Injectable packing is a cutting-edge sealing technology that has revolutionized the machinery industry. This innovative solution offers superior sealing performance and durability compared to traditional packing methods.
In this blog post, we will delve into the world of injectable packing, exploring its definition, types, installation process, advantages, and applications.
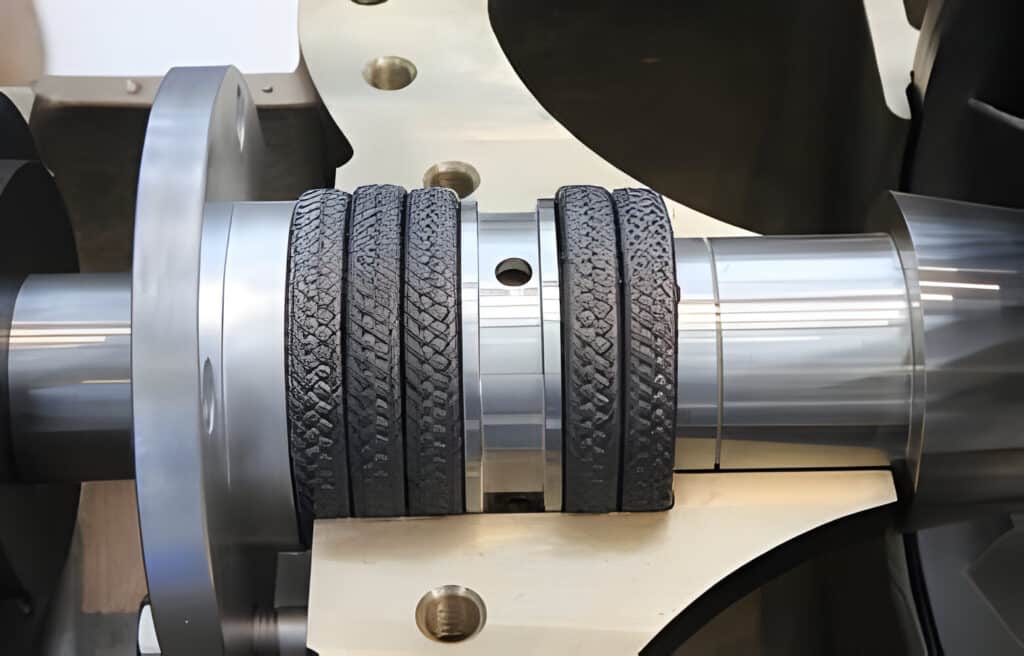
What Is Injectable Packing
Injectable packing, also known as injectable gland packing or injectable compression packing, is a sealing method used in various industrial applications to prevent leakage and maintain system integrity. This type of packing is composed of a pliable, deformable material that can be injected into the space around a shaft or stem, creating a tight seal between the moving and stationary components.
The injectable packing material is typically a blend of fibers, lubricants, and other additives that provide excellent sealing properties and durability. When injected under pressure, the packing material conforms to the contours of the shaft and the surrounding area, effectively filling any gaps or irregularities and creating a reliable seal.
Types of Injectable Packing
Graphite-Based Injectable Packing
Graphite-based injectable packing is a popular choice for high-temperature applications. This type of packing is made from a combination of graphite and other heat-resistant materials, such as carbon fibers or ceramics. Graphite-based packing offers excellent thermal stability, chemical resistance, and low friction properties, making it suitable for use in steam systems, valves, and pumps.
PTFE-Based Injectable Packing
PTFE (polytetrafluoroethylene) based injectable packing is known for its exceptional chemical resistance and low friction characteristics. This type of packing is composed of PTFE fibers and other additives that enhance its sealing performance. PTFE-based packing is ideal for applications involving aggressive chemicals, as it can withstand exposure to a wide range of substances without degradation.
Aramid-Based Injectable Packing
Aramid-based injectable packing is engineered for high-pressure and high-temperature applications. Made from synthetic aramid fibers, this type of packing offers superior strength, durability, and resistance to wear and abrasion. Aramid-based packing is commonly used in valves, pumps, and other rotating equipment in demanding industrial environments.
Hybrid Injectable Packing
Hybrid injectable packing combines the beneficial properties of multiple materials, such as graphite, PTFE, and aramid fibers. By leveraging the strengths of each material, hybrid packing can provide enhanced sealing performance, thermal stability, and chemical resistance. This type of packing is well-suited for applications that require a balance of different properties to ensure optimal sealing under various operating conditions.
Installation Process
Step 1: Surface Preparation
Before installing injectable packing, ensure that the surface is clean, dry, and free from debris, dirt, or grease. Use a wire brush or abrasive tool to remove any loose material or corrosion from the surface.
Step 2: Packing Injection
Inject the packing material into the designated area using a high-pressure injection gun. The injection process should be performed systematically, starting from one end and moving towards the other. Ensure that the packing material is evenly distributed throughout the area, filling any gaps or voids.
Step 3: Pressure Adjustment
Adjust the injection pressure according to the manufacturer’s specifications. The pressure should be high enough to ensure that the packing material penetrates deep into the surface but not so high that it causes damage or distortion. Monitor the pressure throughout the injection process to maintain consistency.
Step 4: Curing
After injection, allow the packing material to cure according to the manufacturer’s guidelines. Curing times can vary depending on the specific product and environmental conditions. During the curing process, the packing material will harden and form a stable, durable seal.
Step 5: Inspection and Testing
Once the packing material has cured, conduct a thorough inspection of the installation. Check for any gaps, voids, or inconsistencies in the packing material. Perform any necessary tests, such as pressure testing or leak detection, to ensure that the injectable packing is functioning correctly and providing an effective seal.
Advantages of Injectable Packing
Enhanced Sealing Performance
Injectable packing offers superior sealing performance compared to traditional packing methods. The injectable nature of the packing material allows it to conform to the shape of the stuffing box, effectively filling any gaps or irregularities.
Reduced Friction and Wear
The use of injectable packing significantly reduces friction and wear on the shaft and packing material. The packing is designed to provide optimal lubrication, minimizing heat generation and extending the life of both the packing and the shaft.
Increased Equipment Reliability
By providing a reliable seal and reducing wear, injectable packing contributes to increased equipment reliability. The improved sealing performance minimizes the occurrence of leaks, which can lead to unplanned downtime and production losses.
Simplified Maintenance
Injectable packing simplifies the maintenance process compared to traditional packing methods. The packing can be easily injected into the stuffing box without the need for extensive disassembly or equipment downtime.
Applications of Injectable Packing
Pumps
Injectable packing finds extensive use in various types of pumps, including centrifugal, reciprocating, and rotary pumps. It effectively seals the stuffing box, preventing leakage of the pumped fluid and ensuring optimal pump performance. The enhanced sealing capabilities of injectable packing make it particularly suitable for pumps handling abrasive, corrosive, or high-temperature fluids.
Valves
Injectable packing is commonly used in valves to provide a reliable seal between the valve stem and the body. It prevents leakage of the process fluid and maintains the integrity of the valve operation. The adaptability of injectable packing allows it to accommodate the movement of the valve stem while maintaining a tight seal, even under varying temperature and pressure conditions.
Agitators and Mixers
In agitators and mixers, injectable packing is employed to seal the shaft entry point and prevent the leakage of the mixed or agitated fluid. The packing material withstands the rotary motion of the shaft and the forces exerted by the fluid, ensuring a stable and efficient mixing process.
Compressors
Injectable packing is used in compressors to seal the shaft and prevent the leakage of compressed gases. It provides a reliable seal under the high pressures and temperatures encountered in compressor operations. The use of injectable packing helps maintain compressor efficiency, reduces energy losses, and minimizes the risk of environmental emissions.
Turbines
In turbines, injectable packing is utilized to seal the shaft and prevent steam or gas leakage. The packing material withstands the high rotational speeds and temperatures associated with turbine operation. By maintaining a reliable seal, injectable packing contributes to the efficient and safe functioning of turbines in power generation and other industrial applications.