Pump cooling seal systems offer a robust solution to these challenges. This comprehensive overview will delve into the components, purposes, and types of these systems based on cooling methods, providing insights to optimize pump performance and reliability.
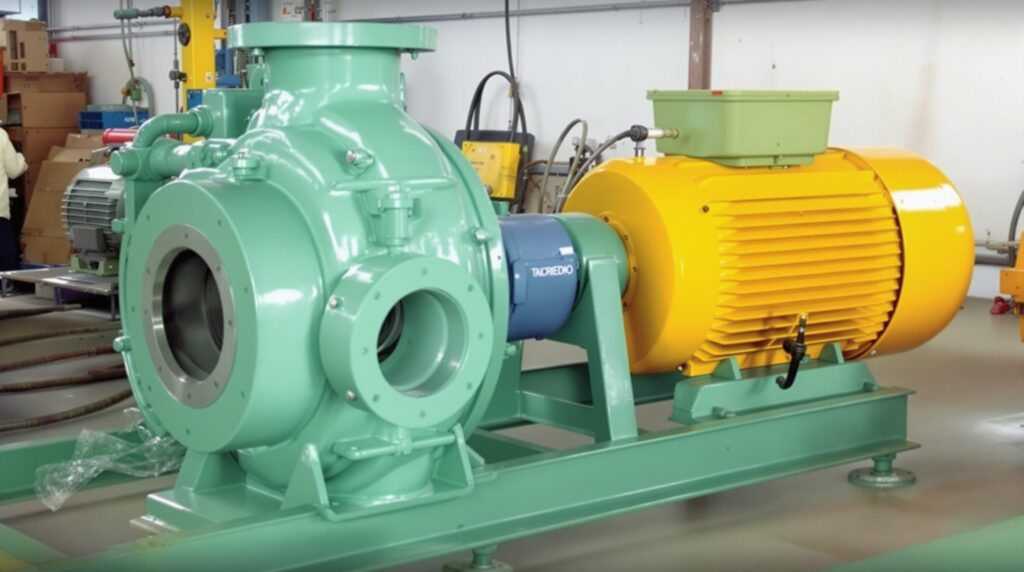
What is a Pump Cooling Seal System
A pump cooling seal system is an integral component of many pumping systems, particularly in industrial applications involving high temperatures, pressures, or hazardous materials.
At its core, a pump cooling seal system consists of a seal chamber that surrounds the mechanical seal. This chamber is typically filled with a cooling fluid, such as water or a water-glycol mixture, which circulates around the seal. The fluid serves to absorb and dissipate heat generated by friction at the seal faces, thereby preventing excessive temperature buildup that could lead to seal damage or failure.
purposes of Pump Cooling Seal System
- Cooling the seal and shaft: The friction generated between the rotating and stationary components of the mechanical seal produces heat. The cooling seal system continuously removes heat from the seal faces and shaft, maintaining optimal operating temperatures.
- Lubricating the seal: The cooling fluid circulated by the seal system acts as a lubricant, creating a thin film between the seal faces that prevents direct contact and minimizes wear..
- Flushing away impurities: In some applications, the pumped fluid may contain solids, crystals, or other contaminants that can accumulate on the seal faces and cause abrasive wear or clogging. The cooling seal system provides a continuous flow of clean fluid that flushes away these impurities, keeping the seal faces clean and free from harmful deposits.
Components of Pump Cooling Seal System
- Mechanical seal: The heart of the cooling seal system is the mechanical seal itself. It consists of two main components – a rotating seal ring attached to the shaft and a stationary seal ring mounted in the seal housing. The seal faces are precisely lapped and polished to create a tight seal when pressed together.
- Seal chamber: The seal chamber is the space surrounding the mechanical seal where the cooling fluid circulates. It is designed to contain and direct the flow of the cooling medium, ensuring proper heat dissipation and lubrication. The seal chamber also serves as a collection point for any leakage past the seal faces.
- Cooling fluid lines: The cooling seal system includes a network of pipes, hoses, or tubing that carries the cooling fluid to and from the seal chamber. These lines are sized and routed to provide adequate flow and pressure while minimizing pressure drops and turbulence.
- Heat exchanger (optional): In some cases, the heat removed from the seal may need to be dissipated to maintain the cooling fluid at a suitable temperature. A heat exchanger, such as a shell-and-tube or plate type, can be incorporated into the cooling system to transfer heat from the circulating fluid to a secondary coolant or the atmosphere.
Based on Cooling Method
External Flush
In an external flush cooling system, a clean, cool fluid is introduced into the seal chamber from an external source. The flushing fluid can be taken from the pump discharge, a separate pumping system, or a pressurized reservoir. The flush flow is regulated by control valves, orifices, or flow meters to maintain the desired flow rate and pressure.
External flush systems are commonly used when the pumped fluid is dirty, abrasive, or prone to crystallization.
Quench
A quench cooling system involves injecting a small amount of a low-pressure, inert fluid into the atmospheric side of the seal chamber. The quench fluid, such as nitrogen gas or clean water, creates a barrier that prevents the ingress of contaminants and absorbs heat from the seal faces.
Quench systems are often used in conjunction with double seals, where the quench fluid is introduced between the primary and secondary seals.
Closed-loop System
In a closed-loop cooling system, the cooling fluid is continuously circulated through the seal chamber and a heat exchanger. The heat generated by the seal is transferred to the cooling fluid, which then passes through the heat exchanger to dissipate the heat to a secondary coolant or the atmosphere. The cooled fluid returns to the seal chamber, completing the loop.
Closed-loop systems provide a stable, controlled environment for the seal and are suitable for high-temperature or critical applications.