Compressor seals are critical components in rotating equipment, ensuring safe and efficient operation by preventing leaks and maintaining pressure. In the demanding environment of industrial machinery, these sealing systems must withstand extreme conditions while delivering reliable performance.
This article explores the fundamentals of compressor seals, delving into their working principles, various types, key components, and support systems.
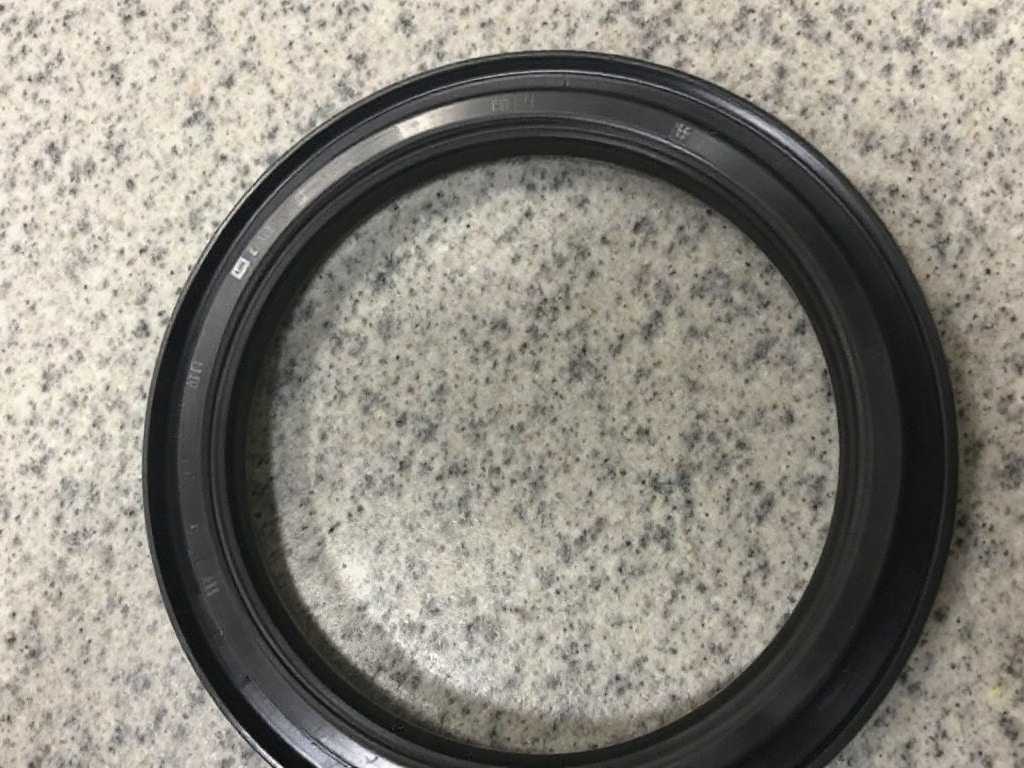
What Is a Compressor Seal
A compressor seal is a critical component in a compressor system that prevents the leakage of process gas or air from the compressor casing while the shaft rotates. Compressor seals maintain a barrier between the high-pressure gas inside the compressor and the atmosphere, ensuring efficient operation and preventing environmental contamination.
How Compressor Seals Work
Compressor seals operate by creating a barrier between the rotating shaft and the stationary compressor casing. This barrier is typically achieved through a combination of mechanical components, such as rotating and stationary seal faces, and a sealing fluid, such as oil or gas.
The rotating seal face is attached to the compressor shaft, while the stationary seal face is fixed to the compressor casing. As the shaft rotates, the seal faces maintain contact with each other, creating a seal that prevents leakage. The sealing fluid is used to lubricate and cool the seal faces, reducing friction and wear.
Types of Sealing Systems
Wet Sealing Systems
Wet sealing systems utilize a liquid, typically oil, to lubricate and cool the seal faces. The oil is circulated through the sealing system, providing a barrier between the process gas and the atmosphere. Wet seals are commonly used in applications where the process gas is compatible with the sealing oil and where the presence of oil in the process gas is acceptable.
Advantages of wet sealing systems include:
- Effective lubrication and cooling of seal faces
- Ability to handle high pressures and temperatures
- Relatively simple design and maintenance
Disadvantages of wet sealing systems include:
- Potential for oil contamination of the process gas
- Higher oil consumption and disposal costs
- Increased risk of oil leakage to the environment
Dry Sealing Systems
Dry sealing systems, also known as dry gas seals, use a pressurized gas, typically nitrogen or process gas, to create a barrier between the rotating and stationary seal faces. The gas is injected between the seal faces, creating a thin film that prevents contact and reduces friction.
Advantages of dry sealing systems include:
- No oil contamination of the process gas
- Lower power consumption due to reduced friction
- Longer seal life and reduced maintenance requirements
- Environmentally friendly, with no oil leakage risks
Disadvantages of dry sealing systems include:
- Higher initial cost compared to wet seals
- Increased complexity of the sealing system
- Requirement for a clean, dry gas supply for sealing
Seal Arrangements
Single Seals
Single seals have one set of seal faces – a rotating and stationary face – forming a single point of contact to prevent leakage. They are the simplest type of seal but have limited capability in high pressure or poor lubricating fluid applications.
Single seals are often used in clean, lubricating fluids at moderate pressures and temperatures. They require less support equipment and have a lower cost than multiple seal arrangements. However, if the single seal interface fails, process fluid can immediately leak to the atmosphere.
Tandem Seals
Tandem seals utilize two single seals mounted in series, with a buffer fluid between them maintained at a pressure lower than the process fluid. This arrangement provides redundancy – if the primary seal fails, the secondary seal contains the process fluid.
The two seals act independently – the primary seal absorbs the full pressure drop from the process fluid to the buffer fluid, while the secondary seal handles the smaller pressure difference from the buffer fluid to atmosphere. This allows each seal to be optimized for its specific pressure conditions.
Tandem seals are often used in more hazardous, higher pressure applications where additional safety and reliability are required. The buffer fluid between the seals can be monitored to detect primary seal leakage before an external leak occurs. However, tandem seals are more complex and costly than single seals.
Double Seals
Double seals also use two sets of seal faces, but with a barrier fluid between them maintained at a pressure higher than the process fluid. This ensures that if either seal fails, the higher pressure barrier fluid will leak into the process rather than allowing process fluid to escape.
The two seal stages work together to contain the barrier fluid. The inboard seal handles the pressure difference from the barrier fluid to the process, while the outboard seal handles the pressure drop from the barrier fluid to atmosphere.
Double seals provide maximum safety and emissions control and are used with hazardous, toxic or explosive process fluids. The barrier fluid is usually a clean, inert fluid compatible with the process. An external reservoir, circulation pump and heat exchanger are required to supply the pressurized barrier fluid.
Support Systems
Oil Seal Systems
Contacting wet seals require a lubricating fluid film between the seal faces to minimize wear and friction. In oil seal systems, this is provided by an oil circulated from an external reservoir.
The reservoir holds a supply of clean oil and incorporates conditioning elements like heaters or chillers to maintain the optimum oil viscosity. A circulation pump sends oil to the seal cavity, where it lubricates the faces and removes frictional heat. Flow controls and check valves maintain consistent oil flow and pressure.
Gas Seal Systems
Dry gas compressor seals use a pressurized gas, usually nitrogen, as the sealing medium between the faces instead of oil. This eliminates the complexities of oil systems and allows higher operating speeds and temperatures.
The gas is usually maintained at a pressure slightly higher than the process gas to ensure positive flow through the seal faces. A control panel meters sealing gas from a high pressure source, regulating its pressure and flow to the seal chamber.
Filters and demisters remove any particles or liquids from the gas supply to avoid contaminating the seal faces. Gas conditioning systems may heat the supply gas to prevent condensation of vapors from the process gas.
Tandem and double gas seals are used for maximum reliability in critical compressors. In a tandem arrangement, the secondary seal acts as a backup if the primary fails. A double gas seal maintains an inert barrier gas between the process and atmosphere for maximum emissions control.