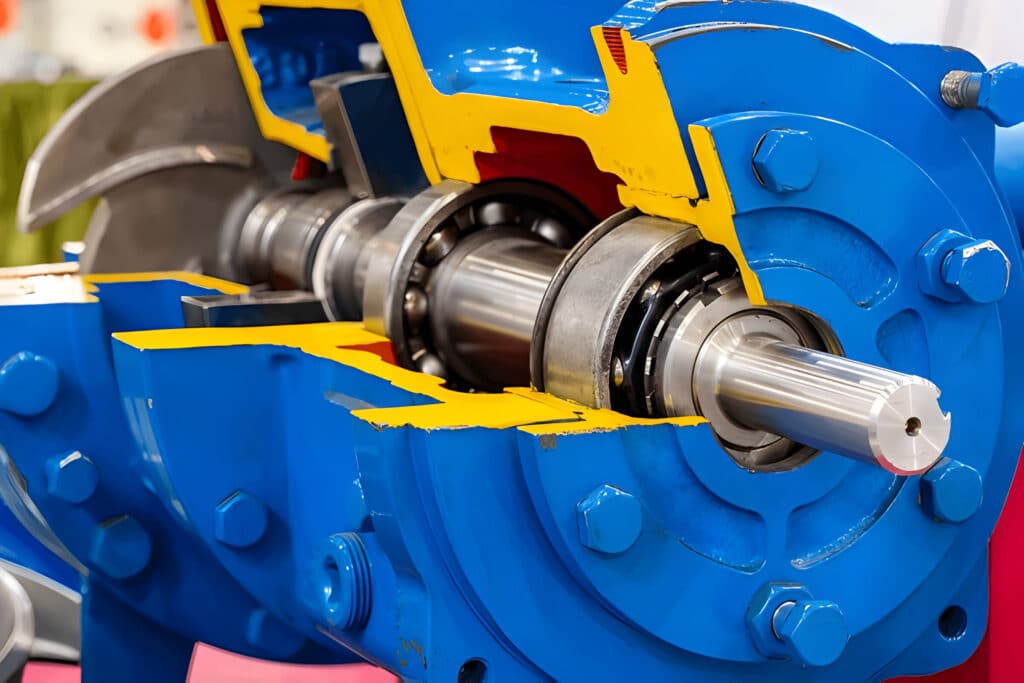
What Are Centrifugal Pumps
Centrifugal pumps are a common type of pump that utilizes the transfer of rotational energy from an impeller to increase the pressure and flow rate of a fluid. These pumps are used in a wide range of applications, including water supply, chemical processing, and industrial markets. The key component of a centrifugal pump is the impeller, which is a rotating disc with curved vanes that create a low-pressure zone at the pump inlet and a high-pressure zone at the outlet.
Centrifugal pumps are known for their simple design, which consists of a volute casing that houses the impeller and directs the fluid flow from the suction port to the discharge port. The impeller is mounted on a shaft that is driven by an electric motor or other power source. As the impeller rotates, it imparts kinetic energy to the fluid, which is then converted to pressure energy as the fluid flows through the volute casing and out the discharge port.
How Do Centrifugal Pumps Work
Centrifugal pumps work by converting the mechanical energy of a rotating impeller into kinetic energy, which is then used to pump fluids. The impeller, a key component of the pump, consists of curved vanes that spin rapidly within the pump casing. As the impeller rotates, it creates a low-pressure zone at the center, drawing fluid into the pump through the suction port.
The fluid enters the eye of the impeller and is captured by the rotating vanes. As the fluid moves outward along the vanes, it gains velocity and pressure. The centrifugal force generated by the rotating impeller pushes the fluid through the pump casing and into the discharge port, where it exits the pump at a higher pressure than when it entered.
Design of Centrifugal Pumps
The design of centrifugal pumps varies depending on the specific application and the type of fluid being pumped. However, most centrifugal pumps consist of two main components:
Volute
The volute is a spiral-shaped casing that surrounds the impeller. Its primary function is to collect the fluid discharged from the impeller and guide it towards the discharge port. The volute is designed to gradually increase in cross-sectional area, which helps to convert the fluid’s velocity into pressure.
Diffuser
In some centrifugal pump designs, a diffuser is used instead of a volute. The diffuser is a set of stationary vanes that surround the impeller. As the fluid moves through the diffuser, the vanes guide the flow and help to convert the fluid’s velocity into pressure. Diffusers are commonly used in multi-stage centrifugal pumps.
Parts of Centrifugal Pumps
Centrifugal pumps consist of several key components that work together to ensure efficient and reliable operation:
Impeller
The impeller is the rotating component of the pump that generates the centrifugal force necessary to move the fluid. It consists of a set of curved vanes that are designed to draw the fluid in and accelerate it outwards. Impellers can be made from various materials, such as cast iron, stainless steel, or composite materials, depending on the application and the type of fluid being pumped.
Diffuser or Volute Casing
The diffuser or volute casing is the stationary component that surrounds the impeller. Its primary function is to collect the fluid discharged from the impeller and guide it towards the discharge port. The casing also helps to convert the fluid’s velocity into pressure.
Shaft and Shaft Sleeves
The shaft is the rotating component that connects the impeller to the motor. It is supported by bearings and sealed to prevent leakage. Shaft sleeves are often used to protect the shaft from wear and corrosion, especially when pumping abrasive or corrosive fluids.
Bearings
Bearings are used to support the shaft and ensure smooth rotation. They can be either ball bearings or sleeve bearings, depending on the application and the load requirements.
Mechanical Seals
Mechanical seals are used to prevent leakage along the shaft. They consist of two mating surfaces, one stationary and one rotating, that are held together by spring pressure. Mechanical seals are widely used in centrifugal pumps due to their reliability and ability to handle a wide range of fluids and pressures.
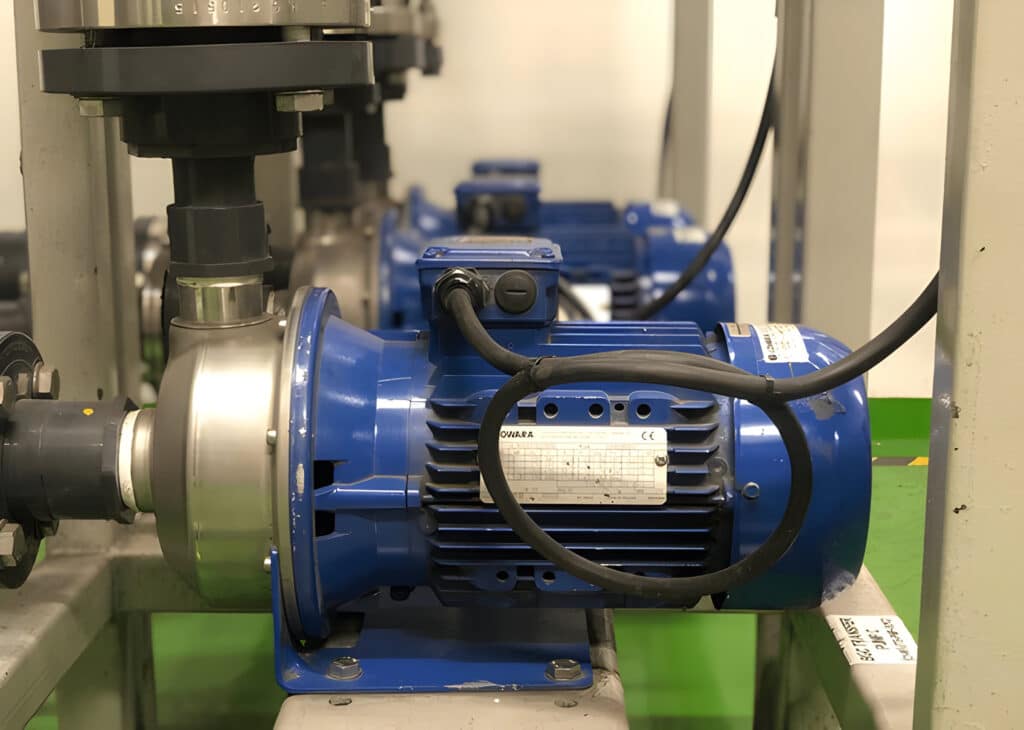
Types of Pump
There are two main types of pumps: positive displacement pumps and centrifugal pumps. Positive displacement pumps work by physically moving a fixed amount of fluid with each cycle, while centrifugal pumps use the kinetic energy of a spinning impeller to push fluid through the pump.
Positive Displacement Pump
Positive displacement pumps are a type of pump that moves fluid by repeatedly enclosing a fixed volume and moving it mechanically through the system. They are typically used for high-pressure, low-flow applications and can handle viscous liquids. Examples of positive displacement pumps include progressive cavity pumps, diaphragm pumps, and Air Motor pumps.
Centrifugal Pump
- Single-stage Centrifugal Pumps: These pumps have a single impeller and are best suited for low to moderate pressure applications. They are commonly used in water supply, irrigation, and industrial markets.
- Multi-Stage Centrifugal Pumps: These pumps feature multiple impellers in series, each stage increasing the pressure of the fluid. Multistage pumps are used when higher pressures are required, such as in boiler water supply and high-pressure cleaning applications.
- Axial-Flow Centrifugal Pumps: Also known as propeller pumps, these pumps have an axial design where the impeller pushes the fluid along the axis of the shaft. They are commonly used in applications with high flow rates and low head requirements, such as flood control and irrigation.
- Radial-Flow Centrifugal Pumps: In these pumps, the fluid enters the impeller axially and is discharged radially, perpendicular to the shaft. Radial-flow pumps are suitable for high-pressure applications and can handle a wide range of fluids, including clean liquids, chemicals, and hot water.
Advantages of Centrifugal Pumps
- Simple design: Centrifugal pumps have fewer moving parts compared to positive displacement pumps, which makes them easier to manufacture, operate, and maintain.
- High efficiency: Centrifugal pumps can achieve high efficiencies, especially when operating at their best efficiency point (BEP).
- Wide range of applications: Centrifugal pumps can handle a wide variety of liquids, including water, chemicals, and even some viscous fluids.
- Low cost: Due to their simple design and high production volumes, centrifugal pumps are generally less expensive than other types of pumps.
- Smooth flow: Centrifugal pumps provide a steady, non-pulsating flow, which is essential for many applications.
Disadvantages of Centrifugal Pumps
- Limited suction lift: Centrifugal pumps have a limited suction lift capability, which means they must be located close to the fluid source or require priming.
- Low efficiency at off-design conditions: Centrifugal pumps are most efficient when operating at their best efficiency point (BEP). Efficiency drops significantly when operating at flow rates or pressures away from the BEP.
- Not suitable for high-viscosity fluids: Centrifugal pumps are not well-suited for pumping high-viscosity fluids, as the increased fluid resistance can significantly reduce the pump’s efficiency and performance.
- cavitation risk: Centrifugal pumps are susceptible to cavitation, which occurs when the fluid’s pressure drops below its vapor pressure, leading to the formation of vapor bubbles that can damage the pump.
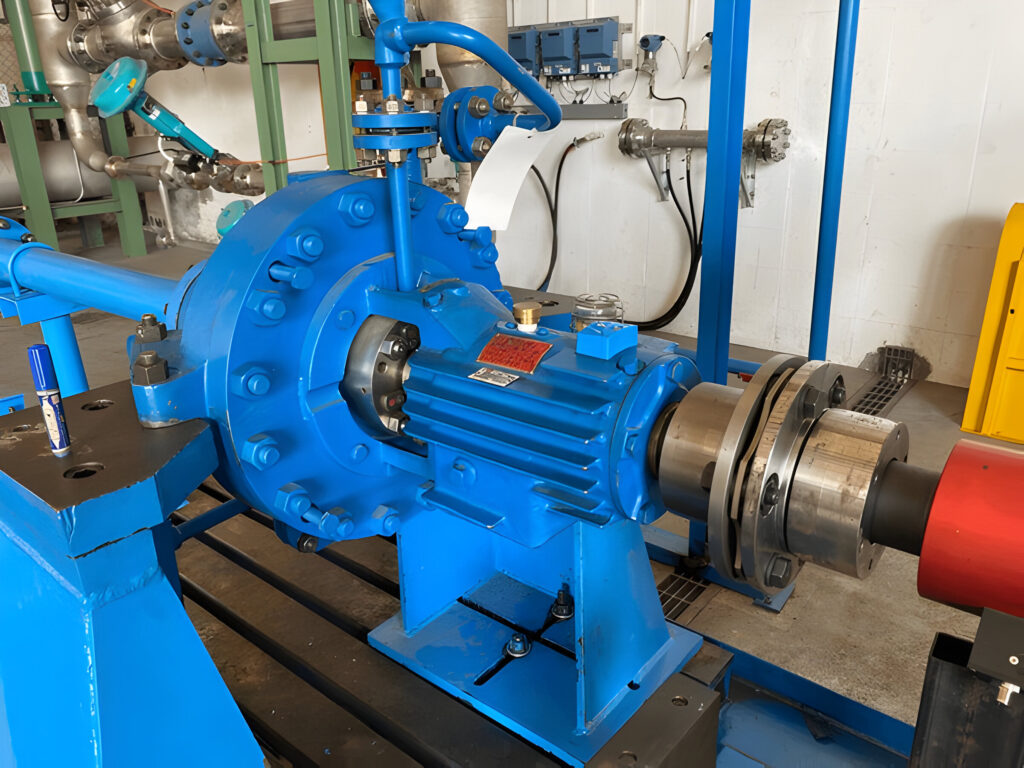
Centrifugal vs Positive Displacement Pumps
Factor | Centrifugal Pumps | Positive Displacement Pumps |
---|---|---|
Operating Principle | Uses kinetic energy to move fluids by accelerating them radially outward | Moves fluids by physically displacing them with a reciprocating or rotary mechanism |
Flow Rate | Provides a continuous, stable flow; flow rate varies with discharge pressure | Delivers a constant flow rate regardless of discharge pressure |
Efficiency | High efficiency for low-viscosity fluids; efficiency decreases with increasing viscosity | Maintains high efficiency for both low and high-viscosity fluids |
Pressure | Generates high pressure; suitable for high head applications | Generates high pressure; ideal for high-pressure applications |
Fluid Handling | Handles clean, low-viscosity fluids with few solids; not suitable for shear-sensitive fluids | Handles a wide range of fluids, including viscous, shear-sensitive, and abrasive fluids |
Maintenance | Low maintenance requirements due to simple design and fewer moving parts | Higher maintenance requirements due to more complex design and moving parts |
Cost | Lower initial cost and lower energy consumption for low-viscosity applications | Higher initial cost but more energy-efficient for high-viscosity applications |
Common Applications | Water supply, irrigation, cooling systems, boiler feed, and general industrial applications | Chemical processing, oil and gas, food and beverage, pharmaceuticals, and metering applications |
ANSI vs API Pumps
Factor | ANSI Pumps | API Pumps |
---|---|---|
Application | General industrial, chemical processing, water treatment | Oil and gas, petrochemical, refineries |
Design | Standardized dimensions and interchangeable parts | Customized for specific applications |
Operating Conditions | Moderate temperatures and pressures | High temperatures, pressures, and flow rates |
Materials | Cast iron, stainless steel, ductile iron | Carbon steel, stainless steel, duplex, alloy 20 |
Seal Chamber | Smaller, limited space for seals and flush plans | Larger, accommodates various seals and flush plans |
Efficiency | Moderate efficiency due to standardized design | Higher efficiency due to customized design |
Maintenance | Easier maintenance due to interchangeable parts | More complex maintenance due to customized parts |
Cost | Lower initial cost and replacement part cost | Higher initial cost and replacement part cost |
Centrifugal Pump vs Centripetal Pump
Factor | Centrifugal Pump | Centripetal Pump |
---|---|---|
Energy Transfer | Converts rotational energy into kinetic energy of the fluid | Converts kinetic energy of the fluid into pressure energy |
Impeller Design | Curved vanes that push fluid outward from the center | Straight vanes that guide fluid inward towards the center |
Fluid Flow | Radial flow from the center towards the outer edge of the impeller | Axial flow from the outer edge towards the center of the impeller |
Pressure Generation | Generates pressure by increasing fluid velocity and then converting it to pressure in the volute casing or diffuser | Generates pressure by directly converting fluid velocity into pressure |
Applications | Wide range of applications, including water supply, chemical processing, and industrial markets | Limited applications, mainly in specialized fields such as aerospace and certain industrial processes |
Efficiency | Generally higher efficiency due to the effective conversion of rotational energy to fluid kinetic energy | Lower efficiency compared to centrifugal pumps due to the direct conversion of kinetic energy to pressure |
Maintenance | Relatively simple design, easier to maintain and repair | More complex design, requiring specialized maintenance and repair |
Cost | Generally more cost-effective due to their widespread use and simpler design | Higher costs associated with their specialized nature and complex design |
Applications for Centrifugal Pumps
- Water supply and treatment: Centrifugal pumps are commonly used for pumping water in municipal water supply systems, irrigation, and water treatment plants.
- HVAC systems: Centrifugal pumps are used in heating, ventilation, and air conditioning systems to circulate water or other heat transfer fluids.
- Chemical processing: Centrifugal pumps are used to transfer chemicals in various processing industries, such as petrochemicals, pharmaceuticals, and food processing.
- Oil and gas industry: Centrifugal pumps are used for various applications in the oil and gas industry, such as crude oil transfer, pipeline boosting, and injection systems.
- Power generation: Centrifugal pumps are used in power plants for feedwater systems, cooling water circulation, and condensate transfer.
Operational Factors of Centrifugal Pumps
Throttling Flowrates
Throttling is a common method used to control the flow rate in centrifugal pump systems. By adjusting the discharge valve, the flow rate can be reduced while maintaining a constant pump speed. This allows for greater flexibility in meeting varying demand requirements. However, throttling can also lead to increased energy usage and reduced pump efficiency, especially when operating far from the pump’s best efficiency point (BEP).
Head – Flow Curves
The head-flow curve is a graphical representation of a centrifugal pump’s performance, illustrating the relationship between the total head (pressure) and the flow rate. The shape of the head-flow curve varies depending on the pump type, impeller design, and other factors. Operating a pump too far from its BEP can result in reduced efficiency, increased wear, and potential damage to the pump components.
Viscosity
The viscosity of the fluid being pumped is another critical factor in centrifugal pump operation. As fluid viscosity increases, the pump’s performance decreases due to increased friction losses and reduced flow velocity. Centrifugal pumps are generally best suited for low to medium viscosity fluids, such as water, oils, and some chemicals.
Horsepower
The horsepower requirements of a centrifugal pump depend on factors such as flow rate, head, fluid density, and pump efficiency. Selecting a pump with the appropriate horsepower rating is crucial for ensuring efficient operation and avoiding motor overload. Additional horsepower may be required when pumping high viscosity fluids or when operating at high flow rates and pressures. Proper sizing and selection of the pump and motor can help optimize energy usage and reduce maintenance costs over the life of the system.
FAQs
Why can’t centrifugal pumps handle air?
Centrifugal pumps are designed to pump liquids, not gases. When air enters a centrifugal pump, it can cause the pump to lose prime and stop pumping. This is because the air disrupts the continuous flow of liquid through the pump, reducing its efficiency and performance.
Is a centrifugal pump AC or DC?
Centrifugal pumps can be driven by either AC (alternating current) or DC (direct current) motors. The choice between AC and DC depends on the specific application, power source availability, and control requirements. AC motors are more commonly used due to their simplicity, reliability, and lower cost, while DC motors offer better speed control and are suitable for battery-powered applications.