What is API Plan 11
API Plan 11 is a simple method for managing the fluid that lubricates and cools a mechanical seal in a pump or other rotating equipment.
In this plan, the seal chamber is connected to a tank or reservoir that holds the seal fluid. The fluid flows from the tank into the seal chamber, providing lubrication and cooling for the seal faces. As the equipment operates, the used fluid flows back out of the seal chamber and returns to the tank.
API Plan 11 is a very simple and reliable method for seal lubrication and cooling. It doesn’t require any additional equipment like coolers or filters, making it inexpensive and easy to implement. However, it only works well when the pumped fluid is clean, non-abrasive, and compatible with the seal materials.
How Does API Plan 11 Work
In API Plan 11, the fluid that lubricates and cools the seal is taken from the pump discharge (outlet) and piped to the seal chamber. The seal chamber is the space around the seal where the lubricating fluid collects.
The pressure generated by the pump pushes a small amount of the pumped fluid through the piping and into the seal chamber. This constant flow of fresh, clean fluid from the pump discharge keeps the seal faces lubricated and helps carry away any heat generated by friction.
The fluid that enters the seal chamber then leaks past the seal faces and back into the pump casing, where it mixes with the main flow of pumped fluid. This leakage is normal and necessary for the seal to function properly.
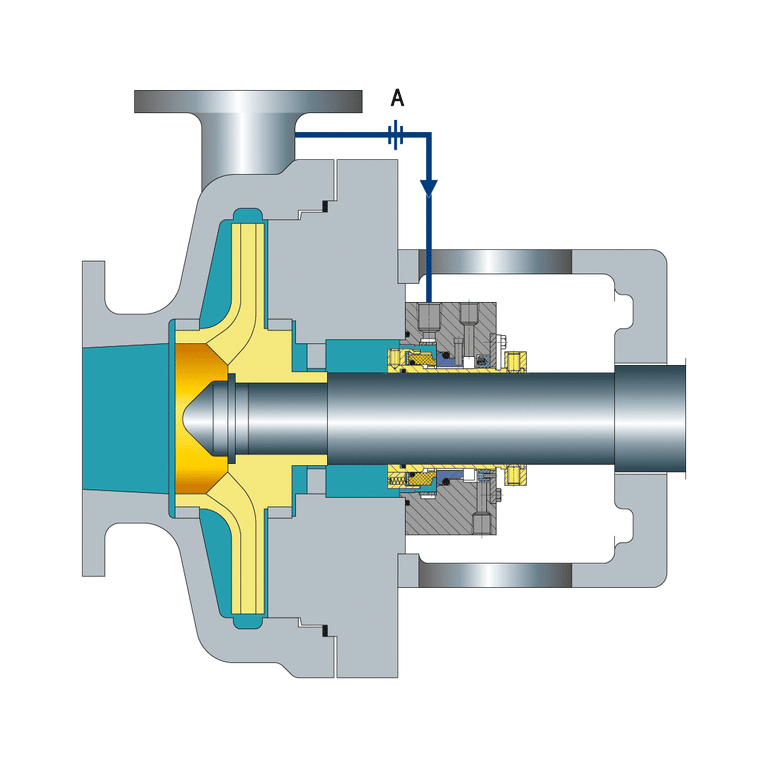
Design of API Plan 11
The basic idea behind API Plan 11 is to allow the sealed fluid to flow through the seal chamber. This helps cool the seal and flush away any contaminants or debris. The flow is maintained by the pressure differential between the seal chamber and the pump discharge.
To set up an API Plan 11 system, you’ll need the following key components:
- Seal Chamber: Features inlet and outlet ports, with the inlet at the bottom and the outlet at the top for optimal flow management.
- Throttle Bushing: Installed in the outlet port to maintain a pressure differential and ensure adequate flow, with size dependent on various operating factors.
- Piping: Connects the chamber ports to the pump’s suction and discharge, facilitating flow and pressure management.
When designing an API Plan 11 system, there are a few key considerations:
- Seal Chamber and Piping Sizing: Ensure they are sized to handle expected flow rates and pressure drops without causing erosion or excessive pressure drops.
- Material Selection: Choose materials for the seal chamber, throttle bushing, and piping that are compatible with operating conditions and the sealed fluid, focusing on corrosion resistance, temperature limits, and pressure ratings.
- Piping Layout: Design the layout to avoid air pockets and dead legs, using smooth bends and minimal fittings to reduce pressure losses.
- Instrumentation: Add pressure gauges or flow meters to monitor system performance and identify potential issues.
Advantages of API Plan 11
- Simplicity: Easy to install, operate, and maintain, the system consists of a seal chamber connected to the pump’s discharge line.
- Cost-effectiveness: Utilizes pumped fluid for lubrication and cooling, reducing the need for additional equipment and lowering costs.
- Reliability: Continuously flushes the seal chamber with fresh fluid, preventing contaminant buildup and prolonging seal life.
- Versatility: Suitable for a wide range of applications and fluids, making it a preferred choice in many industries.
Disadvantages of API Plan 11
- High Water Consumption: Plan 11 diverts a significant amount of process fluid to flush the seal, increasing costs in high-flow or costly fluid systems.
- Contamination Risk: Impurities from the process fluid can directly reach the seal faces, increasing wear and reducing seal life.
- Pressure Fluctuations: Flush flow varies with pump pressure, causing inconsistent seal flushing and potential air entry into the seal during low pressure.
- Poor Lubrication: Unsuitable for fluids with poor lubricating properties, leading to increased friction and heat at the seal faces.
- Lack of Control: No external control over flush rate or temperature; flush fluid’s temperature matches the process fluid, potentially causing issues.
Applications
- Centrifugal Pumps
- Mixers and Agitators
- Compressors
- Barrier Fluid Backup