EPR (Ethylene Propylene Rubber) and EPDM (Ethylene Propylene Diene Monomer) are two synthetic rubber compounds widely used in various industrial applications. While both materials share similarities in their composition and properties, they exhibit distinct differences that make them suitable for specific use cases.
This blog post will delve into the key distinctions between EPR and EPDM, focusing on their chemical structures, physical properties, and typical applications in the machinery industry.
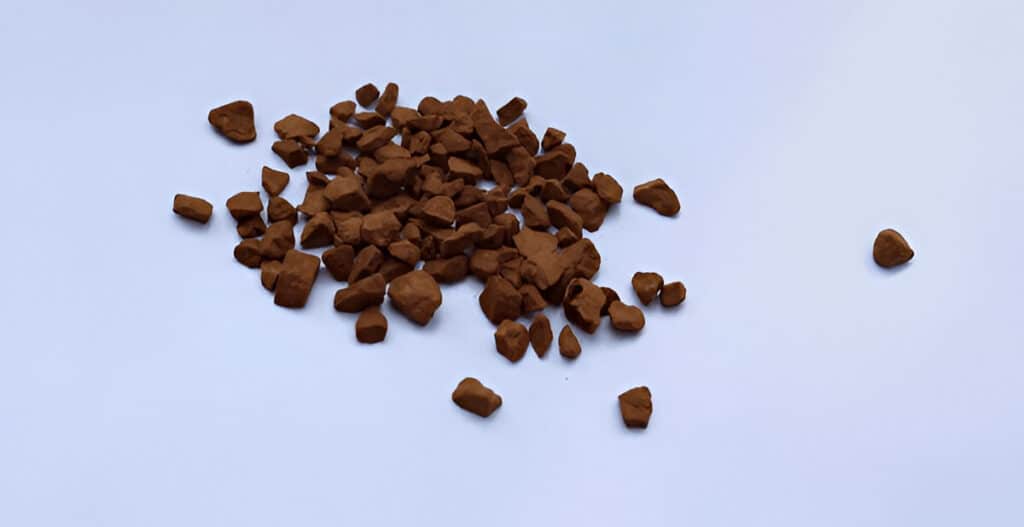
What Is EPR
EPR, or Ethylene Propylene Rubber, is a synthetic rubber copolymer consisting of ethylene and propylene monomers. This versatile rubber compound offers excellent resistance to water, steam, and many polar solvents. EPR exhibits notable performance in applications involving high temperatures, with an operational temperature range between -50°C and 150°C.
One of the key characteristics of EPR is its exceptional resistance to ozone, UV radiation, and weathering. This makes it an ideal choice for outdoor applications and environments where exposure to these elements is common. Additionally, EPR demonstrates good resistance to acids, alkalis, and some types of alcohol.
EPR finds widespread use in various industries, including the automotive, electrical, and seal industry. Its resistance properties and temperature range make it suitable for applications such as electrical insulation, seals, gaskets, and hoses.
What Is EPDM
EPDM, or Ethylene Propylene Diene Monomer, is another type of synthetic rubber that shares similarities with EPR. However, EPDM incorporates an additional diene monomer, which sets it apart from EPR in terms of properties and applications.
EPDM rubber exhibits excellent resistance to ozone, UV radiation, and weathering, making it suitable for outdoor applications. It also offers good resistance to water, steam, and mild acids. However, EPDM has limited resistance to oils, petroleum products, and aromatic hydrocarbons compared to EPR.
The temperature range for EPDM is slightly wider than EPR, with an operational range between -50°C and 150°C. This temperature resistance, combined with its excellent resistance to ozone and weathering, makes EPDM a popular choice for applications in the automotive industry, such as weather stripping, hoses, and seals.
Key Difference Between EPR and EPDM
Composition
EPR is an ethylene-propylene copolymer, while EPDM has an additional diene monomer incorporated into its structure.
Flexibility
From a functional standpoint, both EPR and EPDM exhibit excellent flexibility over a wide range of temperatures. However, EPDM maintains its flexibility better at lower temperatures due to its unique chemical structure.
Temperature Range
EPDM generally has a broader operating temperature range compared to EPR. EPDM can typically withstand temperatures from -40°C to 150°C.
EPR, while still offering good temperature resistance, typically has a slightly narrower operating range from -40°C to 130°C. It may not perform as well as EPDM in applications that involve constant exposure to high temperatures or steam.
Electrical Properties
EPR rubber exhibits excellent electrical insulation characteristics, making it a suitable choice for applications that require high resistance to current flow.
On the other hand, EPDM rubber has relatively lower electrical insulation properties compared to EPR. While EPDM still provides adequate electrical resistance for many applications, it may not be the ideal choice when exceptional electrical insulation is a primary requirement.
Curing Process
EPR rubber is typically cured using peroxide compounds, which create strong, stable cross-links between the polymer chains. Peroxide curing allows EPR to achieve excellent heat resistance, chemical resistance, and mechanical properties. The peroxide cure formulation used for EPR results in a rubber compound with superior performance characteristics.
In contrast, EPDM rubber can be cured using either peroxide or sulfur-based systems. Sulfur-cured EPDM is more common and provides good overall properties, while peroxide-cured EPDM offers enhanced heat resistance and better compression set resistance.
Performance Characteristics
EPR and EPDM exhibit distinct performance characteristics that set them apart. EPR rubber is known for its exceptional resistance to heat, steam, and aggressive chemicals. It maintains its mechanical properties over a wide temperature range and offers excellent resistance to polar solvents, acids, and bases. EPR’s chemical resistance profile includes resistance to mineral oils, vegetable oils, and aliphatic hydrocarbons.
EPDM rubber, on the other hand, is recognized for its outstanding resistance to weathering, ozone, and UV radiation. It provides excellent performance in outdoor applications and environments exposed to sunlight and atmospheric conditions. EPDM also offers good resistance to water, steam, and mild chemicals. However, its resistance to oils and hydrocarbons is relatively lower compared to EPR.
Applications
EPR rubber finds extensive use in the electrical and electronics industry, where its excellent electrical insulation properties are highly valued. It is commonly used in wire and cable insulation, electrical connectors, and sealing applications in demanding environments. EPR is also used in the nuclear industry due to its resistance to radiation.
EPDM rubber, with its exceptional weathering resistance and durability, is widely used in automotive and construction applications. It is a popular choice for weather seals, window and door seals, roofing membranes, and automotive hoses. EPDM’s resistance to water and steam makes it suitable for various sealing applications in the food and beverage industry. Its broad temperature range and good chemical resistance also make it applicable in industrial and manufacturing settings.