Labyrinth seals, despite their widespread use in rotating equipment, often struggle to fully prevent leakage under high-pressure conditions. Failure to address this limitation can lead to decreased system efficiency, increased maintenance costs, and potential safety hazards. This document aims to provide a comprehensive overview of labyrinth seals, their working principles, components, classifications, and a comparison with mechanical seals.
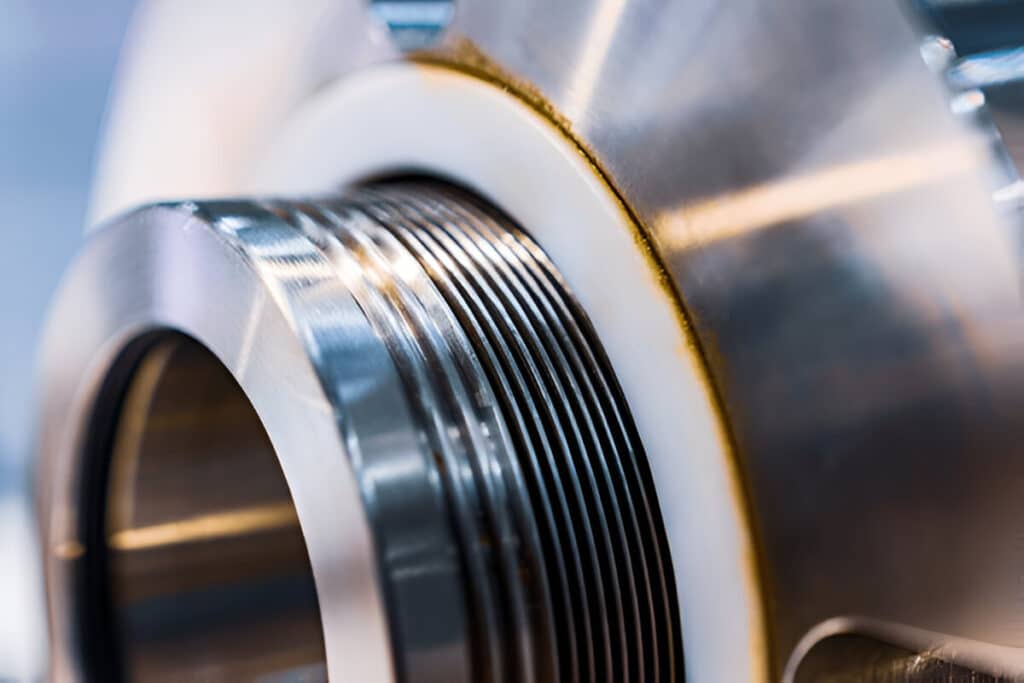
What is a Labyrinth Seal
A labyrinth seal is a specialized type of seal that utilizes a maze-like pathway to significantly reduce fluid leakage or ingress of contaminants between two regions. Also known as non-contact seals or micro labyrinth seals, these devices operate on the fundamental principle of creating an intricate, convoluted path that makes it extremely difficult for fluids or particles to pass through.
The complex passageway in a labyrinth seal consists of a series of interlocking gaps and chambers. By forcing any fluid or contaminant to navigate this winding route, labyrinth seals effectively impede their flow without requiring direct contact between the rotating and stationary components.
How Labyrinth Seals Work
The primary function of a labyrinth seal is to create an elaborate, tortuous path that hinders the passage of fluids or contaminants. This is typically accomplished by integrating multiple grooves or chambers into the sealing structure itself.
These grooves, frequently referred to as “teeth,” are strategically positioned on either the rotating components (rotors), stationary components (stators), or interlocked between the two. By alternating the placement of these teeth, a labyrinth seal forms a series of restrictions and expansions that repeatedly disrupt and divert the flow.
Centrifugal Force
One key aspect is the utilization of centrifugal force, particularly in applications involving rotating shafts. As the shaft rotates at high speeds, the centrifugal effect pushes the fluid outwards, directing it away from potential leakage paths within the seal. This outward motion helps to prevent the fluid from penetrating deeper into the labyrinth.
Vortex Motion
Furthermore, the chambers within a well-designed labyrinth seal are engineered to capture any fluid that manages to bypass the initial barriers. Once trapped, the fluid is forced into a vortex motion within these chambers. This swirling action not only prevents the fluid from escaping further but also acts as a barrier against other fluids or contaminants trying to enter the sealed area.
Turbulence
The labyrinthine nature of the pathway also contributes to the sealing effect by inducing turbulence within the fluid. As the fluid navigates the twists, turns, and sudden expansions of the labyrinth, it experiences increased turbulence and energy dissipation. This turbulence further impedes the fluid’s ability to traverse the seal, thereby enhancing the overall sealing performance.
Non-contact Operation
A distinctive attribute of labyrinth seals is their non-contact operation. Unlike many other sealing methods that rely on direct physical contact between components, labyrinth seals maintain a small but precise gap between the rotor and stator. This gap, typically on the order of a few thousandths of an inch (e.g., 0.003 inches or 76 microns).
Key Components of a Labyrinth Seal
A labyrinth seal consists of several essential components that work together to achieve effective sealing performance:
- Stator: The stator is the stationary part of the labyrinth seal. It is securely attached to the fixed portion of the machinery, such as the housing, and remains in a fixed position during equipment operation. The stator features grooves or teeth that interlock with those on the rotor to create the labyrinth pathway.
- Rotor: The rotor is the dynamic component of the labyrinth seal, directly attached to the rotating shaft of the machine. As the name implies, the rotor rotates along with the shaft, with its grooves or teeth aligning with those on the stator to form the intricate sealing path.
- Labyrinth Gap: The labyrinth gap refers to the meticulously controlled space that exists between the rotor and stator. The passages within the labyrinth gap are not simple straight paths. Instead, they extend radially inward in various complex patterns, creating a truly maze-like structure.
Classification of Labyrinth Seals
Straight-through Labyrinth Seal
The straight-through labyrinth seal represents the most basic design. It features a series of axial grooves or teeth machined into both the stationary and rotating components. While the resulting pathway remains relatively direct, the grooves create a convoluted route that effectively hinders fluid flow.
This design offers a balance between simplicity and moderate sealing efficiency, making it well-suited for applications such as pumps, turbines, and compressors where some leakage can be tolerated. The straight-through configuration is easier to manufacture compared to more complex designs, contributing to its cost-effectiveness.
Stepped Labyrinth Seal
The grooves along the sealing path feature varying axial depths, creating a stepped profile. This stepped geometry enhances the pressure differential across the seal, resulting in improved sealing efficiency.
The increased complexity of the stepped design makes it ideal for high-performance applications where minimizing leakage is crucial. Gas turbines, steam turbines, and high-pressure compressors often employ stepped labyrinth seals to maintain optimal efficiency and prevent fluid losses.
Interleaved Labyrinth Seal
In this configuration, the teeth or grooves on the rotor and stator are strategically offset or interleaved with each other. This arrangement creates an even more tortuous path for fluids, significantly increasing flow resistance.
By maximizing the complexity of the leakage path, interleaved labyrinth seals provide enhanced sealing performance. They are particularly effective in applications where high rotational speeds and significant pressure differentials are involved, such as in turbomachinery.
Labyrinth Seal vs Mechanical Seal
Operating Principle
Labyrinth seals rely on a non-contact principle, utilizing convoluted paths and fluid dynamics manipulation to obstruct flow. They do not involve any physical contact between the rotating and stationary components. In contrast, mechanical seals operate on a contact principle, relying on the physical contact between two precisely mated sealing faces to prevent leakage. These faces are held together under pressure to maintain a tight seal.
Contact
The absence of physical contact is a defining feature of labyrinth seals. A small but carefully designed gap exists between the rotating and stationary components, which is critical for the seal’s operation. On the other hand, mechanical seals rely on direct and continuous contact between the sealing faces. This contact is maintained by spring mechanisms or other means to ensure a consistent seal.
Sealing Effectiveness
Labyrinth seals, while effective in many applications, are not designed to completely prevent leakage. They are often used in systems where a certain amount of controlled leakage is acceptable or even factored into the design. In contrast, mechanical seals offer superior sealing effectiveness, even under high pressure and temperature conditions. They provide a greater degree of control over leakage rates, making them suitable for applications where minimal leakage is essential.
Design Complexity
Labyrinth seals have a relatively simple design, primarily consisting of a series of grooves or chambers machined into the sealing components. This simplicity contributes to their cost-effectiveness and ease of manufacturing. Mechanical seals, on the other hand, are more complex, incorporating multiple components such as rotating and stationary sealing faces, spring mechanisms, and auxiliary seals like O-rings or gaskets. This increased complexity allows for precise control over sealing performance but also results in higher initial costs.
Cost
The simpler design and fewer components of labyrinth seals translate to lower initial costs compared to mechanical seals. However, it’s important to consider the long-term cost implications. While labyrinth seals may have lower upfront expenses, their inability to completely prevent leakage can lead to increased operational costs over time. Mechanical seals, despite their higher initial investment, can provide long-term cost savings by minimizing fluid losses and maintaining system efficiency.
Temperature and Pressure Handling
Labyrinth seals can operate effectively under high temperature and pressure conditions. However, at extremely high pressures, their sealing efficiency may decrease due to increased leakage through the gaps. Mechanical seals offer greater versatility in handling a wide range of temperatures and pressures. They are often the preferred choice for extreme operating conditions where maintaining a tight seal is critical.
Typical Applications
Labyrinth seals find widespread use in applications such as turbines, compressors, and pumps where some leakage can be tolerated. Their non-contact nature makes them well-suited for high-speed rotating equipment, low-pressure environments, non-critical sealing applications, and dirty or abrasive conditions. Mechanical seals, on the other hand, are the go-to choice for applications where minimizing or eliminating leakage is paramount. They are commonly used in pumps, agitators, mixers, and systems handling hazardous, toxic, or expensive fluids. Mechanical seals also excel in high-pressure applications and situations requiring precise leakage control.