Fiber packings are a critical sealing component in pumps, preventing fluid leakage and ensuring efficient operation. Choosing the right fiber packing material requires careful consideration of factors like fluid compatibility, operating conditions, and performance requirements.
This article dives into the principles behind how fiber packings seal, the various types of fiber materials used, their properties, and key criteria for selecting the optimal packing for a given application. By understanding these fundamentals, pump operators and maintenance personnel can make informed decisions to maximize pump reliability and service life.
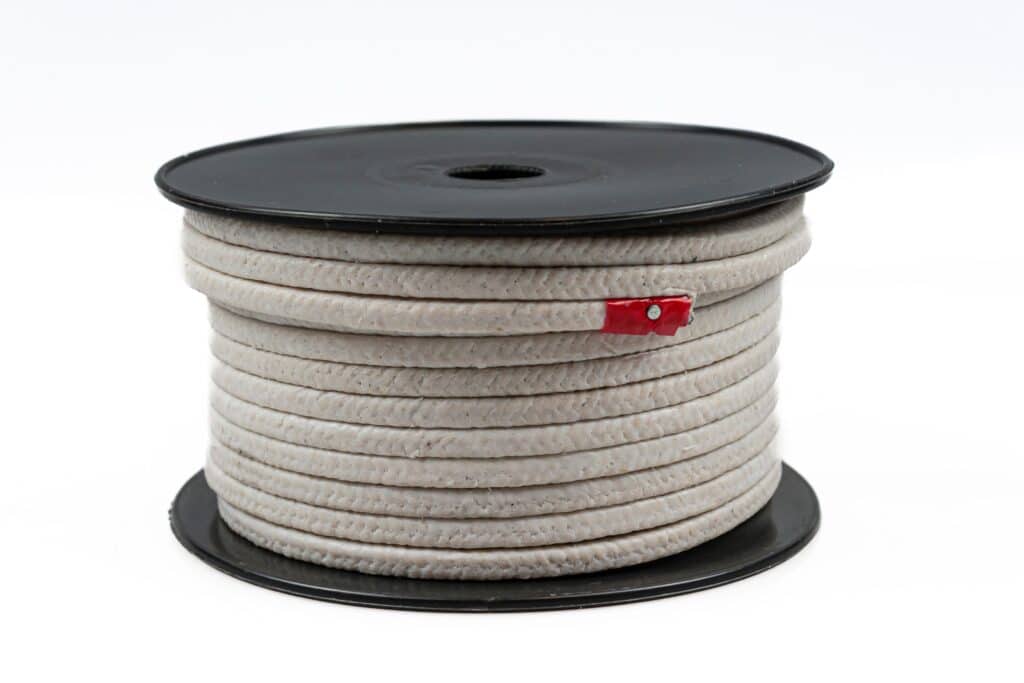
What Is a Fiber Packing
Fiber packing, also known as compression packing, is a type of mechanical seal used to control leakage in pumps, valves, and other rotary equipment. It consists of braided or twisted strands of flexible material that are compressed into the stuffing box, creating a seal between the rotating shaft and the stationary housing.
The primary function of fiber packing is to prevent fluid from escaping the system while allowing the shaft to rotate with minimal friction and wear. Fiber packings are commonly used in applications where a cost-effective and reliable sealing solution is required, such as in industrial pumps, mixers, and agitators.
Sealing Principles of Fiber Packings
Fiber packings achieve a seal through a combination of compression and controlled leakage. When the packing is properly installed and compressed, it conforms to the shape of the shaft and stuffing box, filling the gaps and creating a tight seal.
As the shaft rotates, a small amount of fluid is allowed to leak through the packing, which helps to lubricate and cool the sealing interface. This controlled leakage is essential for preventing excessive heat buildup and premature wear of the packing material.
The sealing performance of fiber packings depends on several factors, including:
- Packing density: The packing must be compressed to the appropriate density to ensure effective sealing without causing excessive friction or wear.
- Gland adjustment: The gland follower, which compresses the packing, must be properly adjusted to maintain the optimal packing density and compensate for wear over time.
- Packing material: The choice of packing material depends on the specific application requirements, such as temperature, pressure, and chemical compatibility.
- Shaft condition: A smooth, properly finished shaft surface is essential for achieving a reliable seal and minimizing packing wear.
Types of Fiber Materials
Fiber materials used in pump packings can be classified into four main categories: natural fibers, synthetic fibers, mineral fibers, and metal and ceramic fibers.
Natural Fibers
Natural fibers, such as cotton, flax, and hemp, are derived from plants. These fibers are biodegradable, renewable, and have good thermal insulation properties. However, they have limited chemical resistance and are not suitable for high-temperature applications.
Synthetic Fibers
Synthetic fibers are man-made materials, including polyester, nylon, and aramid. These fibers offer excellent chemical resistance, high strength, and good durability. They can withstand higher temperatures compared to natural fibers and are commonly used in pump packings for various industrial applications.
Mineral Fibers
Mineral fibers, such as asbestos and ceramic fibers, are inorganic materials with high heat resistance. Asbestos fibers were widely used in the past due to their excellent thermal and chemical resistance properties. However, due to health concerns, asbestos has been largely replaced by safer alternatives like ceramic fibers in modern pump packings.
Metal and Ceramic Fibers
Metal and ceramic fibers, such as stainless steel and glass fibers, offer high strength, excellent heat resistance, and good chemical compatibility. These fibers are often used in combination with other materials to create composite packings that can withstand extreme conditions in pumps handling aggressive fluids or operating at high temperatures.
Properties of Fiber Materials
- Thermal resistance: Ability to withstand high temperatures without degradation
- Chemical resistance: Resistance to various chemicals and corrosive fluids
- Tensile strength: Ability to withstand tensile stress without breaking
- Abrasion resistance: Resistance to wear caused by friction and abrasive particles
- Flexibility: Ability to bend and conform to the shape of the stuffing box
- Resilience: Ability to recover from compression and maintain sealing properties
- Dimensional stability: Resistance to changes in size and shape under varying conditions
- Moisture absorption: Ability to absorb or repel moisture, which can affect sealing performance
Selection Criteria for Fiber Packings
Fluid Type
The type of fluid being handled by the pump is a critical factor in selecting the appropriate fiber packing. Different fluids have varying chemical properties that can affect the packing material. For example, aggressive chemicals may degrade certain fibers, while abrasive particles can cause premature wear.
Temperature
The operating temperature of the pump is another important consideration when selecting fiber packings. High temperatures can cause some fibers to degrade or lose their sealing properties. For high-temperature environments, materials like ceramic fibers or graphite-based packings are often preferred.
Pressure
The operating pressure of the pump also influences the choice of fiber packing. High-pressure applications require packings with excellent mechanical strength and resistance to extrusion. Synthetic fibers, such as aramid or PTFE, are well-suited for high-pressure environments due to their superior strength and low creep properties.
Shaft Speed
The rotational speed of the pump shaft can affect the performance and wear rate of the fiber packing. High-speed applications generate more heat due to friction, which can lead to premature wear and leakage. In such cases, packings with good heat dissipation properties and low friction coefficients are preferred. Materials like graphite or PTFE-based packings are commonly used in high-speed applications.