Choosing the right mechanical seal for your machinery application can be a challenge. With both dry and wet seal options available, it’s important to understand their key differences.
In this post, we’ll break down the core differences between dry and wet mechanical seals, including lubrication, contact, operating condition sensitivity, maintenance needs, environmental impact, cost, and typical applications.
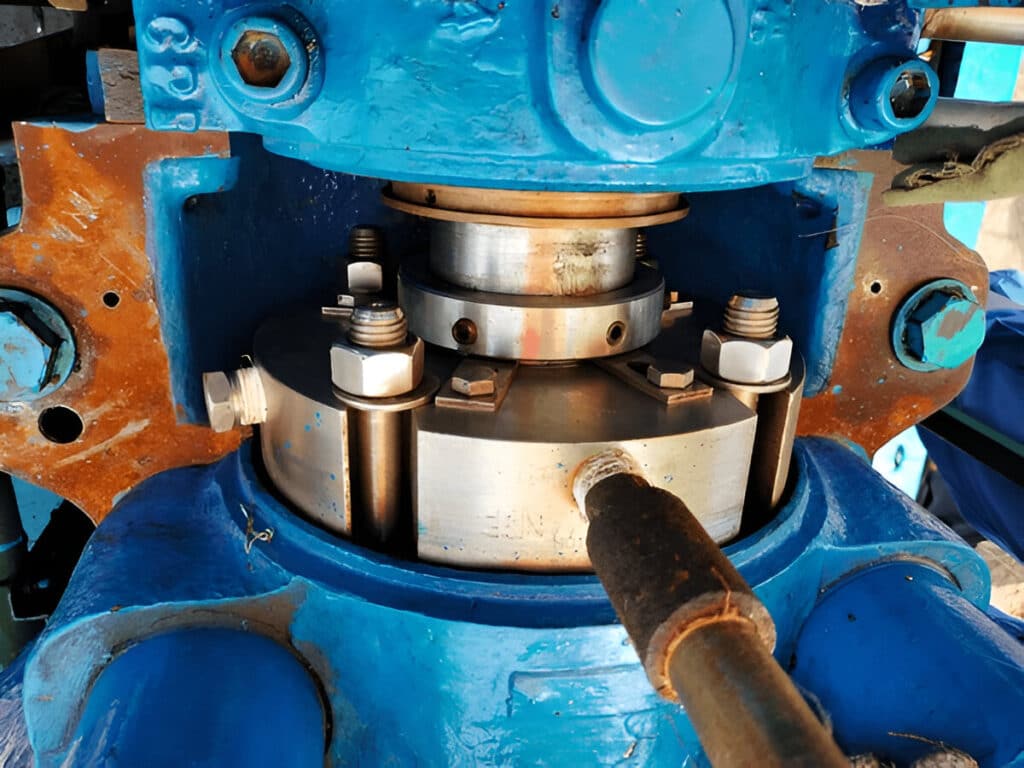
What Is Dry Mechanical Seal
A dry mechanical seal operates without any liquid barrier between the seal faces. The seal faces are made of a hard, wear-resistant material such as silicon carbide, tungsten carbide or carbon graphite. These materials have self-lubricating properties that allow the seal faces to run against each other with minimal friction and wear, even in the absence of liquid lubrication.
The stationary face is typically spring-loaded to maintain contact with the rotating face. A secondary seal, usually an O-ring, prevents leakage between the stationary face and the housing. Dry gas seals are a type of dry mechanical seal that use pressurized gas as a barrier instead of liquid. Dry mechanical seals are often used in applications where process contamination must be avoided.
What Is Wet Mechanical Seal
A wet mechanical seal uses a liquid barrier fluid between the seal faces to provide lubrication and cooling. The barrier fluid is typically recirculated from a reservoir at a pressure higher than the process fluid to prevent process fluid from entering the seal chamber.
The liquid film between the faces also helps to exclude contaminants. Wet seals are often double seals with two sets of seal faces. The barrier fluid is introduced between the two sets of faces. Any process fluid that leaks past the first set of faces is thus prevented from entering the atmosphere by the second set. Wet seals are used in applications where the process fluid is dirty, abrasive or polymerizing.
The Difference Between Dry and Wet Mechanical Seal
Lubrication
Dry seals have no liquid lubrication between the faces and depend on the seal face materials for lubrication.
Wet seals have a liquid film that lubricates the faces and provides more forgiving operating conditions.
Contact
In dry seals, the seal faces run in direct contact with each other without any liquid film separating them.
Wet seals maintain a thin liquid film between the seal faces, avoiding direct contact of the sliding faces.
Sensitivity to Operating Conditions
Dry seals are more sensitive to changes in operating conditions such as temperature, pressure and speed compared to wet seals. Factors such as thermal expansion, pressure distortion and dynamic instability can cause the faces to distort or open up, resulting in increased leakage.
Wet seals are more forgiving due to the cushioning and heat dissipation provided by the barrier fluid.
Maintenance Frequency
Dry seals may require more frequent maintenance and face replacement due to the direct contact and wear between faces.
Wet seals, when operated with a clean and compatible barrier fluid, tend to have longer intervals between maintenance.
Environmental Impact
Dry seals have less environmental impact compared to wet seals. Since there is no liquid barrier, there is no risk of barrier fluid leakage or disposal. Dry gas seals use an inert gas as the barrier which vents out to the atmosphere.
Wet seals pose the risk of barrier fluid leakage which can contaminate the process or the environment. The barrier fluid also needs to be disposed of safely.
Cost
The initial cost of a dry seal is generally lower than a wet seal due to the simpler design and fewer components. However, the operating and maintenance costs can be higher due to increased wear and more frequent part replacement.
Wet seals have a higher upfront cost but typically last longer and require less frequent repairs. The cost of barrier fluid and its disposal also need to be considered.
Applications
Dry seals are suitable for clean, non-polymerizing fluids at moderate temperatures and pressures. Typical applications include gas compressors, steam turbines and pumps handling hydrocarbons and other volatile fluids.
Wet seals are used for more demanding duties involving high pressures, temperatures, and dirty or abrasive fluids. Examples include petroleum refineries, chemical plants and power plants.