The spring inside a mechanical seal is a critical component that keeps the seal faces pressed together to prevent leaks in rotating equipment like pumps and mixers. This spring provides constant force that maintains face contact even when equipment is idle or operating at low pressure. Without this spring force, the seal faces would separate and allow fluid to escape, causing equipment failure and safety hazards.
Springs work alongside fluid pressure to create the perfect balance for sealing. They push hard enough to prevent leaks but not so hard that they cause excessive wear. The spring also compensates for normal wear of the seal faces and small shaft movements that occur during operation.
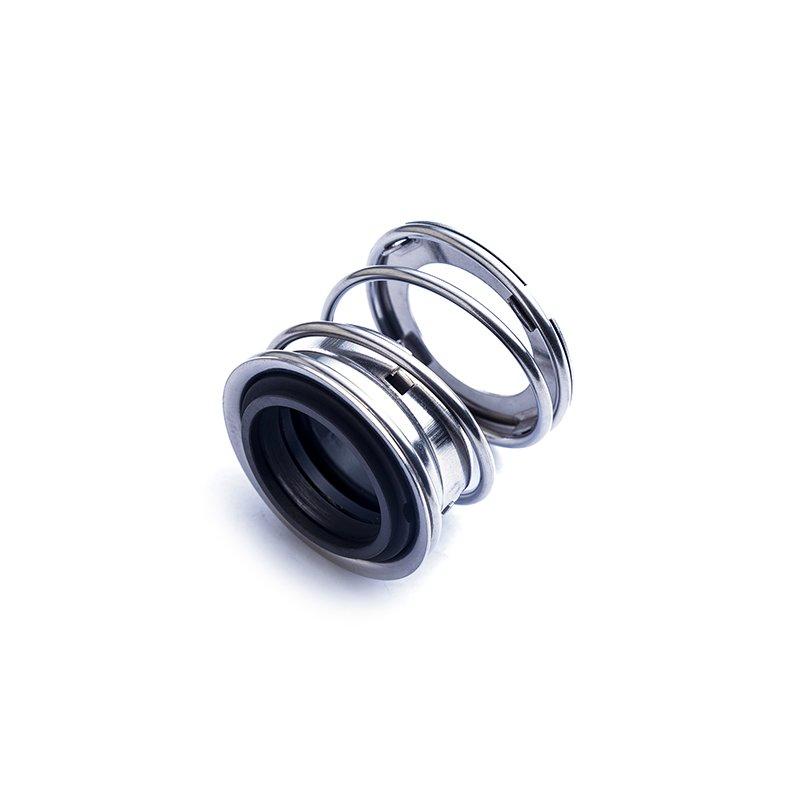
The Role of Springs in Mechanical Seals
Springs serve three essential functions in mechanical seals.
- They maintain constant face contact between the rotating and stationary seal faces. This closing force stays active whether the pump is running or stopped, preventing leaks during startup and shutdown when fluid pressure is minimal.
- Springs compensate for wear and movement that naturally occur during operation. As seal faces wear down over thousands of hours of use, the spring extends to maintain contact. The spring also absorbs small shaft deflections caused by bearing tolerances or temperature changes.
- Springs balance the fluid forces trying to push the seal faces apart. During operation, pumped fluid creates pressure that attempts to separate the faces. The spring pushes back against this pressure, maintaining just enough force to allow a microscopic film of fluid for lubrication while preventing bulk leakage.
Types of Springs Used in Mechanical Seals
Mechanical seals use four main spring types, each with distinct advantages for different applications.
Single Coil Spring (Single Spring Seal)
Single coil springs use one large spring to provide all the sealing force. The robust design features thick wire that resists corrosion and handles dirty fluids well. Solids and sludge have fewer places to accumulate compared to multiple small springs.
However, single springs don’t distribute force as evenly around the seal faces. All force comes from one point, which can create slight tilting or uneven wear patterns. These springs also require more axial space, making the entire seal assembly longer.
At high shaft speeds, single springs can experience unwinding from centrifugal forces. Manufacturers counter this by designing the spring direction to resist unwinding during rotation. Despite these limitations, single springs remain popular for dirty or viscous services where clogging is a concern.
Multiple Coil Springs (Multi-spring Seal)
Multi-spring seals distribute several small springs evenly around the seal circumference. This arrangement provides uniform face loading, keeping the seal faces parallel and evenly pressed together. Better pressure distribution improves sealing performance and creates more consistent wear patterns.
Multiple springs create a more compact design than single springs. The shorter springs fit into less axial space while still providing adequate force. Manufacturers can use the same spring design across different seal sizes by simply changing the number of springs.
The main disadvantage is vulnerability to clogging and corrosion. Small-diameter spring wire has more surface area exposed to attack. Abrasive particles, scale, or viscous fluids can pack between the coils more easily than with a single robust spring.
Wave Spring
Wave springs compress a flat metal ribbon formed into peaks and valleys around a circle. This design achieves the required spring force in minimal axial space. Wave springs are often half the height of traditional coil springs with similar force output.
The compact design comes with trade-offs. Wave springs have a steep force-versus-deflection curve. Small amounts of face wear or thermal expansion cause large changes in spring force. This means the closing force drops off more quickly as faces wear compared to coil springs.
Wave springs excel in applications with tight space constraints. When equipment has shallow seal chambers that can’t accommodate traditional springs, wave springs provide the solution.
Bellows (Metal Bellows Seals)
Metal bellows serve dual purposes as both spring and secondary seal. The accordion-like structure compresses and extends to provide spring force while eliminating the need for dynamic O-rings on the shaft. This removes a common failure point in traditional seals.
Bellows distribute force uniformly around the entire seal face circumference. The design inherently self-balances pressure without requiring multiple individual springs. This uniform loading improves face contact and reduces wear.
These seals excel in extreme temperature applications. Metal bellows handle both cryogenic and high-temperature services where rubber components would fail. They also prevent shaft fretting and seal hang-up problems associated with sliding O-rings.
The main challenges involve spring rate control and cost. Bellows thickness and convolution count must balance pressure capability against spring stiffness. Too stiff and the bellows won’t flex properly. Too soft and they won’t maintain adequate face contact.