Mechanical seals are essential components in machinery, but they can fail prematurely if not properly monitored and maintained.
Seal failures lead to leaks, equipment damage, unplanned downtime, and costly repairs – all of which significantly impact production and profitability.
By recognizing the common signs of mechanical seal failure early, such as visual leakage, unusual noises, excessive vibration, overheating, and contamination, proactive maintenance can be performed to prevent catastrophic failures and minimize operational disruptions.
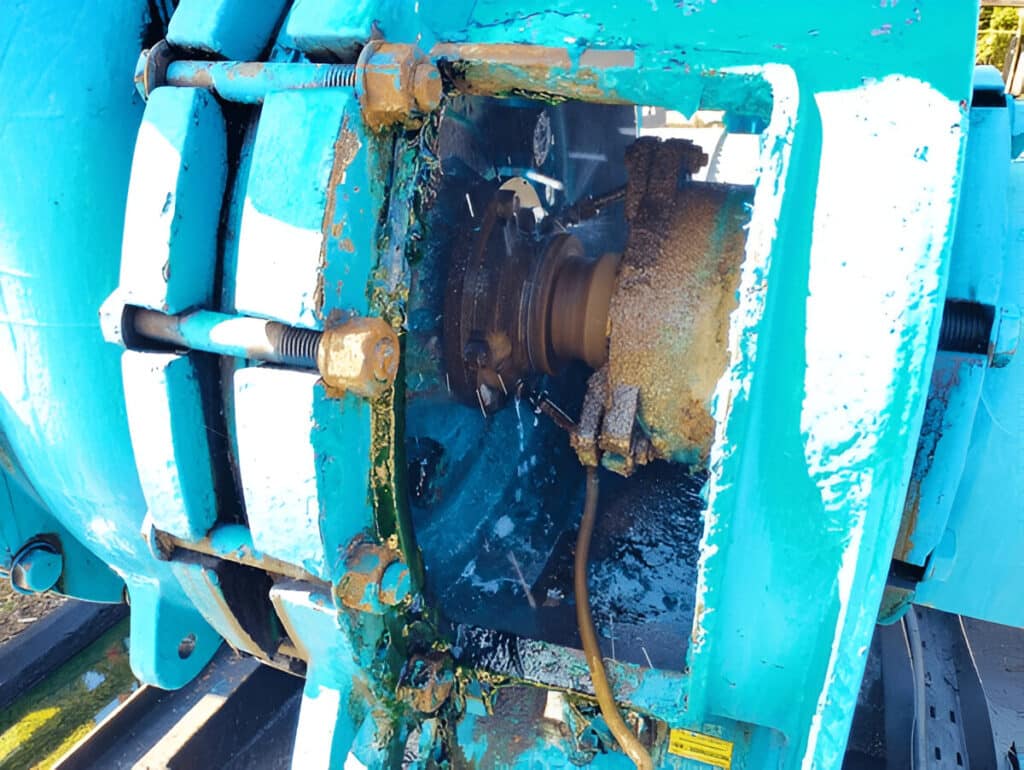
Visual Leakage
One of the most apparent signs of mechanical seal failure is visible leakage from the seal area. While a properly functioning seal should prevent any fluid from escaping, a compromised seal may allow product, flushing fluid, or barrier fluid to leak out. This leakage can range from a slow drip to a steady stream, depending on the severity of the seal damage.
Visual inspection of the seal and surrounding area can often reveal evidence of leakage, such as:
- Accumulation of fluid on or around the seal gland
- Fluid dripping or spraying from the seal
- Stains, residue, or crystallized product on seal components
- Wet or contaminated surfaces near the seal
Unusual Noises
Another potential indicator of mechanical seal problems is the presence of abnormal noises emanating from the seal or surrounding equipment. Some common noise-related symptoms of seal failure include:
- Squealing or high-pitched whistling sounds, which may indicate dry running or lack of lubrication
- Grinding, scratching, or metal-on-metal contact noises, suggesting seal face damage or misalignment
- Pulsating or intermittent noises that coincide with shaft rotation, possibly due to seal face deformations or rotating equipment issues
- Loud banging, knocking, or clanking sounds, potentially caused by excessive vibration or loose components
Excessive Vibration
Mechanical seals are precision components that require proper alignment and smooth, balanced rotation to function effectively. Excessive vibration can disrupt this delicate balance, leading to accelerated wear, seal face damage, and premature failure. Vibration-related seal issues can manifest in several ways:
- Visibly shaking or oscillating seal components
- Abnormal movement of the shaft or coupling
- Loose, rattling, or displaced seal hardware
- Fluctuations in seal leakage or performance
Overheating
Mechanical seals rely on a thin fluid film between the seal faces for lubrication and heat dissipation. When a seal begins to fail, this fluid film can break down, causing increased friction and heat generation at the seal interface. Overheating can lead to a range of seal failure modes, including:
- Thermal distortion or warping of seal faces
- Blistering, cracking, or heat checking of seal face materials
- Degradation or breakdown of elastomers and secondary seals
- Coking or carbonization of process fluids
- Increased wear and abrasion of seal components
Seal Face Damage
Seal face damage is one of the key indicators of mechanical seal failure. A variety of different issues on the seal faces can point to problems with the seal. Some common examples of seal face damage include:
- Grooves or notches: Deep grooves, notches, or striations on the seal faces are often caused by abrasive particles or debris getting trapped between the faces.
- Uneven wear track: If the wear track on the seal face is not uniform and even, it indicates that the faces are not maintaining proper contact. Uneven wear accelerates seal deterioration.
- Fractures or cracks: Seal faces can develop fractures or cracks due to thermal or mechanical shocks, excessive pressure, or improper installation.
- Chipping: Chipping of the seal faces, especially around the edges, weakens the seal and creates potential leak paths. Chipping is often the result of improper handling during installation.
- Heat checking: A network of fine cracks on the seal face, known as heat checking, occurs when the faces are exposed to rapid temperature changes. This is more common with hard face materials.
- Coking: Coking refers to a buildup of hardened, carbonaceous material on the seal faces. It is caused by overheating of certain process fluids and indicates the seal is operating outside its temperature limits.
- Blistering: Some seal face materials can develop blisters or pits when exposed to corrosive chemicals or electrolysis.
- Fretting: Fretting corrosion appears as a red or black oxidation on the seal faces, caused by minor vibrations between the faces.
Contamination
In addition to seal face damage, contamination of the sealing surfaces is another frequent contributor to premature seal failure. Contaminants interfere with the proper operation of the seal faces, leading to increased wear and leakage. Common types of contamination include:
- Carbon dust: Carbon dust can be generated by friction in the seal cavity or by the breakdown of carbon-based seal face materials. This fine dust gets trapped between the seal faces, causing abrasive wear.
- Product buildup: Process fluids, especially in crystallizing or polymerizing services, can solidify on the seal faces during periods of low flow or standstill. Product buildup holds the faces open, creating a leak path.
- Atmospheric contaminants: If the seal is exposed to the environment, airborne dust, dirt, and moisture can enter the seal cavity and contaminate the faces.
- Lubricant breakdown: In seals that use a barrier fluid or lubricating film, the fluid can break down over time, producing contaminants that damage the seal faces and inhibit proper lubrication.
Changes in Performance
In addition to the previously mentioned symptoms, mechanical seal failure can also manifest through changes in overall seal performance. These changes may be gradual or sudden, and can include:
- Increased leakage rates
- Difficulty maintaining desired pressure or flow
- Frequent adjustments or repairs needed
- Reduced sealing effectiveness or product contamination