Was verursacht Pumpenvibrationen? Übermäßige Vibrationen in Pumpen können zu Leistungseinbußen, erhöhten Wartungskosten und sogar zum Totalausfall führen.
In diesem Blogbeitrag untersuchen wir die Hauptfaktoren, die zu Pumpenvibrationen beitragen, und bieten Ihnen praktische Einblicke, um diese Probleme wirksam zu identifizieren und zu beheben.
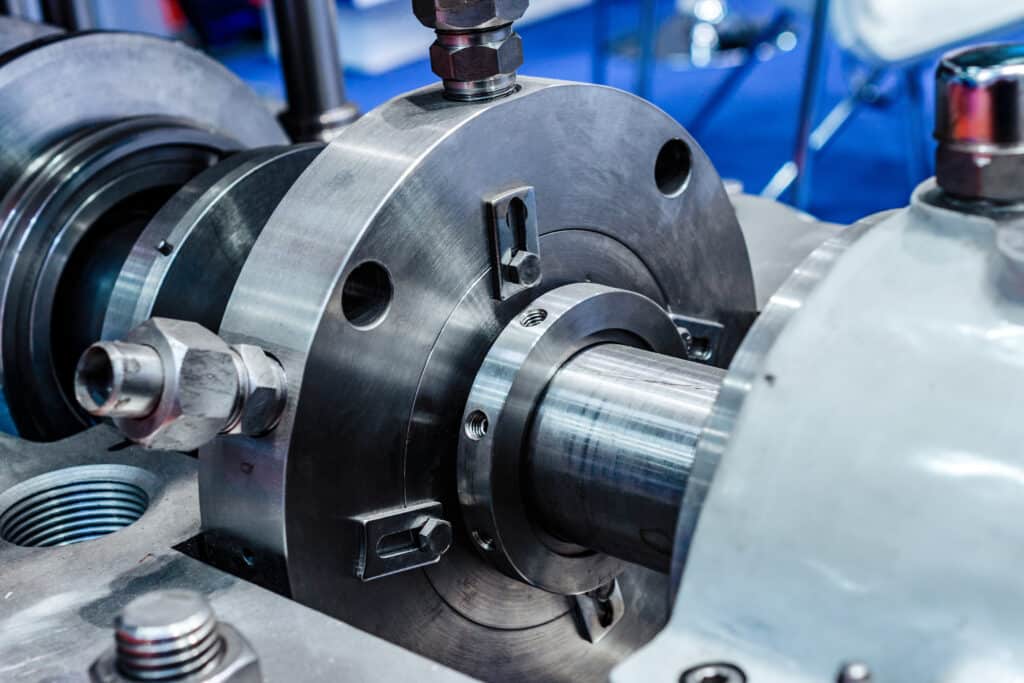
Mechanische Ursachen für Pumpenvibrationen
1. Rotorunwucht
Statisches und dynamisches Ungleichgewicht
Die Rotorunwucht, eine häufige Ursache übermäßiger Vibrationen bei Kreiselpumpen, kann als statisch oder dynamisch klassifiziert werden.
Eine statische Unwucht tritt auf, wenn der Schwerpunkt von der Rotationsachse versetzt ist, wodurch auf den Rotor eine Nettokraft wirkt.
Eine dynamische Unwucht entsteht dagegen, wenn die Hauptträgheitsachse nicht mit der Rotationsachse ausgerichtet ist, sodass ein Nettopaar entsteht.
Ursachen und Auswirkungen von Vibrationen
Faktoren wie Materialungleichmäßigkeit, Fertigungstoleranzen und ungleichmäßiger Verschleiß tragen zur Unwucht des Rotors bei.
Ein unausgeglichener Rotor erzeugt unerwünschte Vibrationen, was zu erhöhten Lagerbelastungen, reduzierten Robbenlebenund mögliche strukturelle Schäden.
Die Schwingungsfrequenz entspricht typischerweise der Betriebsgeschwindigkeit der Pumpe, wobei die Amplitude proportional zum Grad der Unwucht ist.
Wie repariert man
Um die Auswirkungen einer Rotorunwucht zu mildern, werden verschiedene Auswuchttechniken eingesetzt. Das Auswuchten in einer Ebene eignet sich für kurze, starre Rotoren, während das Auswuchten in zwei Ebenen für längere, flexible Rotoren erforderlich ist.
2. Gebogene Welle
Wie eine gebogene Welle Vibrationen verursacht
Eine gekrümmte Welle führt zu einer geometrischen Asymmetrie, die dazu führt, dass der Rotor während der Drehung taumelt. Dieses Taumeln erzeugt eine Vibration mit der Rotationsfrequenz der Welle, die oft von Oberwellen begleitet wird.
Die Stärke der Vibration hängt vom Grad der Wellenauslenkung und der Betriebsdrehzahl des Rotors ab.
Methoden zur Erkennung und Quantifizierung von Wellenunrundheit
Wellenschlag, ein Maß für die Abweichung der Welle von einer geraden Linie, kann mithilfe von Messuhren oder Laserausrichtungswerkzeugen ermittelt werden. Diese Instrumente messen die radiale Verschiebung der Welle an verschiedenen Stellen und ermöglichen so die Quantifizierung des Ausmaßes der Biegung.
Überlegungen zum Richten und Ersetzen von Wellen
Wenn eine verbogene Welle festgestellt wird, müssen Korrekturmaßnahmen ergriffen werden. Bei kleineren Biegungen können Wellenrichttechniken wie Kalt- oder Wärmerichten eingesetzt werden.
Wenn die Biegung jedoch stark ist oder die Welle bereits mehreren Richtversuchen unterzogen wurde, ist häufig ein Austausch erforderlich, um einen zuverlässigen Pumpenbetrieb sicherzustellen und weitere Schäden an zugehörigen Komponenten zu verhindern.
3. Unwucht des Laufrads
Ursachen für Laufradunwucht
Eine Unwucht des Laufrads kann verschiedene Ursachen haben, unter anderem Erosion, Korrosion und Verschmutzung.
Erosion tritt auf, wenn abrasive Partikel in der gepumpten Flüssigkeit das Laufradmaterial ungleichmäßig abnutzen.
Korrosion, die durch chemische Reaktionen zwischen dem Laufrad und der gepumpten Flüssigkeit verursacht wird, kann zu ungleichmäßigem Materialverlust führen.
Fouling, also die Ansammlung von Schmutz auf den Laufradoberflächen, trägt ebenfalls zur Unwucht bei.
Auswirkungen auf Vibration und Pumpenleistung
Ein unausgeglichenes Laufrad erzeugt Vibrationen bei der Pumpenbetriebsdrehzahl und deren Vielfachen. Diese Vibrationen können zu übermäßigem Lagerverschleiß führen, Dichtungsfehler, und Kupplungsschäden.
Darüber hinaus kann eine Unwucht des Laufrads zu einer verringerten Pumpeneffizienz, einem erhöhten Stromverbrauch und einer verringerten Durchflussrate führen, da die hydraulische Leistung des Laufrads beeinträchtigt wird.
Techniken zum Auswuchten und Trimmen von Laufrädern
Um eine Unwucht des Laufrads zu beheben, kann ein Auswuchten oder Trimmen des Laufrads vor Ort durchgeführt werden.
Beim In-situ-Auswuchten wird dem Laufrad während des Einbaus in die Pumpe mithilfe spezieller Werkzeuge und Techniken Material hinzugefügt oder entfernt.
Beim Trimmen eines Laufrads hingegen muss das Laufrad entfernt und seine Oberflächen bearbeitet werden, um das Gleichgewicht wiederherzustellen.
4. Lagerprobleme
Arten von Lagerausfällen und ihre Schwingungssignaturen
Zu den häufigsten Ausfallarten zählen Innenringdefekte, Außenringdefekte, Kugel- oder Rollendefekte und Käfigdefekte.
Diese Defekte erzeugen Vibrationen bei bestimmten Fehlerfrequenzen, die mit der Geometrie und Drehzahl des Lagers in Zusammenhang stehen.
Durch die Analyse des Schwingungsspektrums können Art und Schwere des Lagerfehlers ermittelt werden.
Ursachen für Lagerausfälle
Lagerausfälle können verschiedene Ursachen haben, beispielsweise unzureichende Schmierung, Überlastung und Fehlausrichtung.
Eine unzureichende Schmierung führt zu erhöhter Reibung und Wärmeentwicklung und beschleunigt den Verschleiß.
Eine Überlastung durch zu große radiale oder axiale Kräfte kann zu vorzeitigem Ermüdungsbruch führen.
Eine Fehlausrichtung, ob winklig oder parallel, führt zu zusätzlicher Belastung der Lager und verkürzt deren Lebensdauer.
Strategien zur Lagerwartung und Zustandsüberwachung
Regelmäßiges Schmieren mit geeigneten Schmiermitteln und in geeigneten Mengen trägt dazu bei, die Reibung zu verringern und die Wärme abzuleiten.
Zustandsüberwachungstechniken wie Schwingungsanalyse, Temperaturüberwachung und Ölanalyse, geben Aufschluss über den Zustand des Lagers.
5. Wellenfehlstellung
Arten von Fehlausrichtungen
Wellenfehlstellungen können in drei Typen eingeteilt werden: eckig, parallel und kombiniert.
Eine Winkelfehlstellung tritt auf, wenn die Wellen in einem Winkel zueinander stehen, während eine Parallelfehlstellung entsteht, wenn die Wellen versetzt sind, aber parallel bleiben. Eine kombinierte Fehlstellung ist eine Kombination aus Winkel- und Parallelfehlstellung und ist die häufigste Art, die in diesem Bereich auftritt.
Auswirkungen auf Vibration und Kupplungsverschleiß
Falsch ausgerichtete Wellen erzeugen Vibrationen an der Kupplung, deren Frequenz typischerweise ein Vielfaches der Wellendrehzahl beträgt.
Diese Vibrationen können zu beschleunigtem Verschleiß der Kupplungskomponenten und damit zu einem vorzeitigen Ausfall führen.
Darüber hinaus kann eine Fehlausrichtung zu übermäßigen radialen und axialen Belastungen der Lager führen, was ihre Lebensdauer verkürzt und das Risiko eines katastrophalen Ausfalls erhöht.
Ausrichtungstechniken und Toleranzen
Zur Korrektur einer Wellenfehlstellung werden verschiedene Ausrichtungstechniken eingesetzt, darunter die Laserausrichtung, die umgekehrte Messuhrmethode und die Fühlerlehrenmethode.
Die genaueste und effizienteste Technik ist die Laserausrichtung. Dabei werden Laserstrahlen zum Messen und Anpassen der relativen Positionen der Wellen verwendet.
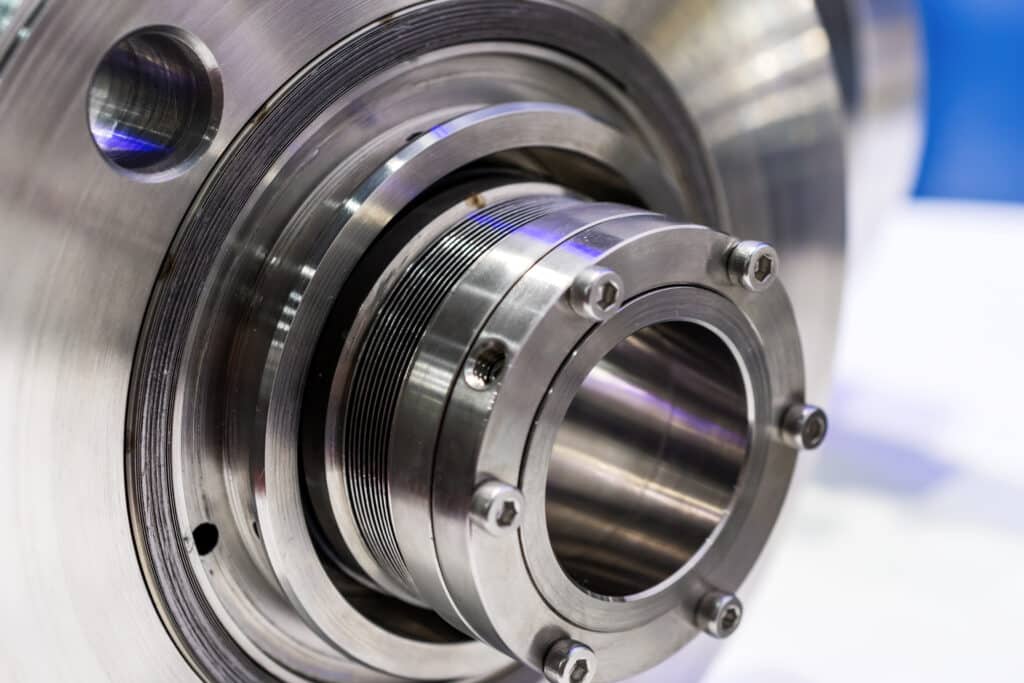
Hydraulische Ursachen für Pumpenvibrationen
1. Kavitation
Erklärung der Kavitation und ihrer Ursachen
Kavitation ist ein Phänomen, das auftritt, wenn der lokale Druck in einer Flüssigkeit unter ihren Dampfdruck fällt, wodurch sich Dampfblasen bilden. Bei Kreiselpumpen tritt Kavitation typischerweise am Laufradeinlass auf, wo die Flüssigkeit einen schnellen Druckabfall erfährt.
Faktoren wie unzureichende Netto-Saughöhe (NPSH), hohe Flüssigkeitstemperatur und eingeschränkte Saugleitungen tragen zum Auftreten von Kavitation bei.
Auswirkungen auf Vibration, Lärm und Pumpenschäden
Kavitation kann schwerwiegende Auswirkungen auf die Leistung und Lebensdauer der Pumpe haben. Wenn die Dampfblasen kollabieren, erzeugen sie hochintensive Stoßwellen, die zu erhöhten Vibrationen und Geräuschpegeln führen. Dieser als Kavitationserosion bezeichnete Prozess kann das Laufrad, die Spirale und andere Pumpenkomponenten erheblich beschädigen.
Kavitation verringert außerdem die Pumpeneffizienz und kann, wenn sie nicht behoben wird, zu einem vollständigen Pumpenausfall führen.
NPSH-Anforderungen und Strategien zur Kavitationsvermeidung
Um Kavitation zu vermeiden, muss unbedingt sichergestellt werden, dass der verfügbare NPSH-Wert (NPSHA) immer den vom Pumpenhersteller angegebenen erforderlichen NPSH-Wert (NPSHR) übersteigt.
Dies kann durch eine entsprechende Systemkonstruktion erreicht werden, einschließlich einer ausreichenden Saugrohrgröße, der Minimierung von Saugleitungsverlusten und der Aufrechterhaltung eines ausreichenden Saugdrucks.
Das Betreiben der Pumpe in der Nähe ihres Bestleistungspunkts (BEP) und die Auswahl einer Pumpe mit einer geeigneten spezifischen Saugdrehzahl (Nss) tragen ebenfalls dazu bei, das Kavitationsrisiko zu verringern.
2. Strömungspulsation
Ursachen für Strömungspulsation
Durchflusspulsationen bei Kreiselpumpen können durch verschiedene Faktoren entstehen, wie z. B. den Betrieb in der Nähe der Nulldruckhöhe oder Systemresonanz.
Wenn eine Pumpe in der Nähe ihrer Schließdruckhöhe arbeitet, wird der Durchfluss instabil, was zu Druckschwankungen und Pulsationen führt.
Eine Systemresonanz tritt auf, wenn die Pulsationsfrequenz mit der Eigenfrequenz des Rohrleitungssystems übereinstimmt, wodurch die Vibrationen verstärkt werden und möglicherweise schwere Schäden entstehen.
Auswirkungen auf Vibration und Systemstabilität
Durchflusspulsationen können den Vibrationsgrad und die Gesamtstabilität des Pumpensystems erheblich beeinträchtigen.
Durch die oszillierende Strömung werden an der Pumpe und den Rohrleitungskomponenten wechselnde Kräfte erzeugt, was zu verstärkter Vibration und Beanspruchung führt.
In extremen Fällen kann die Durchflusspulsation zu Rohrbrüchen, Geräteschäden und ungeplanten Ausfallzeiten führen.
Darüber hinaus kann es insbesondere bei sensiblen Anwendungen zu Beeinträchtigungen der Prozesskontrolle und Produktqualität führen.
Überlegungen zur Pulsationsdämpfung und zum Systemdesign
Um die Auswirkungen der Durchflusspulsation zu mildern, können verschiedene Pulsationsdämpfungstechniken eingesetzt werden.
Hierzu gehören die Installation Pulsationsdämpfer, wie Blasen- oder Membranspeicher, in der Druckleitung, um Druckschwankungen zu absorbieren. Eine ordnungsgemäße Rohrleitungskonstruktion mit Berücksichtigung von Rohrstützen, Ankern und Flexibilität kann dazu beitragen, das Risiko einer Systemresonanz zu verringern.
Darüber hinaus können Durchflussinstabilitäten minimiert werden, indem die Pumpe in größerer Entfernung von der Abschaltdruckstufe betrieben wird und ein ausreichender NPSH-Wert sichergestellt wird.
3. Off-BEP-Betrieb
Bester Wirkungsgradpunkt (BEP) und Pumpenleistungskurven
Der Best Efficiency Point (BEP) ist die Durchflussrate, bei der ein Kreiselpumpe arbeitet mit maximaler Effizienz. Pumpenleistungskurven, die Förderhöhe, Leistung und Wirkungsgrad im Verhältnis zur Durchflussrate darstellen, liefern wertvolle Informationen über die Betriebseigenschaften der Pumpe.
Der Betrieb einer Pumpe bei oder nahe ihrem besten Leistungspunkt gewährleistet optimale Leistung, minimiert den Energieverbrauch und verringert das Risiko mechanischer Probleme.
Folgen eines Betriebs abseits des BEP
Der Betrieb einer Pumpe deutlich außerhalb ihres Bestpunkts kann sich nachteilig auf den Vibrationsgrad und die Lebensdauer der Pumpe auswirken.
Bei Durchflussraten unterhalb des BEP ist die Pumpe einer erhöhten Radialbelastung ausgesetzt, was zu stärkerer Wellendurchbiegung und Lagerverschleiß führt.
Bei Durchflussraten über dem BEP kann es zu Kavitation, übermäßiger Geräuschentwicklung und Vibrationen der Pumpe kommen.
Längerer Betrieb außerhalb des BEP kann zu vorzeitigem Lagerausfall, Dichtungsschäden und Laufradverschleiß führen.
Bedeutung der richtigen Pumpenauswahl und Systemauslegung
Die Pumpe sollte so ausgewählt werden, dass sie unter normalen Betriebsbedingungen nahe ihrem besten Wirkungsgrad arbeitet. Dabei sind Faktoren wie Durchflussrate, Förderhöhe und Flüssigkeitseigenschaften zu berücksichtigen.
Das System sollte so ausgelegt sein, dass Druckverluste minimiert und stabile Strömungsbedingungen gewährleistet werden.
Eine regelmäßige Überwachung der Pumpenleistung und des Vibrationsniveaus kann dabei helfen, einen Betrieb außerhalb des Bestpunktbereichs zu erkennen und umgehend Korrekturmaßnahmen einzuleiten.
Abschließend
Pumpenvibrationen können verschiedene Ursachen haben, darunter Kavitation, Fehlausrichtung, Unwucht und mechanische Probleme. Die Identifizierung und Behebung der Grundursache ist entscheidend für die Aufrechterhaltung der Pumpenleistung und -lebensdauer.
Wenn Sie fachkundige Unterstützung bei der Diagnose und Lösung von Pumpenvibrationsproblemen benötigen, wenden Sie sich noch heute an unser erfahrenes Team.