The machinery industry faces constant challenges in creating reliable, flexible, and precise components that can withstand harsh operating conditions. Traditional solutions often fall short, leading to costly downtime and repairs.
Edge-welded bellows offer a game-changing solution for the machinery industry. With their unique design and manufacturing process, edge-welded bellows provide superior flexibility, durability, and precision for a wide range of applications. From axial to angular and lateral movement, these innovative components can handle it all while ensuring reliable performance in even the most demanding environments.
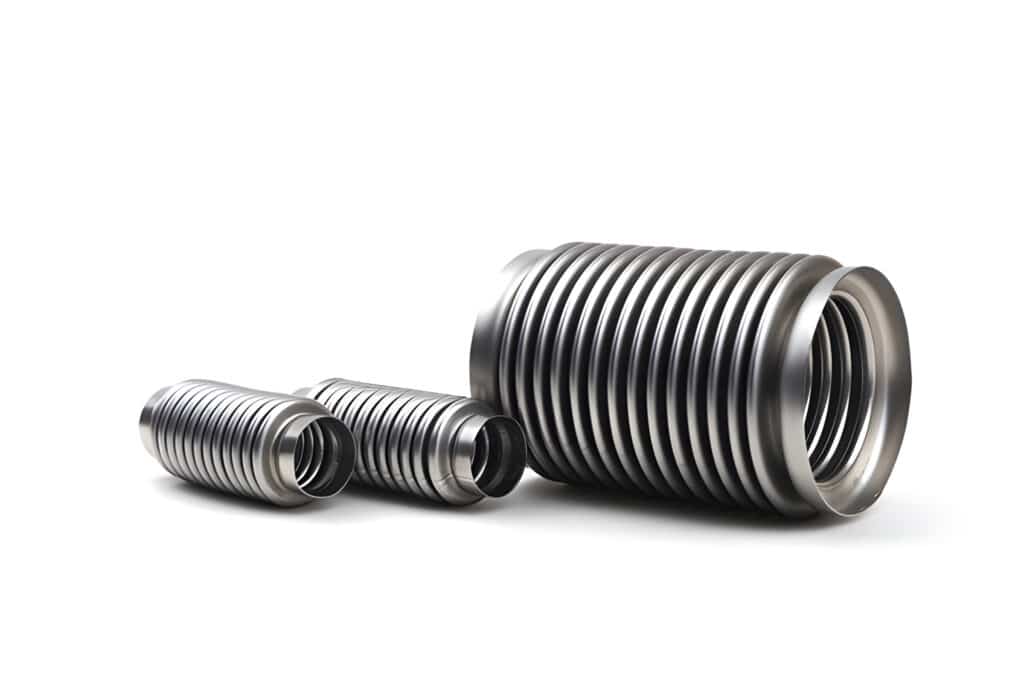
What Are Edge-Welded Bellows
Edge-welded bellows are flexible, pressure-tight components used to accommodate movement in mechanical systems while maintaining a sealed environment. These bellows are constructed by welding together a series of thin metal diaphragms, typically made from corrosion-resistant materials such as stainless steel, Inconel, or Hastelloy. The welded edges of the diaphragms form convolutions, allowing the bellows to compress, extend, and flex without leakage.
The primary function of edge-welded bellows is to serve as a dynamic seal in applications that require motion while maintaining a barrier between two different media or environments. They are designed to withstand high pressures, extreme temperatures, and corrosive conditions, making them suitable for use in a wide range of industries, including aerospace, semiconductor manufacturing, cryogenics, and vacuum systems.
Design Factors
Diaphragm Plate Thickness
Thinner plates allow for greater flexibility and movement, but may limit pressure capacity. Thicker plates can withstand higher pressures but reduce flexibility. Typical diaphragm thicknesses range from 0.002 to 0.060 inches (0.051 to 1.524 mm), with the most common being between 0.005 to 0.015 inches (0.127 to 0.381 mm).
Diaphragm Plate Shape
Common shapes include circular, rectangular, and square plates. Circular plates provide uniform stress distribution and are suitable for high-pressure applications. Rectangular and square plates offer greater stability for lateral movement but may have higher stress concentrations at the corners.
Plate shape also affects the convolution profile of the bellows. Deeper convolutions allow for greater axial movement, while shallower convolutions provide better stability for lateral movement.
Weld Shape
The most common weld shape is a butt weld, where the edges of adjacent plates are welded together directly. This provides a strong, leak-tight seal.
Other weld shapes, such as step welds or lap welds, may be used for specific applications. Step welds can help reduce stress concentrations, while lap welds allow for thicker plate materials.
Seal Face Balance
Seal face balance refers to the distribution of pressure on the sealing surfaces of edge-welded bellows. In a balanced design, the pressure acting on the inside of the bellows is evenly distributed across the sealing surface. This prevents excessive pressure on any one area, which could lead to leakage or premature wear.
Unbalanced designs, where the pressure is not evenly distributed, can result in higher contact forces on certain areas of the seal face. This can cause accelerated wear, seal face distortion, and reduced sealing effectiveness.
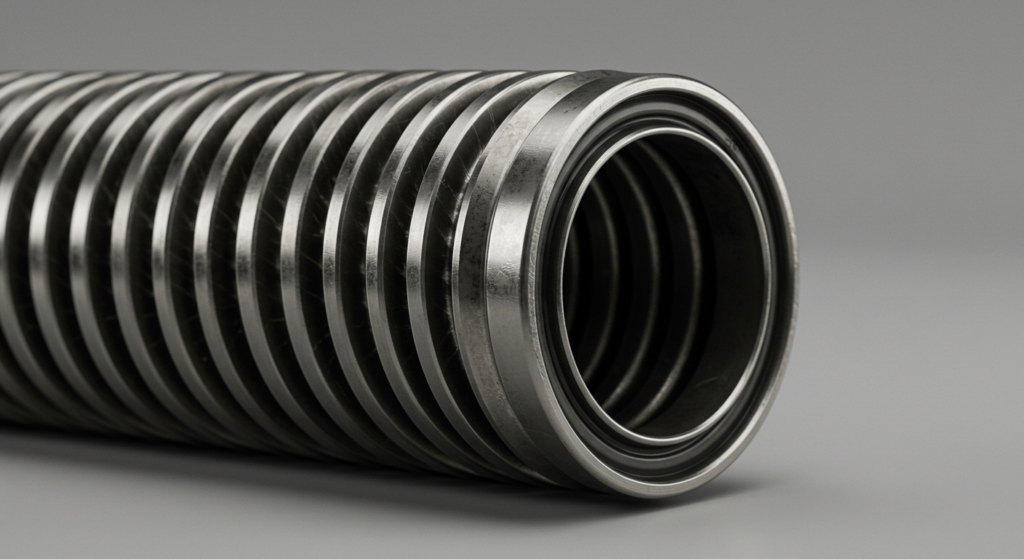
Types of Edge-Welded Bellows
Nested Ripple Bellows
Nested ripple bellows feature a series of nested convolutions with alternating inward and outward folds. This design provides excellent flexibility and allows for significant axial movement. Nested ripple bellows are commonly used in applications requiring high compression ratios, such as in vacuum systems and valves.
Crescent Bellows
Crescent bellows have a unique crescent-shaped convolution profile. This design offers a balance of axial and lateral flexibility, making them suitable for applications with moderate angular and offset movement requirements. Crescent bellows are often used in seal shaft connections and pump couplings.
Flat Plate Bellows
As the name suggests, flat plate bellows are constructed from flat diaphragm plates. This simple design provides good stability and is often used in applications with limited movement requirements. Flat plate bellows are typically less flexible than other types but offer excellent pressure and temperature capabilities.
Single Sweep Bellows
Single sweep bellows have convolutions that sweep in only one direction, creating a cup-like shape. This design allows for significant lateral movement in one plane while providing stability in the perpendicular plane. Single sweep bellows are used in applications requiring high lateral offset, such as in pump connectors and exhaust joints.
Torus Bellows
Torus bellows feature convolutions with a partial toroidal shape. This unique geometry provides excellent angular and lateral flexibility, making torus bellows ideal for applications with high misalignment or offset requirements. Common applications include gimbal joints and flexible connectors in piping systems.
Types of Movement
Axial Movement
Axial movement refers to the compression and extension of the bellows along its central axis. This type of movement allows the bellows to absorb linear displacements, compensate for thermal expansion, or provide a sealed, flexible connection between two components.
Angular Movement
Angular movement occurs when the bellows is subjected to a bending force, causing it to flex at an angle relative to its central axis. Edge-welded bellows can accommodate angular misalignment between connected components, allowing for smooth operation even when parts are not perfectly aligned.
Lateral Movement
Lateral movement, also known as offset or transverse movement, involves the displacement of one end of the bellows relative to the other in a direction perpendicular to the central axis. This type of movement allows edge-welded bellows to compensate for lateral misalignment or provide a flexible connection that can handle shear forces.
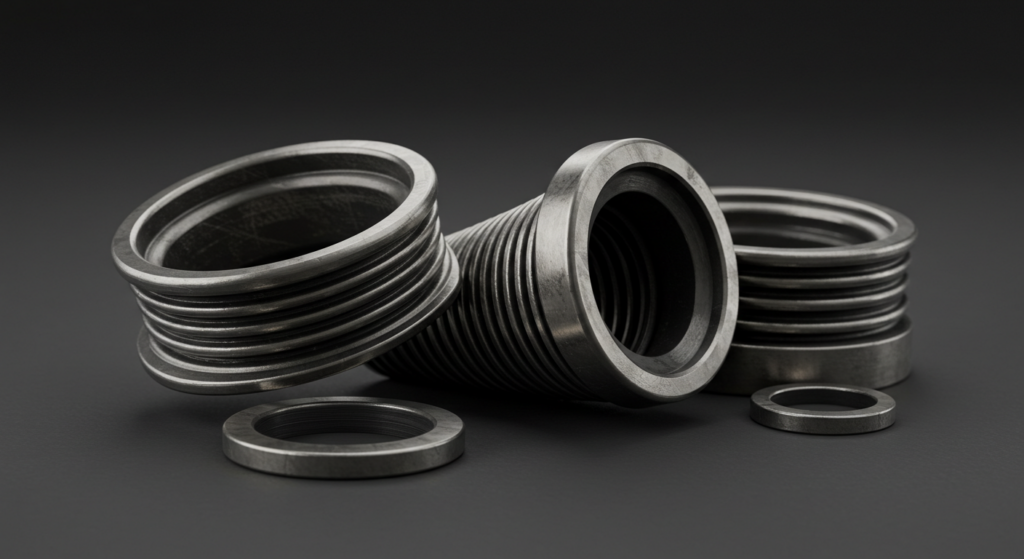
Manufacturing Process of Edge-Welded Bellows
Material Selection
The first step in manufacturing edge-welded bellows is selecting the appropriate material. The choice of material depends on factors such as the operating environment, required strength and flexibility, and compatibility with the media being contained or excluded. Common materials used for edge-welded bellows include stainless steel, titanium, inconel, and hastelloy.
Diaphragm Stamping
Once the material is selected, individual diaphragms are stamped from sheets of the chosen material using precision dies. The stamping process creates the basic shape of each diaphragm, including any required contours or features.
Cleaning and Preparation
Before the diaphragms can be assembled into a bellows, they must be thoroughly cleaned to remove any dirt, oil, or residue from the stamping process. The cleaned diaphragms are then stacked in the desired order, with the edges properly aligned in preparation for welding.
Convolution Formation
To form the convolutions that give edge-welded bellows their flexibility, the stacked diaphragms are welded together along their outer edges. This welding process is typically performed using advanced techniques such as laser welding, electron beam welding, or TIG welding. The welding parameters are carefully controlled to ensure a strong, leak-tight seal without compromising the material properties.
Bellows Core Welding
After the convolutions are formed, the inner edges of the diaphragms are welded together to create a sealed, pressure-tight core. The type of welding used for the core depends on the material and performance requirements, with laser and electron beam welding being common choices for their precision and minimal heat input.
Welding to End Fittings
To integrate the edge-welded bellows into a larger assembly, end fittings are welded to the ends of the bellows. These end fittings, which can be flanges, tubes, or custom shapes, provide a means of connecting the bellows to other components.
Leak Testing
The final step in the manufacturing process is leak testing. Each edge-welded bellows assembly is subjected to rigorous leak testing to verify its pressure integrity and leak-tightness. This testing typically involves pressurizing the bellows with a tracer gas, such as helium, and using sensitive detection equipment to check for any leaks. Only bellows assemblies that pass the leak test are considered ready for use.