A sealing gland is a critical component in various industrial applications, particularly in machinery that involves rotating shafts or reciprocating rods. These devices are designed to prevent leakage of fluids or gases while allowing the shaft or rod to move freely.
Sealing glands come in different types and configurations, each suited for specific operating conditions and media. In this blog post, we will delve into the fundamentals of sealing glands, exploring their construction and functionality.
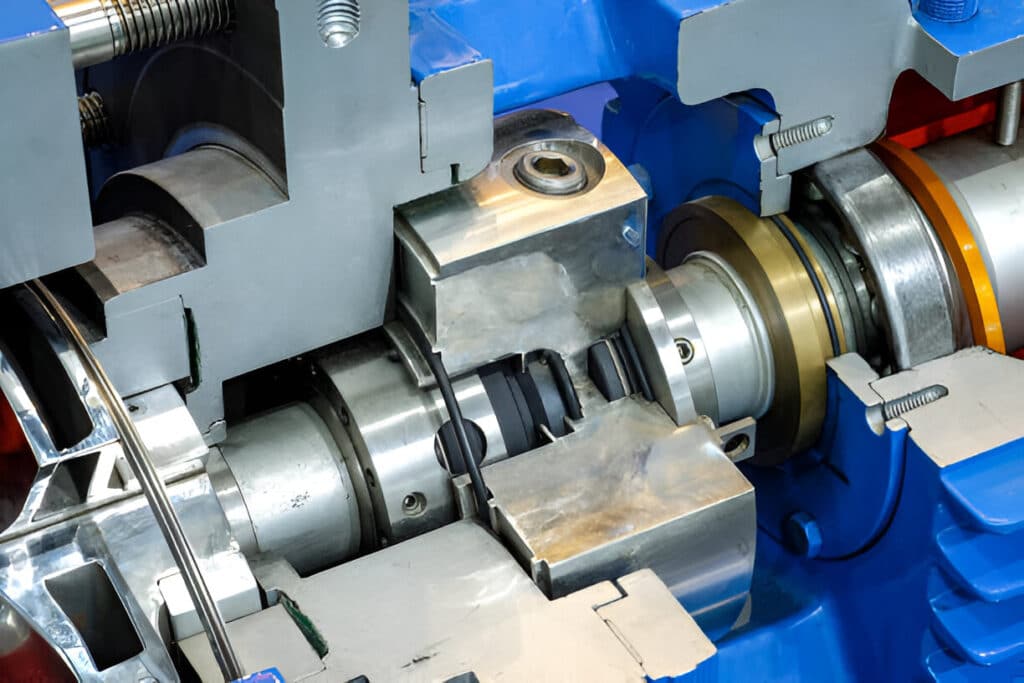
What Is a Sealing Gland
A sealing gland, also known as a stuffing box or packing gland, is a mechanical device used to seal the space around a rotating or reciprocating shaft where it passes through a housing or vessel wall. The primary function of a sealing gland is to prevent leakage of fluids, such as liquids or gases, from the inside of the equipment to the outside environment, while allowing the shaft to rotate or move freely.
The sealing gland assembly typically consists of a housing or stuffing box, which is a cylindrical cavity surrounding the shaft. Inside the stuffing box, a sealing material, such as braided packing or a mechanical seal, is compressed around the shaft to create a tight seal. The compression is usually achieved by tightening a gland follower or a set of adjustable bolts that apply pressure to the sealing material.
How Sealing Glands Work
Sealing glands are designed to prevent leakage of fluids or gases from rotating shafts in machinery. The primary components of a sealing gland include a stuffing box, packing material, and a gland follower. The stuffing box is a cylindrical cavity that surrounds the shaft, while the packing material is compressed within the stuffing box to create a tight seal around the shaft.
The gland follower, which is typically a ring-shaped component, is used to apply pressure to the packing material. This pressure is adjusted by tightening or loosening the gland follower, which in turn compresses or relaxes the packing material. The compression of the packing material against the shaft and the stuffing box walls creates a barrier that prevents fluid or gas from escaping. As the shaft rotates, the packing material remains stationary, maintaining contact with the shaft surface.
Advantages of Sealing Glands
Prevent Leakage
Sealing glands are designed to prevent leakage of fluids or gases from rotating or reciprocating shafts. By minimizing leakage, sealing glands help maintain system efficiency and reduce environmental impact.
Protect Equipment
Effective sealing glands protect equipment from contamination by preventing foreign particles from entering the system. This protection extends the life of bearings, shafts, and other critical components.
Reduce Maintenance
By preventing leakage and contamination, sealing glands reduce the need for frequent maintenance and repairs. This results in lower maintenance costs and increased equipment uptime.
Improve Safety
Sealing glands help prevent hazardous fluids or gases from escaping, enhancing workplace safety. They also reduce the risk of fire or explosion in environments with flammable materials.
Disadvantages of Sealing Glands
Friction and Heat Generation
Sealing glands, particularly gland packing, can generate friction and heat due to contact between the packing material and the shaft. This friction can lead to increased power consumption and wear on the shaft surface.
Regular Adjustment
Gland packing requires regular adjustment to maintain proper compression and prevent leakage. Over-tightening can cause excessive friction and heat, while under-tightening may result in leakage.
Limited Speed and Pressure
Sealing glands have limitations in terms of the maximum speed and pressure they can handle effectively. High-speed or high-pressure applications may require specialized sealing solutions.
Potential for Shaft Damage
Improper installation or adjustment of sealing glands can cause shaft damage, such as scoring or grooving. This damage can lead to premature shaft failure and increased maintenance costs.
Applications of Sealing Glands
Pumps
Sealing glands are commonly used in various types of pumps, including centrifugal, reciprocating, and rotary pumps. They prevent leakage of the pumped fluid and protect the pump’s internal components.
Valves
In valves, sealing glands are used to prevent leakage around the valve stem. They ensure proper sealing and maintain the valve’s functionality, especially in high-pressure or high-temperature applications.
Mixers and Agitators
Sealing glands are employed in mixers and agitators to seal the shaft entry point and prevent leakage of the mixed materials. They help maintain product purity and prevent contamination of the environment.
Compressors
In compressors, sealing glands are used to prevent leakage of the compressed gas and to protect the compressor’s internal components from contamination.
Comparing Gland Packing and Mechanical Seals
Feature | Gland Packing | Mechanical Seals |
---|---|---|
Leakage Control | Allows some leakage, which acts as lubrication | Provides superior leakage control with minimal to no leakage |
Pressure Handling | Suitable for low to medium pressures | Can handle higher pressures compared to gland packing |
Temperature Range | Limited temperature range, typically up to 260°C (500°F) | Wider temperature range, with some designs operating up to 425°C (800°F) |
Shaft Speed | Generally used for slower shaft speeds | Capable of sealing higher shaft speeds |
Maintenance | Requires frequent adjustments and replacements | Less frequent maintenance, but more complex when required |
Cost | Lower initial cost and simpler installation | Higher initial cost and more complex installation |
Seal Lifespan | Shorter lifespan due to wear and degradation | Longer lifespan with proper installation and maintenance |
Environmental Impact | Potential for greater environmental impact due to leakage | Minimal environmental impact due to superior leakage control |
Compatibility | Suitable for a wide range of fluids and applications | Specific designs required for different fluids and applications |
Adjustment | Allows for manual adjustment to compensate for wear | No manual adjustment possible, requiring seal replacement when worn |