Choosing the right pump is critical for efficient fluid handling in numerous industrial applications. Selecting between centrifugal and diaphragm pumps can be challenging, given their distinct mechanisms and performance characteristics.
This blog post offers a comprehensive comparison, detailing each pump type, their strengths, weaknesses, and optimal uses. We’ll explore key differences in flow rate, fluid handling, maintenance, and cost. We will also provide guidance on how to select the right pump for specific operational needs.
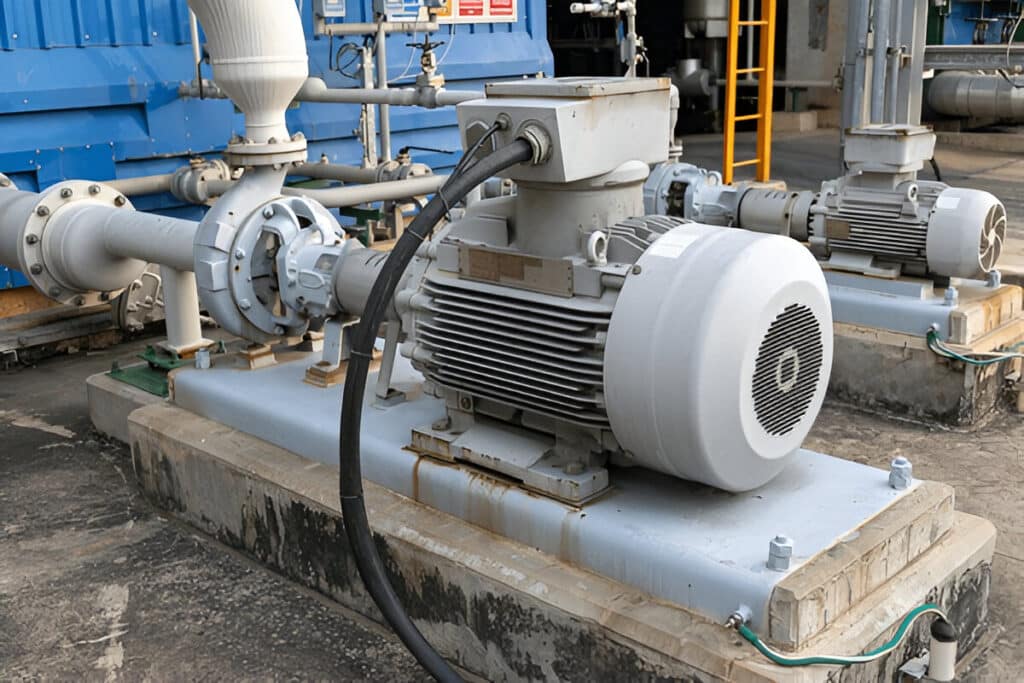
What Is a Centrifugal Pump
A centrifugal pump is a dynamic pump that uses a rotating impeller to move fluids. The impeller, with its curved vanes, increases the fluid’s velocity and pressure, causing it to flow through the pump and into the discharge pipe. These pumps are known for their high flow rates and relatively consistent output, making them ideal for many industrial and commercial uses.
Advantages of Centrifugal Pumps
- Higher Flow Rates: Centrifugal pumps can achieve significantly higher flow rates than diaphragm pumps, making them suitable for applications requiring large volumes of fluid movement.
- Consistent Flow: They provide a smooth, continuous flow of fluid, which is preferred in processes where a steady stream is essential.
- Simpler Design: The design of centrifugal pumps is generally simpler with fewer parts, which can result in easier maintenance and lower costs.
- Cost-Effective for High Volumes: For large-scale applications, centrifugal pumps are often more cost-effective due to their efficiency and long service life.
- Efficient for Low Viscosity Fluids: They operate very efficiently with low-viscosity fluids such as water or light oils.
Disadvantages of Centrifugal Pumps
- Lower Pressure Output: Centrifugal pumps have limited pressure-generating capabilities compared to diaphragm pumps, especially when dealing with viscous fluids.
- Not Suitable for Abrasive or Corrosive Fluids: The close tolerances and mechanical seals can be quickly damaged by abrasive fluids, and corrosive fluids can cause significant issues.
- Loss of Prime: Centrifugal pumps need to be primed before operation, meaning they cannot handle air or gas. Losing prime can cause the pump to stop working.
- Inefficient at Low Flow Rates: These pumps may become inefficient at very low flow rates, causing energy waste and overheating.
- Difficult to Meter Flow Precisely: Centrifugal pumps are not ideal for precise metering applications due to fluctuations in flow rates when external conditions change.
Applications of Centrifugal Pumps
- Water Supply and Distribution: They are commonly used in municipal water systems, irrigation, and building services.
- HVAC Systems: Centrifugal pumps circulate chilled water and hot water in heating and cooling systems.
- Chemical Processing: They are used for handling chemicals that are non-abrasive and non-corrosive.
- Petroleum Industry: These pumps are used to move various fluids, such as light oils, in the petroleum industry.
- Power Plants: Centrifugal pumps play a vital role in cooling systems and feeding water to boilers.
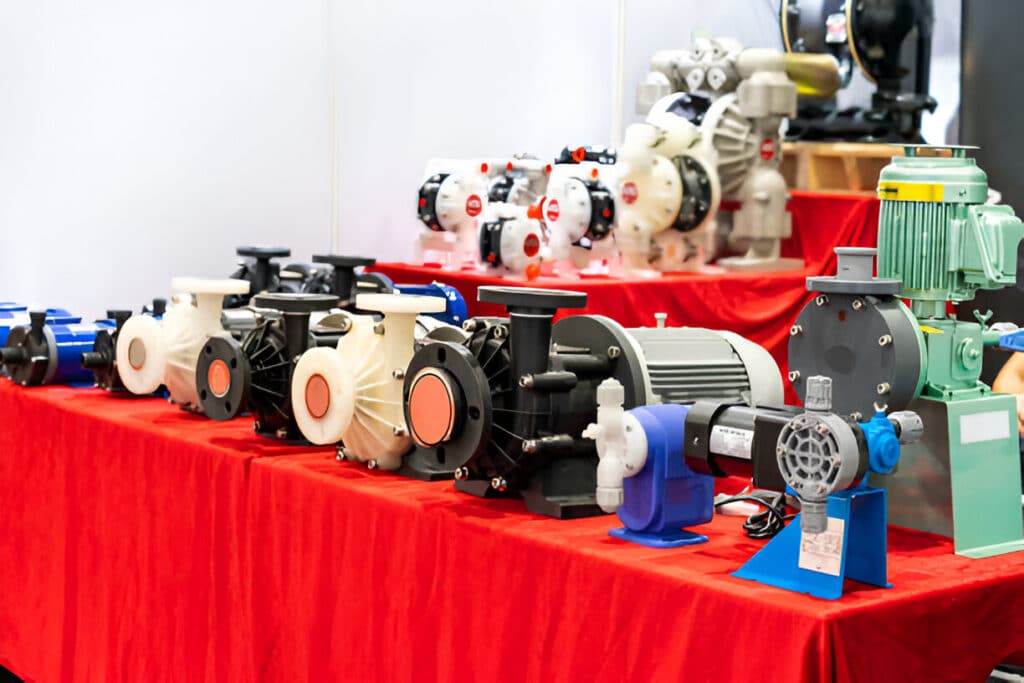
What Is a Diaphragm Pump
A diaphragm pump is a positive displacement pump that uses a flexible diaphragm to move fluids. The diaphragm is driven by a piston, compressed air, or hydraulic fluid, creating a reciprocating motion that draws fluid into and pushes it out of the pump chamber. Diaphragm pumps are known for their ability to handle a wide range of fluids, including viscous, abrasive, and corrosive materials, and their capability to run dry without damage.
Advantages of Diaphragm Pumps
- Self-Priming: Diaphragm pumps are self-priming, meaning they can start pumping even when filled with air.
- Ability to Handle Viscous and Abrasive Fluids: The flexible diaphragm allows these pumps to handle fluids with high viscosity and those with abrasive particles without damage.
- Handles Corrosive Fluids: These pumps can be constructed using materials that are compatible with corrosive chemicals.
- Can Run Dry: Diaphragm pumps can run without liquid and not cause damage to the pump.
- Precise Flow Control: They offer precise flow control and accurate metering.
Disadvantages of Diaphragm Pumps
- Lower Flow Rates: Diaphragm pumps generally have lower flow rates compared to centrifugal pumps.
- Pulsating Flow: They create a pulsating flow due to the reciprocating motion of the diaphragm, which may require additional dampening equipment.
- More Complex Design: Diaphragm pumps have a more complex design with more moving parts, which increases maintenance requirements.
- Higher Initial Cost: Diaphragm pumps tend to have a higher initial cost.
- More Maintenance: Due to the higher complexity of their design and more moving parts, diaphragm pumps typically require more maintenance than centrifugal pumps.
Applications of Diaphragm Pumps
- Chemical Processing: They are widely used in the chemical industry for handling corrosive and abrasive materials.
- Wastewater Treatment: Diaphragm pumps are used to transfer sludge and other thick fluids in wastewater treatment plants.
- Food and Beverage Industry: They handle viscous materials like syrups, pastes, and food slurries.
- Pharmaceutical Industry: These pumps are used for transferring and metering pharmaceutical solutions with precision.
- Mining: They are used for handling abrasive slurries and corrosive liquids in mining operations.
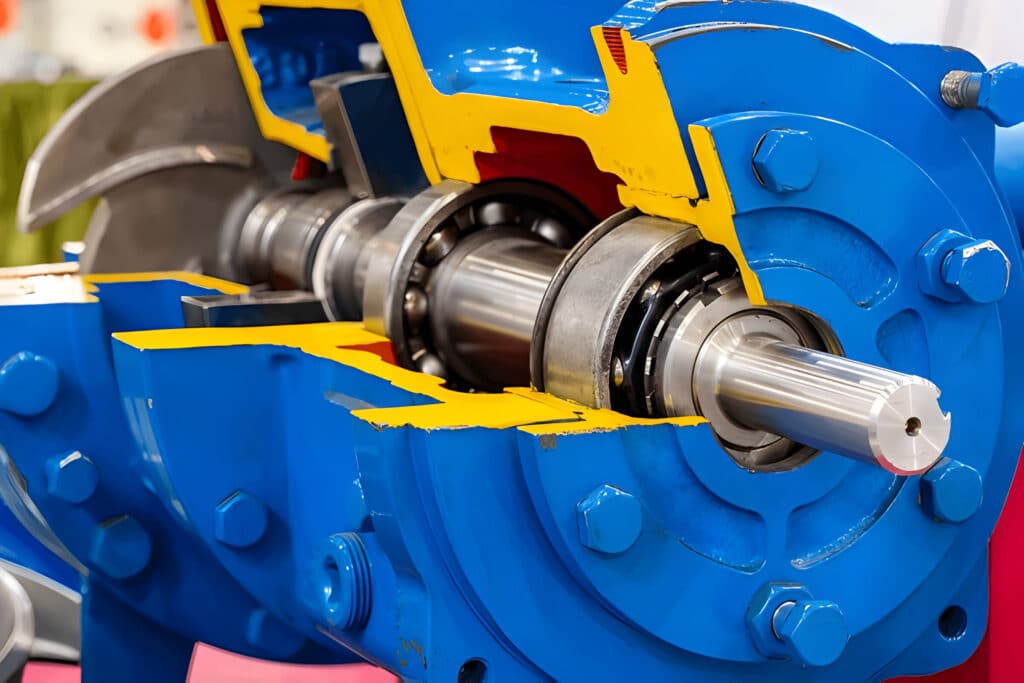
Key Differences Between Centrifugal and Diaphragm Pumps
- Flow Rate and Pressure:
- Centrifugal pumps are better for high flow rates at lower pressures.
- Diaphragm pumps are better for lower flow rates at higher pressures.
- Centrifugal pumps have a flow rate that varies depending on pressure level, while diaphragm pumps provide a constant flow rate.
- Fluid Handling:
- Centrifugal pumps are best for low-viscosity fluids, such as water, solvents, certain chemicals and light oils.
- Diaphragm pumps are best for viscous, abrasive, and shear-sensitive fluids, like heavy oils, wastewater, slurries, and corrosive materials.
- Priming:
- Centrifugal pumps require priming.
- Diaphragm pumps are self-priming.
- Maintenance and Complexity:
- Centrifugal pumps are simpler, with fewer moving parts, and have lower maintenance requirements.
- Diaphragm pumps have a more complex design and require more frequent maintenance.
- Ability to Run Dry:
- Centrifugal pumps cannot run dry without causing damage.
- Diaphragm pumps can run dry without issues.
- Operational Considerations:
- Centrifugal pumps have a narrow optimum operating range.
- Diaphragm pumps offer more flexibility in varying flow and pressure.
- Cost:
- Centrifugal pumps are generally more cost-effective to purchase.
- Diaphragm pumps tend to be more expensive.
- Noise and Vibration:
- Centrifugal pumps generally operate with less noise and vibration.
- Diaphragm pumps may produce noticeable pulsations and vibrations.
- Energy Consumption Analysis:
- Centrifugal pumps are more energy-efficient for high-flow, low-viscosity applications.
- Diaphragm pumps may be less energy-efficient for higher flow applications.
- Pulsation Dampening:
- Centrifugal pumps deliver a smooth, pulseless flow.
- Diaphragm pumps generate a pulsating flow, which may require pulsation dampeners in certain applications.
How to Choose the Right Pump
Selecting the correct pump depends on your specific requirements. Consider the following factors:
- Fluid Viscosity and Type:
- For low-viscosity fluids, choose a centrifugal pump.
- For high-viscosity, abrasive, or shear-sensitive fluids, choose a diaphragm pump.
- Required Flow Rate and Pressure:
- If you need high flow rates at lower pressures, choose a centrifugal pump.
- If you need lower flow rates at higher pressures, choose a diaphragm pump.
- Application Requirements:
- Consider whether the pump needs to be self-priming or run dry.
- Consider the nature of the liquid (e.g., chemical, food-grade, or water).
- Maintenance Capabilities:
- If you need a pump with minimal maintenance, choose a centrifugal pump.
- If you can perform regular maintenance, a diaphragm pump may be suitable.
- Budget Constraints:
- If you are on a tight budget, a centrifugal pump may be more cost-effective.