Stuffing box pressure is a critical parameter in the operation and performance of mechanical seals in pumps and other rotating equipment. Maintaining the optimal stuffing box pressure ensures the proper functioning of mechanical seals, prevents leakage, and extends the life of the sealing components.
In this blog post, we will dive into the concept of stuffing box pressure, exploring its definition, influencing factors, typical ranges, and the formula for calculating it. We will also discuss the significance of stuffing box pressure for mechanical seals, potential issues arising from improper pressure management, and methods to control and adjust the pressure effectively.
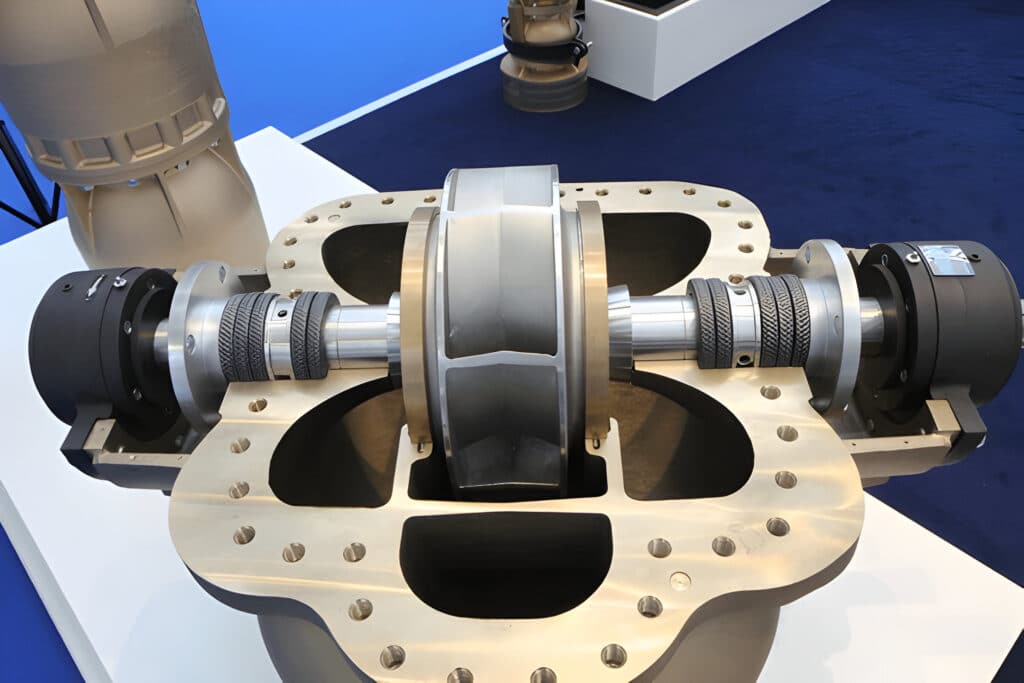
What Is Stuffing Box Pressure
In a centrifugal pump, the stuffing box is a cylindrical space located between the pump casing and the rotating shaft, housing the mechanical seal or packing. Stuffing box pressure refers to the fluid pressure present within this space during pump operation.
The stuffing box pressure is a critical parameter in the proper functioning and longevity of mechanical seals. It affects the seal face lubrication, cooling, and the ability to maintain a liquid film between the stationary and rotating seal faces. Insufficient stuffing box pressure can lead to inadequate lubrication and cooling, resulting in premature seal failure due to increased friction and heat generation.
On the other hand, excessive stuffing box pressure can cause the mechanical seal faces to separate, leading to increased leakage and reduced sealing effectiveness. High pressure can also result in accelerated wear of the seal faces and other components, shortening the overall seal life.
Factors Affecting Stuffing Box Pressure
Pump Design
The design of the pump, particularly the location of the seal chamber and its proximity to the impeller, affects the stuffing box pressure. The closer the seal chamber is to the impeller, the higher the pressure will be due to the influence of the impeller’s centrifugal force.
Suction and Discharge Pressures
The pump’s suction and discharge pressures directly impact the stuffing box pressure. In general, higher suction and discharge pressures result in increased stuffing box pressure. The pressure differential between the suction and discharge sides of the pump also influences the stuffing box pressure.
Presence of Balance Holes or Wear Rings
The presence of balance holes or wear rings in the pump can significantly affect the stuffing box pressure. Balance holes are small openings that allow fluid to flow from the high-pressure side of the impeller to the low-pressure side, helping to equalize pressure and reduce axial thrust on the impeller.
Wear rings, on the other hand, are replaceable rings installed between the impeller and the pump casing to minimize leakage from the high-pressure side to the low-pressure side. The presence of balance holes or wear rings can help maintain a more consistent stuffing box pressure.
Fluid Properties
The properties of the fluid being pumped, such as its viscosity and temperature, can influence the stuffing box pressure. Higher viscosity fluids tend to create higher pressures within the stuffing box due to increased resistance to flow. Similarly, elevated fluid temperatures can lead to increased pressures as the fluid expands and its viscosity decreases.
Typical Ranges of Stuffing Box Pressure
Pump Type | Typical Stuffing Box Pressure Range |
---|---|
Single Stage, End Suction | 10-20 psi (0.7-1.4 bar) |
Single Stage, Double Suction | 15-30 psi (1.0-2.1 bar) |
Multistage, Horizontal | 20-50 psi (1.4-3.4 bar) |
Multistage, Vertical | 30-60 psi (2.1-4.1 bar) |
Stuffing Box Pressure Formula
The stuffing box pressure can be calculated using the following formula:
P_sb = P_s + (P_d – P_s) × k
Where:
- P_sb = Stuffing box pressure
- P_s = Suction pressure
- P_d = Discharge pressure
- k = Constant (typically 0.4-0.6, depending on pump design and balance holes/wear rings)
Functions of Stuffing Box Pressure for Mechanical Seals
- Maintains lubricating fluid film: Appropriate stuffing box pressure ensures an adequate fluid film between the seal faces, reducing friction and wear.
- Prevents fluid vaporization: Sufficient pressure keeps the sealed fluid from vaporizing at the seal faces, avoiding cavitation damage and seal failure.
- Enables proper seal face tracking: Balanced pressure allows the seal faces to maintain proper contact and tracking, preventing leakage and premature wear.
- Facilitates heat dissipation: Proper pressure promotes fluid circulation, helping dissipate heat generated by seal face friction.
Potential Issues Caused by Improper Pressure Management
Failure to maintain appropriate stuffing box pressure can lead to various problems, including:
- Excessive leakage: Low pressure can cause the seal faces to open, resulting in fluid leakage and reduced sealing efficiency.
- Premature seal wear: Insufficient pressure can lead to increased friction and wear between the seal faces, shortening seal life.
- Seal face damage: Elevated pressure can cause the seal faces to close too tightly, leading to excessive heat generation and potential thermal cracking or damage.
- Cavitation and fluid vaporization: Inadequate pressure may allow the sealed fluid to vaporize at the seal faces, causing cavitation damage and seal failure.
Methods to Control or Adjust Stuffing Box Pressure
Using Balance Holes or Back Wear Rings
Balance holes or back wear rings can be incorporated into the seal design to help regulate stuffing box pressure. These features allow a controlled amount of high-pressure fluid to flow from the discharge side to the stuffing box, counteracting the pressure differential across the seal faces. By effectively balancing the pressure, these design elements help maintain proper seal face contact and reduce wear.
Installing External Flush Systems
External flush systems can be used to introduce a clean, compatible fluid into the stuffing box at a controlled pressure. This flushing fluid helps maintain the required pressure in the stuffing box, while also providing cooling and lubrication to the seal faces. External flush systems are particularly beneficial when dealing with abrasive, corrosive, or high-temperature fluids that could otherwise damage the seal faces or cause premature failure.