Mechanical seal face materials determine how well your equipment prevents leaks and lasts over time. They must resist heat, wear, and chemical attack while maintaining a lapped, extremely flat interface. Typically, one face is made of a softer, more compliant material (often a carbon graphite composite) and the other of a harder material (ceramic or carbide).
Common mechanical seal face materials include carbon-graphite, ceramic (aluminum oxide), silicon carbide, tungsten carbide, Ni-Resist, GF PTFE and other metal materials.
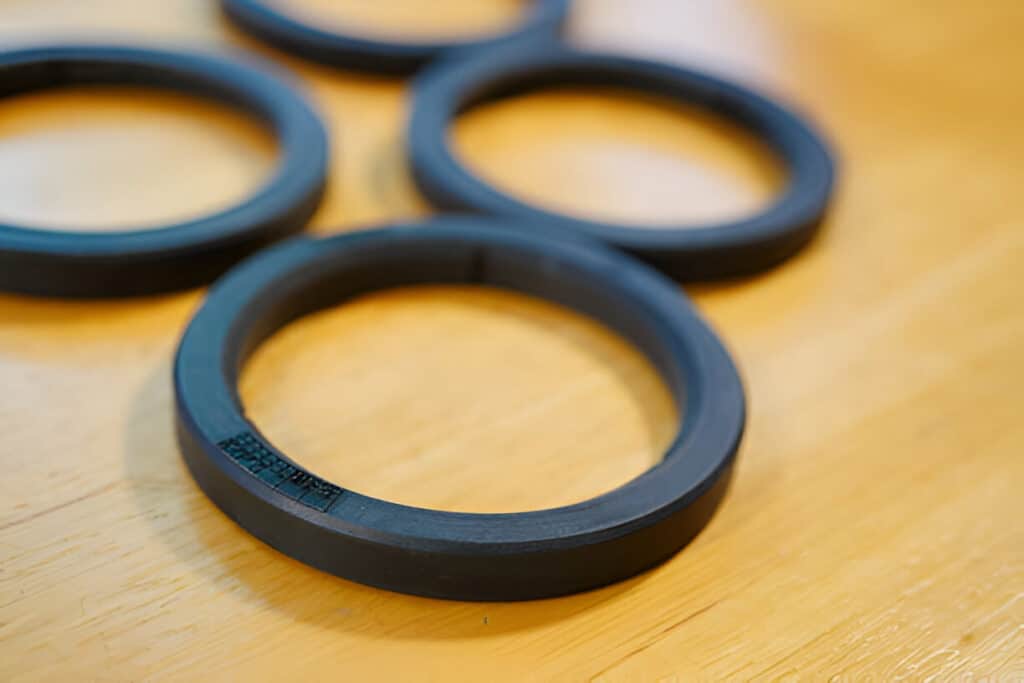
Carbon Graphite (Carbon)
Carbon graphite (often simply called “carbon”) is by far the most common seal face material for one of the two faces. It is a composite material made from a mixture of carbon/graphite powders that are molded and baked, then usually impregnated with resins or metals to enhance its properties.
Carbon-graphite is a relatively soft material (compared to ceramics) with a porous structure that the impregnant fills to make it impervious and stronger. Common impregnants are synthetic resins or metals like antimony. Carbon is unique in that it is self-lubricating – the graphite structure provides a low coefficient of friction and can form a lubricious film. It also has excellent thermal conductivity. These traits make carbon ideal as a “wiping” or wearing face running against a harder counterface.
Ceramic (Aluminum Oxide)
Ceramic in mechanical seals typically refers to Alumina (Aluminum Oxide), usually 99%+ purity alumina oxide. It is a hard, brittle ceramic material (Mohs hardness around 9) that has been used in seals for many decades.
A typical alumina seal face is white or ivory-colored. Alumina ceramic is very chemically inert in most liquids and is also quite inexpensive compared to advanced carbides. It can be formed into seal rings and lapped to a fine finish. Alumina has moderate thermal conductivity and a high temperature capability in itself (the material can withstand >1000 °C), but as a seal face its limitations come from its brittleness and thermal shock behavior.
Silicon Carbide (SiC)
Silicon carbide is a premium hard face material that has become extremely common in modern mechanical seals. It is a ceramic compound of silicon and carbon, typically dark gray or black in color. SiC is one of the hardest seal face materials (hardness ~9.5 Mohs, second only to diamond). It has excellent wear resistance, very high thermal conductivity, and is highly chemical inert.
There are two main types used in seals: reaction-bonded silicon carbide and sintered silicon carbide.
Reaction-bonded SiC (sometimes called RB Sic) is made by infusing molten silicon into a carbon matrix; it ends up with about 8–12% free silicon in the material.
Sintered SiC (also called alpha SiC) is made by directly sintering silicon carbide powder without free silicon, yielding a pure ceramic. Both are hard and wear-resistant, but they have different chemical resistances (due to the free silicon in RB SiC).
Tungsten Carbide (WC)
Tungsten carbide is a hard, heavy metal composite that is also widely used for seal faces. It is technically a cermet (ceramic-metal) – extremely hard tungsten carbide particles are cemented together with a metallic binder (either cobalt or nickel). The resulting material is very hard (Mohs ~9) and also quite tough (less brittle than pure ceramics due to the metal binder).
Tungsten carbide is dense (almost 2-3 times heavier than steel), gray in color, and has a lustrous metallic appearance when polished. Historically, cobalt-bonded tungsten carbide was common, but in mechanical seals, nickel-bonded tungsten carbide is often preferred now for better corrosion resistance. The typical binder content is around 6–10% by weight, with the rest being WC.
Other Face Materials (Metals, Coatings, and Polymers)
While carbon, ceramic, SiC, and tungsten carbide are the most prevalent seal face materials, there are a few others used in niche or older applications:
- Ni-Resist (Nickel-Resistant Cast Iron): Ni-Resist is an alloyed cast iron (~20-25% Ni) that is sometimes used for seal faces (typically the stationary seat). It is essentially a hard iron that is cheap and has decent corrosion resistance to fresh water.
- Bronze and Other Metals: Soft metals like bronze were used in the past for seal faces (often with a carbon partner). Bronze (especially leaded bronze) is soft and was attractive for its conformability and a bit of lubricity from the lead content. But bronze faces distort with heat (poor dimensional stability) and wear fast. They also can’t handle high speeds (they would rub and smear). As a result, bronze faces are now rare, typically only seen in old designs or perhaps very low duty seals.
- Stellite: Stellite is a cobalt-chrome alloy that is very hard and wear resistant. It can be applied as a welded overlay on a stainless steel part to create a hard facing. Stellite-faced seals were more common before SiC became prevalent. They are still used for very large diameter seals (like on big reactor agitators or large shaft seals) where making a huge SiC ring would be extremely costly.
- Glass-Filled PTFE: PTFE (Teflon) by itself is an excellent chemical-resistant material but is far too soft and has a tendency to creep (cold flow) under pressure. To use PTFE as a seal face, it must be reinforced – the most common is Glass-Filled PTFE, where about 15–25% glass fiber is mixed into PTFE. This gives a much harder material that can be lapped to a seal face. The big advantage of GFPTFE is chemical inertness – it can handle acids, alkalis, chlorine, and other extremely aggressive chemicals that would attack carbon or metals. It also has a very low friction coefficient.
Material | Hardness & Wear | Chemical Resistance | Max. Temperature | Key Advantages | Key Drawbacks |
---|---|---|---|---|---|
Carbon-Graphite | Soft/Compliant (wears in abrasives); self-lubricating surface. | Excellent in many fluids; resin or metal impregnation can be attacked by strong oxidizers or acids. | ~260 °C (resin grade); ~370 °C (antimony grade). | Self-lubricating (prevents scoring); broad compatibility; forgiving to upset (blister-resistant grades available). | Low mechanical strength; wears fast with abrasives; can blister with vaporizing fluids (if improper grade). |
Ceramic (Alumina) | Hard, but brittle; good wear in clean service, not for heavy solids. | Inert to most chemicals (not HF acid); no corrosion issues. | ~175 °C (recommended max for alumina in seal service). | Low cost; good wear against carbon; corrosion-proof in water and common fluids. | Very brittle (cracks under thermal shock or impact); lower thermal conductivity (can run hot); limited to moderate speeds/pressures. |
Silicon Carbide | Extremely hard (Mohs 9.5); excellent abrasion resistance (best for slurries). | Excellent: Chemically inert (sintered SiC) to practically all fluids; avoid reaction-bonded grade in pH < 4 or > 11 (free silicon can corrode). | ~400 °C (with appropriate design/holder). Faces themselves stable to 800 °F+. | Highest wear resistance; high thermal conductivity (runs cooler); handles high speeds & pressures; great for corrosive and abrasive services. | Brittle (care in handling); high cost; requires proper mounting to avoid thermal stress; reaction-bonded type not for strong acids/bases. |
Tungsten Carbide | Very hard (Mohs ~9); tough (resists chipping, good for impact/vibration); superior in some abrasive conditions. | Good: Resists mild corrosion, especially with Ni binder; not inert – binder (especially Co) attacked by strong acids, amines, etc.. | ~400 °C (solid WC ring). Pressed in holders may limit to ~260 °C unless special alloys used. | Withstands high pressure (high stiffness, no face distortion); durable under vibration or cavitation; excellent wear in slurry/dirty services. | Expensive; very heavy (high density); less chemically inert than SiC (Ni-WC is better than Co-WC); higher friction (usually run with carbon to lubricate). |
Ni-Resist (Ni-CI) | Soft metal (much softer than carbide); wears quickly – suitable only for clean fluids. | Limited corrosion resistance (okay in neutral pH water, will rust in acids). | ~175 °C (350 °F) max. | Very low cost; tolerates thermal shock (metallic); low friction against carbon (graphitic cast iron). | Poor wear resistance; not for high speeds or any abrasives; corrodes in aggressive fluids, oxidizes at temp. |
GF PTFE | Very soft (low hardness, even with glass); prone to wear and deformation under load. | Outstanding: Inert to nearly all chemicals (acids, caustics, chlorine, etc.). | ~150–200 °C (above this PTFE creeps or degrades). | Ultimate chemical resistance; low friction (non-stick); prevents metal contact in highly aggressive services. | Very low PV limits (only for low pressure & speed); cold flows (needs support); short life – used only when nothing else holds up. |