In the realm of industrial sealing solutions, two elastomeric materials frequently employed are Nitrile Butadiene Rubber (NBR) and Ethylene Propylene Diene Monomer (EPDM). While both NBR and EPDM exhibit excellent sealing properties, they possess distinct characteristics that make them suitable for different applications.
This blog post aims to elucidate the fundamental differences between NBR and EPDM, enabling professionals to make informed decisions when selecting the optimal material for their specific sealing requirements.
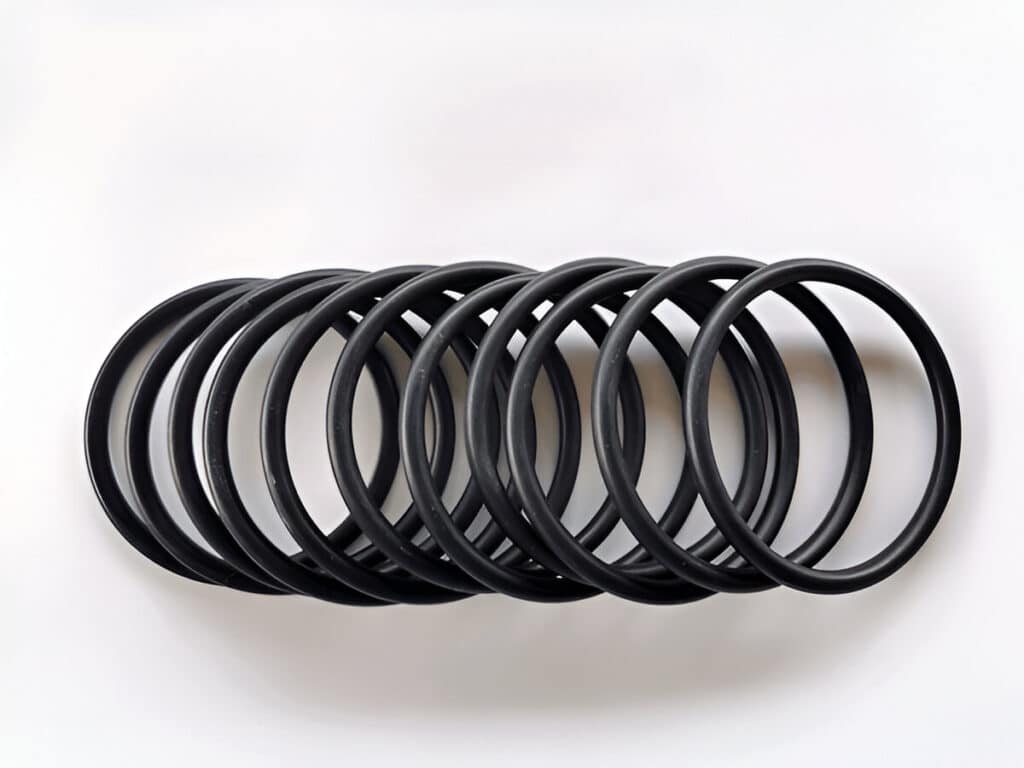
What Is NBR
Nitrile Butadiene Rubber (NBR), also known as Buna-N or Nitrile rubber, is a synthetic rubber known for its excellent resistance to oils, fuels, and other chemicals. NBR is a copolymer of acrylonitrile (ACN) and butadiene. The properties of NBR can be adjusted by varying the acrylonitrile content in the composition.
NBR has a good resistance to aliphatic hydrocarbons, but a poor resistance to ozone, weathering, and aging. It has good mechanical properties, including high tensile strength, abrasion resistance, and good compression set. NBR has a modest temperature range, typically -35°C to 100°C.
NBR is commonly used in the automotive industry for fuel and oil handling hoses, seals, and grommets. It is also used in the production of oil-resistant industrial rubber products such as conveyor belts, floor mats, and industrial gloves.
Advantages of NBR
- Superior resistance to oils, fuels, and other hydrocarbons compared to EPDM
- Excellent abrasion resistance, making it ideal for applications with friction and wear
- Higher tensile strength and tear resistance than EPDM rubber
- Better suited for applications involving petroleum-based fluids and chemicals
- Generally more affordable than EPDM for most industrial applications
Disadvantages of NBR
- Limited temperature range compared to EPDM, typically -35°C to 100°C
- Poor weather resistance, particularly to ozone, UV radiation, and outdoor environments
- Lower flexibility and elasticity than EPDM rubber
- Not suitable for applications involving steam or hot water due to poor steam resistance
- Limited color options compared to the range available with EPDM compounds
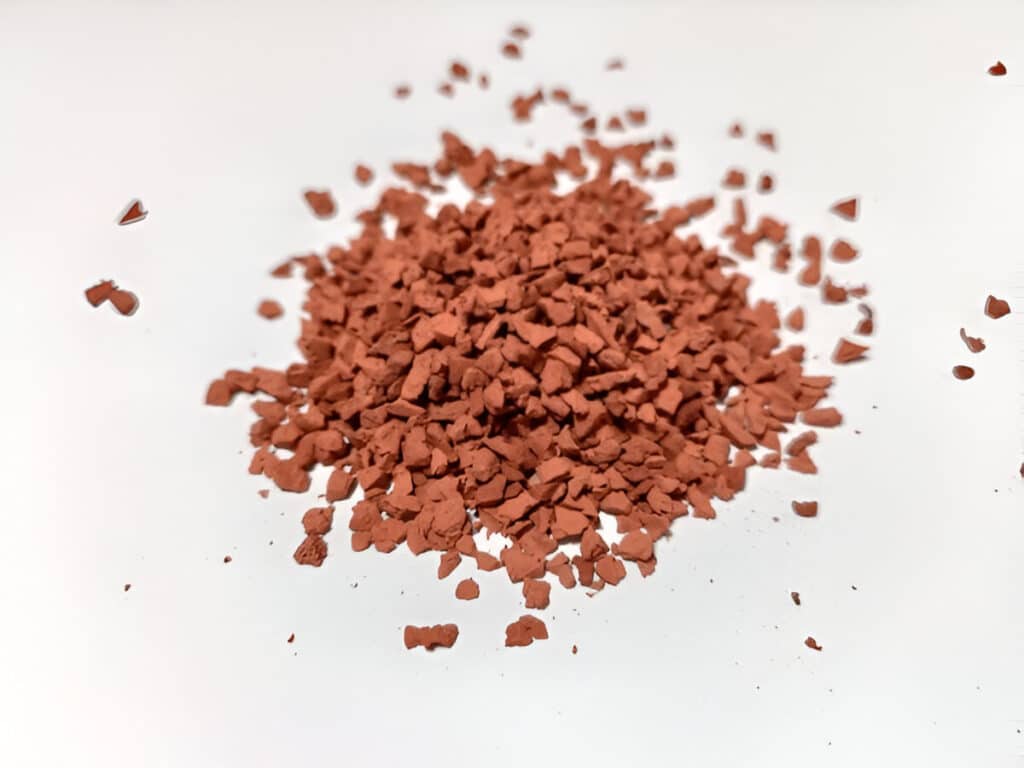
What Is EPDM
Ethylene Propylene Diene Monomer (EPDM) is a synthetic rubber known for its outstanding resistance to heat, ozone, weathering, and aging. EPDM has a saturated polymer backbone structure which gives it excellent stability.
EPDM has excellent resistance to polar substances such as water, acids, phosphates, and many alkaline solutions. However, it has poor resistance to oils and hydrocarbons. EPDM has good physical properties including high tensile strength and elongation at break. It has a wide temperature range from -50°C to 150°C.
EPDM is commonly used in outdoor applications due to its excellent weather resistance. It is used in the automotive industry for weather-stripping, radiator, and steam hoses. EPDM is also used in roofing membranes, electrical insulation, mechanical goods, and in a variety of general-purpose applications.
Advantages of EPDM
- Exceptional weather resistance, including excellent ozone and UV radiation resistance
- Wide temperature range, typically -50°C to 150°C, making it suitable for extreme conditions
- Outstanding flexibility and elasticity, even at low temperatures
- Excellent resistance to steam, hot water, and various chemicals, including acids and alkalis
- Wide range of color options and customization possibilities for specific applications
Disadvantages of EPDM
- Poor resistance to oils, fuels, and hydrocarbon-based chemicals compared to nitrile rubber
- Lower abrasion resistance than NBR, making it less suitable for high-friction applications
- Slightly lower tensile strength and tear resistance compared to nitrile rubber compounds
- Higher cost than NBR for most industrial applications and settings
- May not be the ideal choice for applications primarily involving petroleum-based fluids
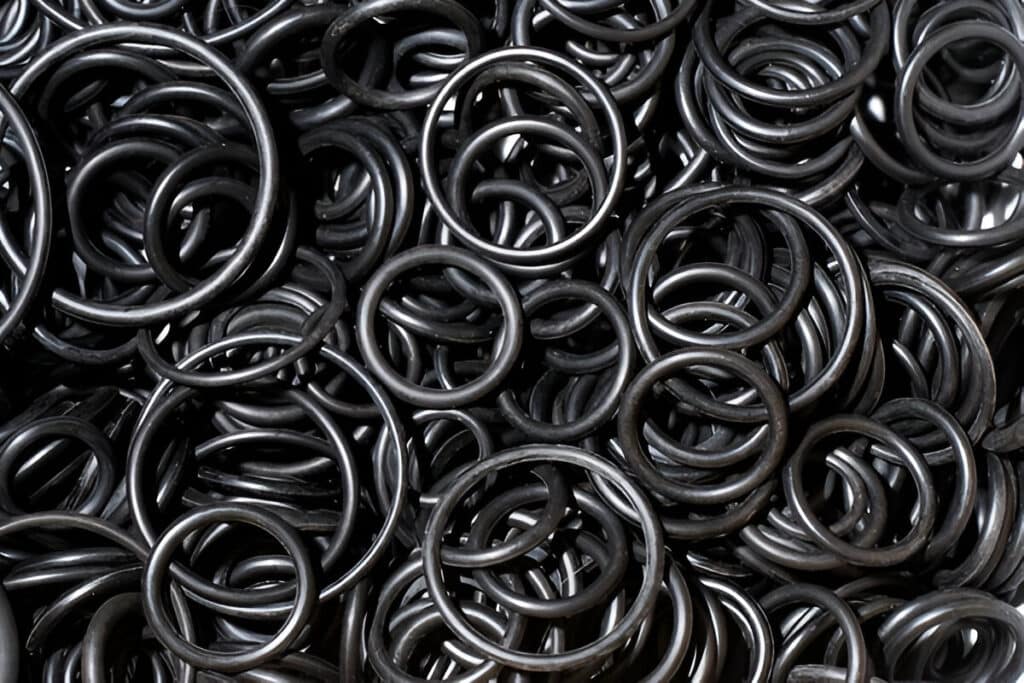
Key Difference Between NBR and EPDM
Material Composition
NBR is a copolymer of acrylonitrile and butadiene, with the acrylonitrile content typically ranging from 18% to 50%. The higher the acrylonitrile content, the better the oil and fuel resistance of the rubber.
EPDM, on the other hand, is a terpolymer composed of ethylene, propylene, and a diene monomer. The diene component allows for cross-linking, which enhances the rubber’s properties.
Temperature Range
NBR has a modest temperature range, typically from -40°C to +120°C, making it suitable for general-purpose applications.
EPDM boasts a wide temperature range, from -50°C to +150°C, allowing it to maintain its properties in both low and high-temperature environments.
Oil Resistance
NBR exhibits excellent resistance to oils, particularly petroleum-based fuels and mineral oils. This property makes it an ideal choice for applications in the automotive industry, such as fuel systems, seals, and gaskets.
EPDM, in comparison, has poor resistance to oils and hydrocarbons, which limits its use in oil-rich environments.
Weather Resistance
EPDM rubber outperforms NBR in terms of weather resistance. It offers exceptional resistance to ozone, UV radiation, and other environmental factors, making it the preferred choice for outdoor applications.
EPDM maintains its flexibility and durability even when exposed to harsh weather conditions, while NBR may degrade over time.
Chemical Resistance
Both NBR and EPDM offer chemical resistance, but their effectiveness varies depending on the type of chemicals involved. NBR provides excellent resistance to aliphatic hydrocarbons, acids, and bases, but has poor resistance to chlorinated and aromatic hydrocarbons.
EPDM, on the other hand, offers outstanding resistance to a wide range of chemicals, including acids, bases, and ketones, but has poor steam resistance.
Flexibility
EPDM rubber exhibits excellent flexibility, even at low temperatures, due to its low glass transition temperature. This property allows EPDM to maintain its elasticity and return to its original shape after deformation.
NBR, while still flexible, may become stiffer at lower temperatures compared to EPDM.
Hardness
NBR typically has a hardness range of 20 to 95 Shore A, while EPDM ranges from 30 to 90 Shore A.
Electric Insulation
EPDM rubber offers superior electric insulation properties compared to NBR. It has a high dielectric strength and low dielectric constant, making it suitable for electrical insulation applications.
NBR, while still an insulator, has lower resistivity and may not be the optimal choice for electrical components.
Common Uses
NBR is commonly used in the automotive industry for seals, gaskets, hoses, and O-rings exposed to oils and fuels. It also finds applications in the production of industrial rollers, conveyor belts, and printing rolls.
EPDM, due to its excellent weather and chemical resistance, is widely used in outdoor and industrial settings. It is the preferred choice for roofing membranes, weather stripping, electrical insulation, and seals in automotive and aerospace applications. EPDM is also used in the production of hoses, tubing, and molded parts for various industries.