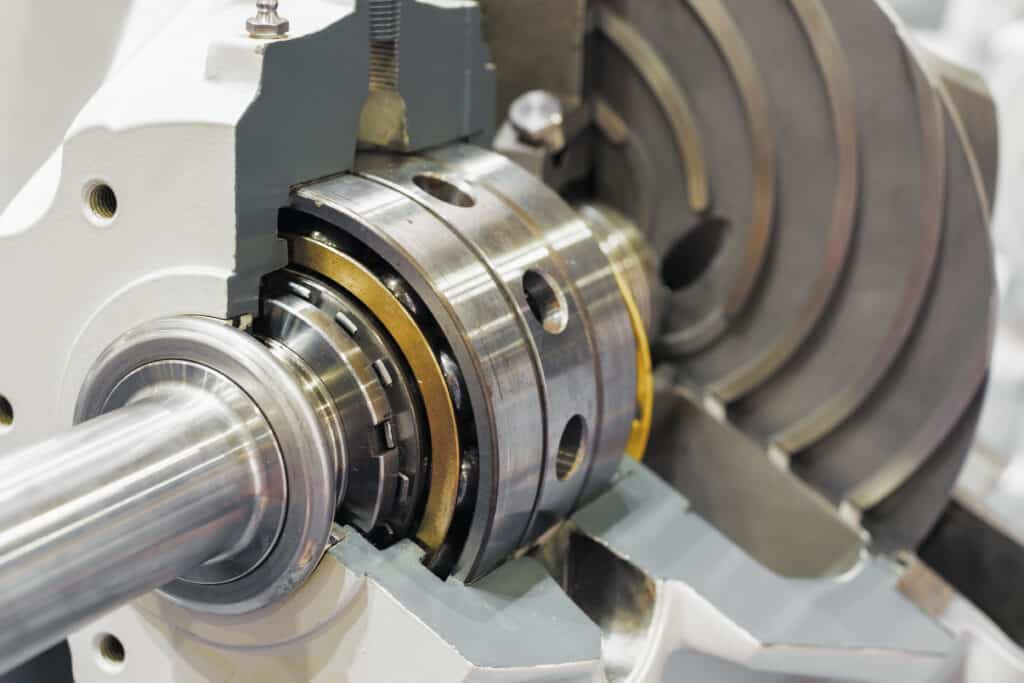
Do Mechanical Seals Need Lubrication
Mechanical seals require lubrication during operation to maintain a stable fluid film between the sealing surfaces. This fluid film, also known as a boundary film, prevents direct contact between the seal faces, which would otherwise result in excessive wear and premature failure.
When Do Mechanical Seals Need Lubrication
- High-speed applications: As the rotating shaft speed increases, the seal faces generate more heat due to friction. Adequate lubrication is necessary to dissipate this heat and prevent thermal damage to the seal materials.
- High-pressure applications: In high-pressure systems, the mechanical seal faces experience increased loading, which can lead to higher friction and wear. Proper lubrication helps to distribute the load evenly and maintain a stable fluid film.
- Dry running conditions: Some mechanical seals may encounter dry running conditions during startup or shutdown periods. In these situations, a lubricant reservoir or barrier fluid system can provide temporary lubrication until the process fluid reaches the seal faces.
- Abrasive or corrosive environments: When handling abrasive or corrosive fluids, mechanical seals require lubrication to minimize the impact of these aggressive media on the sealing surfaces. The lubricant helps to flush away abrasive particles and neutralize corrosive substances.
What Kind of Lubricant Is Used for Mechanical Seals
The selection of the appropriate lubricant for a mechanical seal depends on various factors, including the type of seal, operating conditions, and the process fluid being handled. Some common types of lubricants used for mechanical seals include:
- Process fluid: In many applications, the process fluid itself acts as the lubricant for the mechanical seal. This is known as a “wet seal” arrangement, where a portion of the process fluid is allowed to leak into the seal chamber, providing lubrication and cooling to the seal faces.
- Barrier fluids: In some cases, a separate barrier fluid is used to lubricate the mechanical seal. This is particularly useful when the process fluid is not suitable for lubrication due to its abrasive, corrosive, or volatile nature. Common barrier fluids include glycol-based solutions, silicone oils, and petroleum-based lubricants.
- Flush fluids: Flush fluids are used to cool and lubricate the mechanical seal while also preventing the accumulation of solids or contaminants in the seal chamber. These fluids are typically clean, compatible with the process fluid, and have good heat transfer properties. Examples include water, oil, or specially formulated synthetic fluids.
- Grease: In some slow-speed applications or for seals with elastomeric materials, grease can be used as a lubricant. The grease is packed into the seal chamber during assembly and provides lubrication for a limited period. However, this method is not suitable for high-speed or high-temperature applications.
How Do You Lubricate a Mechanical Seal
Lubricating a mechanical seal involves ensuring that a sufficient and continuous supply of the appropriate lubricant reaches the sealing surfaces. The specific lubrication method depends on the seal design and the application requirements. Some common methods for lubricating mechanical seals include:
- Process fluid lubrication: In this method, the process fluid itself lubricates the seal faces. The seal is designed to allow a controlled amount of process fluid to enter the seal chamber, creating a thin fluid film between the sealing surfaces. This method is suitable for applications where the process fluid is clean, non-abrasive, and compatible with the seal materials.
- Barrier fluid lubrication: In this arrangement, a separate barrier fluid is introduced into the seal chamber to lubricate the seal faces. The barrier fluid is pressurized to a level higher than the process fluid to prevent leakage and maintain a stable lubricating film. This method is used when the process fluid is not suitable for direct lubrication or when enhanced cooling and lubrication are required.
- Flush fluid lubrication: This method involves injecting a clean, compatible flush fluid into the seal chamber to lubricate and cool the seal faces. The flush fluid also helps to prevent the accumulation of solids or contaminants in the seal chamber. The fluid is typically introduced through a separate port and is continuously circulated to maintain a stable lubricating film.
- Grease lubrication: For slow-speed applications or seals with elastomeric components, grease lubrication can be used. The seal chamber is packed with a suitable grease during assembly, which provides lubrication for a limited period. Regular re-greasing may be necessary to maintain adequate lubrication.
Can Mechanical Seals Run Dry
Prolonged dry running can cause severe damage to the mechanical seal and should be avoided whenever possible. The absence of a lubricating film leads to increased friction, heat generation, and wear of the sealing surfaces.