The machinery industry faces significant challenges with traditional sealing methods, leading to excessive emissions, high energy consumption, and frequent maintenance issues. These problems not only impact operational efficiency but also pose environmental concerns.
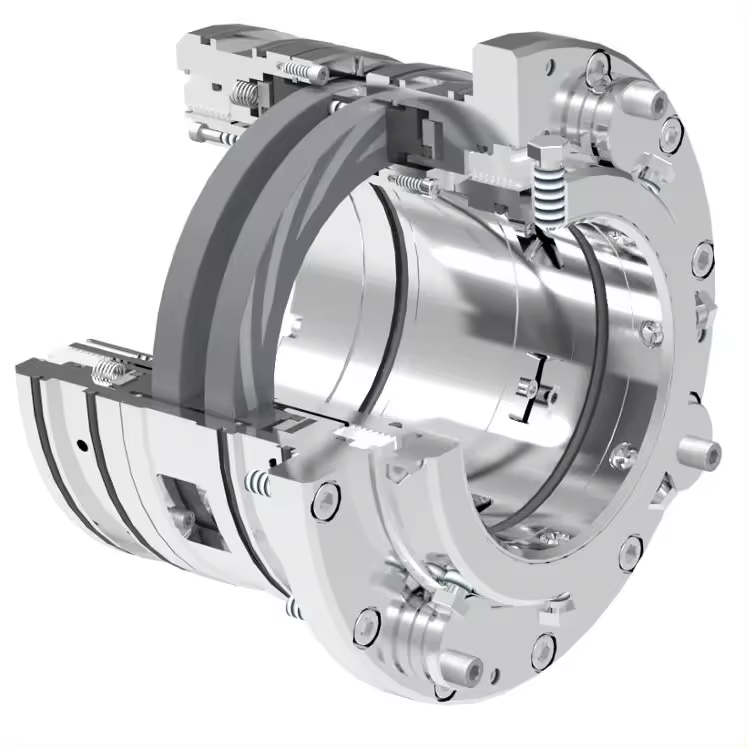
What is a Dry Gas Seal
Fortunately, dry gas seals offer a superior solution. By utilizing advanced technology and innovative design, dry gas seals effectively address the shortcomings of conventional seals, providing enhanced reliability, improved durability, and simplified maintenance.
A dry gas seal is a specialized mechanical seal that utilizes pressurized gas to create a seal between rotating and stationary components in turbomachinery such as compressors, turbines, and pumps. Unlike traditional contacting seals like carbon rings or segmented bushings that rely on contact between surfaces, dry gas seals maintain a small gap between the rotating and stationary faces.
This gap, typically measured in microns, is filled with clean, dry gas that is maintained at a pressure slightly higher than the process fluid pressure. This pressurized gas film acts as a barrier, preventing process fluid from escaping while allowing the rotating component to spin freely with minimal friction and heat generation.
How Dry Gas Seals Work
The working principle of a dry gas seal is based on creating a stable, high-pressure gas film between the rotating and stationary seal faces.
When the machine is at rest, the seal faces are in contact with each other, held closed by springs and gas pressure. As the shaft begins to rotate, a small amount of high-pressure gas is injected between the seal faces through restrictive orifices in the primary ring.
As the gas enters the sealing interface, it creates a thin, high-pressure film that lifts the primary ring away from the mating ring, creating a gap of a few microns. This gas film acts as a lubricating and sealing medium, allowing the mating ring to rotate freely with minimal friction while preventing the leakage of process gas.
Types of Dry Gas Seals
Single Seals
Single dry gas seals consist of a single seal face and are the simplest configuration. They are designed to handle moderate pressure differentials and are commonly used in applications where the sealed gas is clean and dry. Single seals are cost-effective and require minimal space, making them a popular choice for many industrial applications.
Double Seals
Double dry gas seals feature two seal faces arranged in series, providing an additional layer of protection against leakage. The space between the two seal faces is typically pressurized with a barrier gas, such as nitrogen, to prevent process gas from escaping to the atmosphere. Double seals are ideal for applications with higher pressure differentials or where increased reliability is required.
Tandem Seals
Tandem dry gas seals combine the benefits of single and double seals. They consist of two single seals mounted back-to-back, with a common stationary seal face between them. The space between the seals is vented to a flare or recovery system. Tandem seals provide the highest level of safety and reliability, making them suitable for critical applications or processes involving hazardous or toxic gases.
Advantages of Dry Gas Seals
- Reduced Emissions: Dry gas seals minimize leakage, resulting in significantly lower emissions compared to other sealing technologies.
- Lower Energy Consumption: The non-contacting nature of dry gas seals results in minimal friction and heat generation, leading to lower energy consumption and improved overall system efficiency.
- Improved Reliability: Dry gas seals have fewer moving parts and are less susceptible to wear and tear than mechanical seals.
- Enhanced Durability: The materials used in dry gas seals, such as silicon carbide and tungsten carbide, are highly resistant to wear, corrosion, and high temperatures. This durability extends the service life of the seals, reducing replacement costs and minimizing process interruptions.
- Elimination of Oil Contamination: Unlike oil-lubricated seals, dry gas seals do not require an oil supply system.
- Simplified Maintenance: Dry gas seals require minimal maintenance compared to other sealing technologies. The absence of an oil supply system and the reduced wear on seal faces simplify maintenance procedures and lower associated costs.
Disadvantages of Dry Gas Seals
- Sensitivity to Contamination: Dry gas seals are highly sensitive to contaminants in the process gas, such as dirt, dust, and liquids. These contaminants can damage the seal faces and compromise the sealing performance.
- Limited Ability to Handle Liquids: Dry gas seals are designed to operate with clean, dry gases. The presence of liquids in the process gas can lead to seal failure and leakage.
- Higher Initial Cost: The sophisticated design and high-quality materials used in dry gas seals often result in a higher initial cost compared to other sealing technologies.
- Sensitivity to Operating Conditions: Dry gas seals are sensitive to changes in operating conditions, such as pressure, temperature, and gas composition. Deviations from the specified design conditions can affect seal performance and lead to premature failure.
- Temperature Limitations: Dry gas seals have a limited operating temperature range compared to some other sealing technologies. The materials used in the seal faces and secondary seals can degrade at high temperatures, limiting their application in processes with extreme heat.