Proper alignment between the motor and driven equipment is critical in industrial machinery applications. Misalignment, even by a fraction of a millimeter, can lead to issues like excessive vibration, premature bearing failure, and reduced efficiency, ultimately resulting in unplanned downtime and costly repairs. As technology advances, alignment techniques have evolved from straightforward methods using basic tools to sophisticated laser-based systems that provide unparalleled precision.
In this blog post, we will take an in-depth look at the three primary types of motor misalignment – angular, parallel, and combination misalignment. We will then explore the most common alignment techniques employed in the field, from the simple straight edge and feeler gauge method to advanced laser alignment systems, discussing the advantages and limitations of each approach.
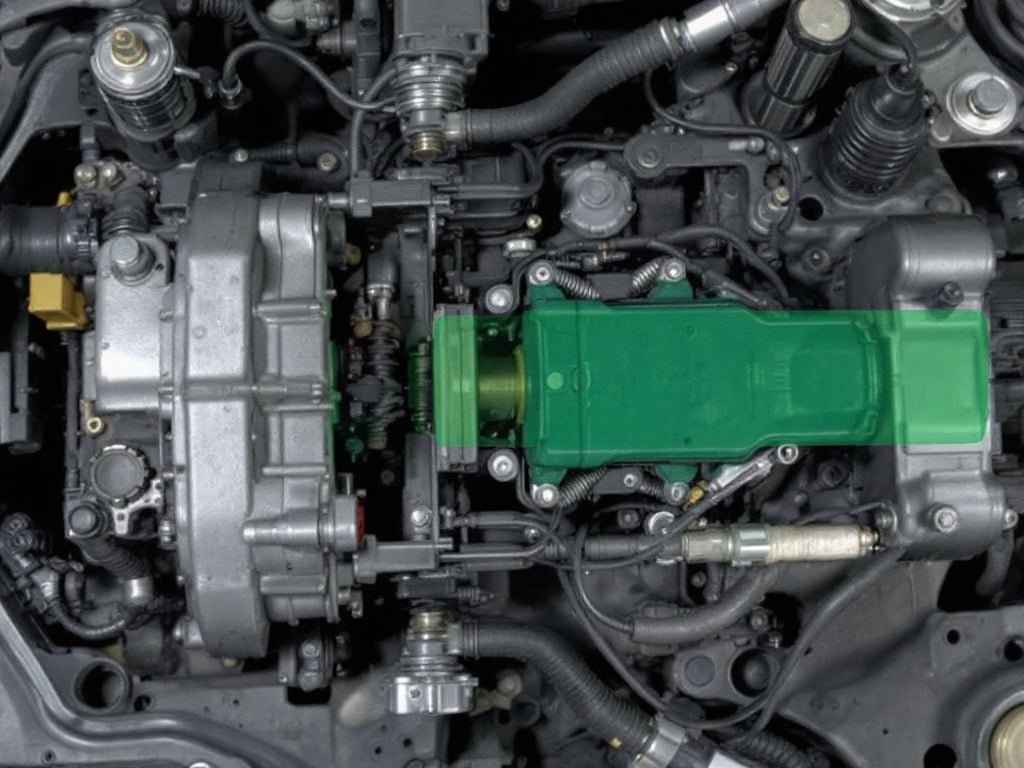
Types of Motor Misalignment
Misalignment between the motor shaft and the driven equipment can lead to a host of issues including excessive vibration, premature bearing failure, seal leakage, and coupling damage.
There are three main types of misalignment that can occur:
Angular Misalignment
In angular misalignment, the centerlines of the motor and driven shafts intersect, but they are not parallel. Picture two lines that cross each other at an angle.
This crossing angle between the shafts causes a bending moment in the coupling during each rotation. The coupling is constantly flexing back and forth as it tries to accommodate the misalignment.
Angular misalignment is usually caused by machines that are not on the same horizontal plane due to improper shimming or a non-level foundation. Picture one machine that sits slightly higher than the other.
The stress from repeated flexing can lead to premature coupling failure. It also transmits damaging cyclical forces to the motor and equipment bearings and seals.
Parallel (Offset) Misalignment
With parallel misalignment, also known as offset misalignment, the motor and driven shaft centerlines are parallel but they are offset from each other. Envision two lines that are on the same plane but do not intersect.
This offset between the shafts causes the coupling to constantly stretch and compress as it rotates, like an accordion. The coupling is always trying to compensate for the gap between the shafts.
Parallel misalignment often results from the motor and driven equipment being shifted horizontally relative to each other. This could be due to incorrect placement during installation or a shifting foundation.
The constant stretching and compressing of the coupling from parallel misalignment accelerates wear. It also places alternating tensile and compressive loads on the shafts, bearings and seals with each rotation.
Combination Misalignment
In the real world, most shaft misalignment is a combination of both angular and parallel misalignment. The motor shaft is at an angle to the driven shaft centerline and there is also an offset between them.
Combination misalignment incorporates the harmful effects of both angular and parallel misalignment. The coupling endures both angular distortion and axial displacement concurrently as it rotates.
As with the individual misalignment types, combination misalignment can arise from imprecise installation, degraded foundations, or improper shimming. It subjects the entire mechanical system to damaging cyclical stresses.
Techniques for Motor Alignment
Straight Edge and Feeler Gauge Method
One of the most basic motor alignment methods uses simple tools – a straight edge and a set of feeler gauges. The straight edge, typically a precision-ground metal ruler, is placed across the coupling connecting the motor to the driven equipment. Feeler gauges, which are thin metal blades of precise thicknesses, are then used to measure any gaps between the coupling faces and the straight edge.
By taking measurements at the top, bottom, and sides of the coupling on both the motor side and equipment side, the offset and angular misalignment can be determined. Shims are then added or removed under the motor or equipment feet to bring the coupling halves into alignment per the equipment specs. The straight edge and feeler gauge method can be effective for some applications but its accuracy is limited, especially for equipment requiring precision alignment.
Dial Indicator Method
A step up in precision from straight edges and feeler gauges is the dial indicator alignment method. Dial indicators are measuring tools with a plunger that moves a dial face to show displacement, typically in increments of 0.001 inch or finer.
To carry out alignment, a pair of dial indicators are mounted on brackets attached to one half of the coupling. The plungers are positioned to contact the face and rim of the other coupling half. As the shafts are rotated together, the dial indicators show the amount of offset or angular misalignment at various positions which can be recorded on an alignment datasheet.
Shimming and adjustments are made to the motor or equipment until the dial indicators show the coupling is aligned within tolerance throughout a full rotation. While more time consuming than the straight edge method, dial indicator alignment provides greater accuracy suitable for many industrial applications. However, long spans between the motor and equipment can reduce accuracy.
Laser Alignment Systems
For the highest precision, laser alignment systems are the preferred technique. These systems use laser transmitters and receivers mounted to the motor and equipment shafts. The laser transmitter emits a plane or line of laser light which is picked up by the receiver.
Special software analyzes the laser readings throughout a full shaft rotation to calculate the vertical and horizontal angularity and offset misalignment. It then provides a visual readout showing exactly how much and where shims or adjustments are needed to precisely align the shafts.
The main drawback of laser alignment is the higher up-front cost of the equipment. However, for precision applications where alignment is critical, the investment can pay off in longer equipment life, reduced vibration, and maintenance savings over time. Many laser systems also offer additional capabilities such as geometric measurements of turbine bores and machine tool ways.