished surfaces that create a tight seal when pressed together. The faces are machined to exceptionally flat and smooth finishes, often within a few light bands of flatness.
The seal faces are designed to maintain a small gap between them, typically ranging from 0.1 to 1 micron. This gap is filled with the process fluid, creating a fluid film that prevents direct contact between the faces. The fluid film helps to minimize wear, reduce friction, and dissipate heat generated during operation.
Types of Seal Faces
Flat vs. Specially Treated Faces
Flat seal faces are the most common type used in mechanical seals. These faces are precision-machined to ensure a smooth, flat surface that allows for optimal sealing performance. Flat faces are typically used in applications with moderate to low pressure and temperature requirements.
In contrast, specially treated seal faces undergo additional surface treatments to enhance their performance and durability. Some common surface treatments include:
- Lapping: A fine abrasive process that improves surface finish and flatness.
- Polishing: A process that reduces surface roughness and increases the face’s reflectivity.
- Coatings: Applying specialized coatings, such as diamond-like carbon (DLC) or tungsten carbide, to improve wear resistance and reduce friction.
Specially treated faces are often used in demanding applications with high pressure, temperature, or corrosive media, as they offer superior performance compared to flat faces.
Rotating vs. Stationary Faces
In a mechanical seal, one seal face is typically stationary, while the other rotates with the shaft. The stationary face is usually mounted in the seal gland or housing, while the rotating face is attached to the shaft or shaft sleeve.
The stationary face remains fixed in position and is often made from a harder, more wear-resistant material, such as silicon carbide or tungsten carbide. This face acts as the primary sealing surface, maintaining a tight seal against the rotating face.
The rotating face, on the other hand, is typically made from a slightly softer material, such as carbon graphite or silicon carbide. This allows the rotating face to conform to the stationary face, creating a more effective seal. The rotating face is spring-loaded to maintain constant contact with the stationary face, even under varying operating conditions.
Materials Used in Seal Faces
Material | Properties | Applications |
---|---|---|
Carbon Graphite | – Self-lubricating – Good thermal conductivity – Resistant to thermal shock – Brittle | – Water and other aqueous solutions – Low viscosity fluids – High temperature applications |
Silicon Carbide (SiC) | – Extremely hard – Wear resistant – Chemically inert – High thermal conductivity | – Abrasive and corrosive fluids – High pressure applications – Oil and gas industry |
Tungsten Carbide (WC) | – Very hard – Wear resistant – High thermal conductivity – Good corrosion resistance | – Abrasive and corrosive fluids – High pressure applications – Oil and gas industry |
Alumina Ceramic (Al2O3) | – Hard and wear resistant – Chemically inert – Electrically insulating – Brittle | – Corrosive fluids – High temperature applications – Electrical insulation required |
Stainless Steel | – Corrosion resistant – Tough and ductile – Relatively soft compared to other seal face materials | – Non-corrosive fluids – Low to moderate pressure applications – Food and pharmaceutical industries |
Bronze | – Good lubricity – Moderate wear resistance – Relatively soft compared to other seal face materials | – Low pressure applications – Non-corrosive fluids – Backup rings and throttle bushings |
What is the Face Gap of a Mechanical Seal
The face gap, also known as the fluid film thickness, is the microscopic space between the rotating and stationary faces of a mechanical seal. This gap is typically measured in microns (μm) and plays a critical role in the proper functioning of the seal. The face gap allows a thin film of the sealed fluid to enter and lubricate the sealing surfaces, reducing friction and wear.
In a properly functioning mechanical seal, the face gap remains stable and consistent, maintaining an optimal thickness for lubrication without allowing excessive leakage.
The seal faces are lapped to a high degree of flatness, typically within 2 to 3 helium light bands (0.58 to 0.87 μm), to ensure a uniform gap. The spring force and hydraulic pressure acting on the seal faces help maintain the optimal face gap during operation.