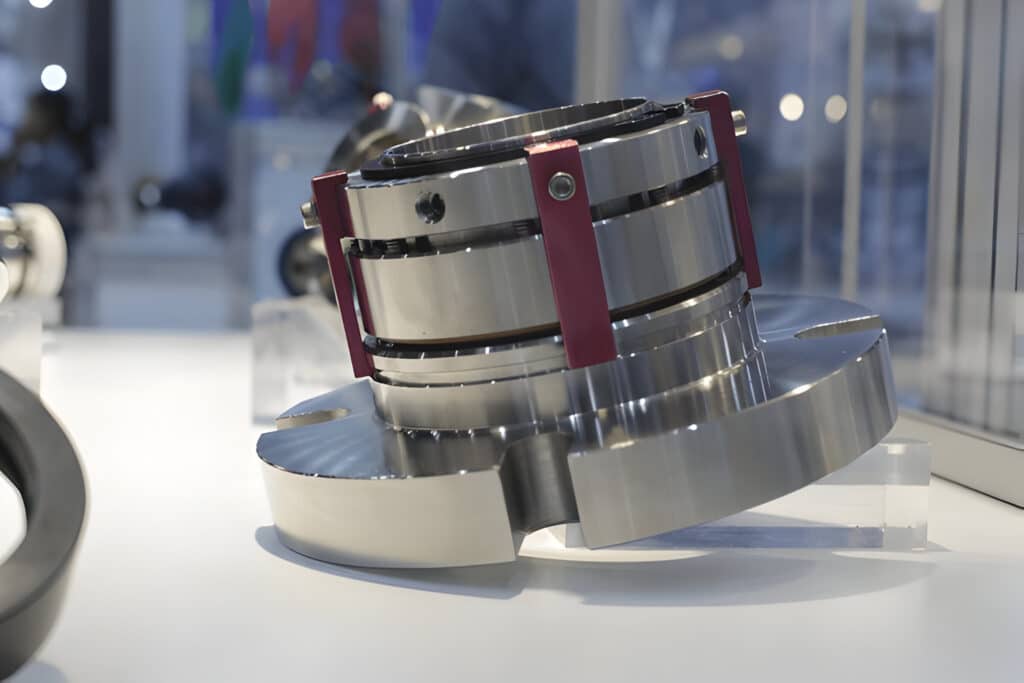
What Are Dry Running Mechanical Seals
Dry running mechanical seals are specialized sealing devices designed to operate without the need for external lubrication or a liquid film between the seal faces. These seals are engineered to withstand the challenges of dry running conditions, such as increased friction and heat generation. Dry running mechanical seals are commonly used in applications where the presence of a liquid barrier fluid is not feasible or desirable, such as in mixers, agitators, and certain pump types.
How Do Dry Running Mechanical Seals Work
The working principle of dry running mechanical seals relies on the careful selection of seal face materials that can withstand dry running conditions. These materials, such as silicon carbide, tungsten carbide, and carbon graphite, possess excellent tribological properties, allowing them to maintain a low coefficient of friction and minimize wear during dry operation.
In a dry running mechanical seal, the stationary and rotating seal faces are pressed together by spring force and hydraulic pressure, creating a tight seal that prevents fluid leakage. The seal faces are lapped to a high degree of flatness, ensuring optimal contact and sealing performance. As the shaft rotates, the seal faces generate frictional heat, which is dissipated through the seal components and the surrounding environment.
Features of Dry Running Mechanical Seals
- Specialized seal face materials: Dry running mechanical seals utilize advanced materials like silicon carbide, tungsten carbide, and carbon graphite for their seal faces. These materials exhibit excellent wear resistance, thermal conductivity, and self-lubricating properties, enabling them to operate effectively in dry conditions.
- Robust seal design: The overall design of dry running mechanical seals is engineered to withstand the challenges of dry operation. This includes optimized geometry, precise face lapping, and spring loading mechanisms that maintain proper face contact and sealing force.
- Heat dissipation features: To manage the heat generated during dry running, these seals incorporate features such as heat-dissipating fins, thermal conductive components, and optimized fluid flow paths to facilitate efficient heat transfer away from the seal faces.
- Compatibility with various fluids: Dry running mechanical seals are designed to handle a wide range of fluids, including abrasive, viscous, and corrosive media. The selection of seal face materials and secondary sealing components ensures compatibility and reliable performance in diverse applications.
Advantages of Dry Running Mechanical Seals
- Elimination of external lubrication: Dry running mechanical seals operate without the need for an external lubrication system or barrier fluid. This simplifies the overall system design, reduces maintenance requirements, and eliminates the risk of contamination associated with barrier fluids.
- Reduced operating costs: By eliminating the need for barrier fluids and associated support systems, dry running mechanical seals help reduce initial installation costs and ongoing operating expenses. This includes savings on fluid procurement, storage, and disposal, as well as reduced maintenance costs related to barrier fluid systems.
- Increased reliability and service life: Dry running mechanical seals are designed to withstand the challenging conditions of dry operation, resulting in improved reliability and extended service life compared to conventional wet seals. The advanced materials and robust design of these seals minimize wear, leakage, and premature failure.
- Compatibility with various applications: Dry running mechanical seals are suitable for a diverse range of industrial applications, including mixers, agitators, pumps, and other rotating equipment. They can handle various fluids, temperatures, and pressure conditions, making them a versatile sealing solution.
Applications of Dry Running Mechanical Seals
- Mixers and agitators: Dry running mechanical seals are commonly used in mixers and agitators, especially in the pharmaceutical, food, and chemical industries. These applications often require dry running capabilities to prevent product contamination and ensure process purity.
- Pumps handling viscous or abrasive fluids: In pump applications where the pumped fluid has a high viscosity or contains abrasive particles, dry running mechanical seals provide reliable sealing performance without the need for an external barrier fluid. This helps prevent seal face damage and extends seal life.
- Vacuum and high-temperature applications: Dry running mechanical seals are well-suited for vacuum and high-temperature applications where the use of a liquid barrier fluid is not feasible. The specialized materials and design of these seals enable them to withstand extreme conditions while maintaining sealing integrity.
- Flue gas desulfurization systems: In flue gas desulfurization (FGD) systems, dry running mechanical seals are used to seal the slurry pumps and agitators. These seals operate reliably in the harsh, abrasive environment of FGD systems, ensuring efficient and environmentally compliant operation.
FAQs
How Long Can Mechanical Seals Run Dry?
Most mechanical seals can function between 10 seconds to 2 minutes without liquid.
What Is the Difference between Wet Mechanical Seal and Dry Mechanical Seal?
The primary difference between wet and dry mechanical seals lies in their lubrication and cooling mechanisms.
Wet mechanical seals rely on a liquid barrier fluid, such as water, oil, or a specially formulated lubricant, to lubricate and cool the seal faces during operation. The barrier fluid forms a thin film between the stationary and rotating seal faces, reducing friction and heat generation.
Dry mechanical seals are designed to operate without the need for an external barrier fluid. They rely on advanced seal face materials with self-lubricating properties, such as carbon graphite or silicon carbide, to minimize friction and wear during dry running. Dry mechanical seals also incorporate design features that promote efficient heat dissipation, such as heat-dissipating fins or thermal conductive components.