Oil and grease seals are critical components in machinery, but do you know the key differences between them? Using the wrong seal for your application can lead to leaks, contamination, and premature failure.
Without understanding the distinctions in primary function, structure, lubricant viscosity, shaft fit, speed ratings and temperature ranges, you risk choosing a seal that won’t provide optimal performance and protection. This can result in costly downtime and repairs.
In this article, we’ll break down the major differences between oil seals and grease seals. You’ll learn how to select the right type of seal based on your machinery’s specific requirements, ensuring reliable operation and extending equipment life.
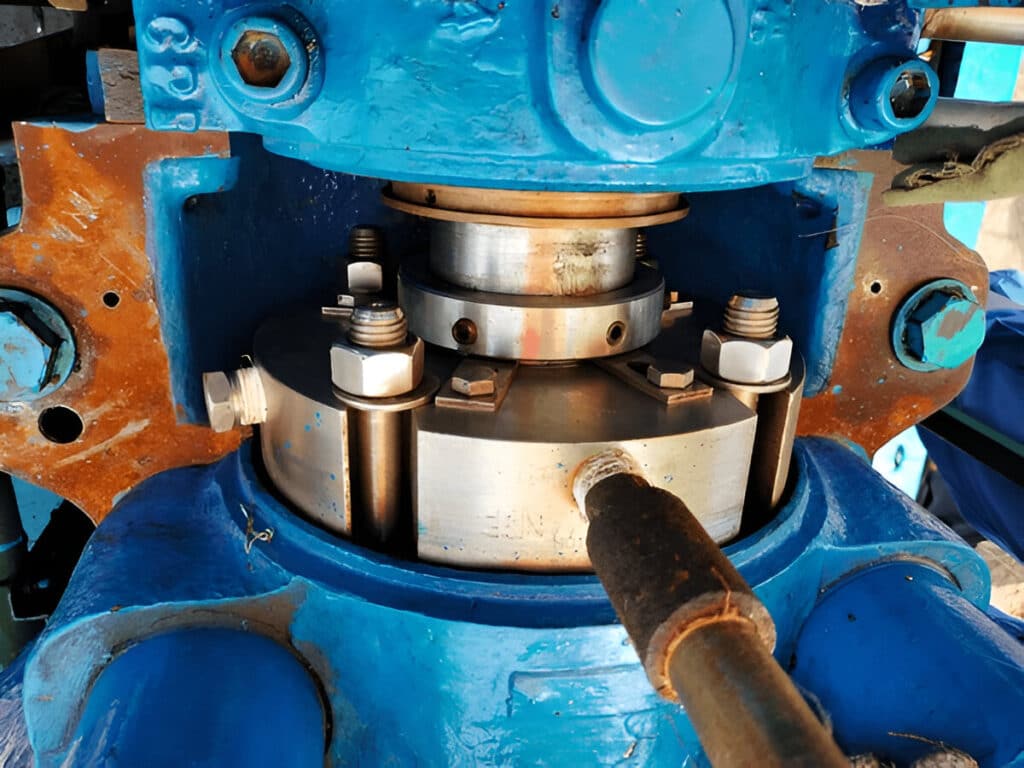
What is Oil Seal
An oil seal is a type of mechanical seal designed to prevent leakage of lubricating oil from a machinery component, such as a bearing housing or gearbox. Oil seals are typically made from elastomeric materials, such as nitrile rubber (NBR) or fluoroelastomer (FKM), and consist of a flexible sealing lip that maintains contact with a rotating shaft or other moving component. The primary function of an oil seal is to contain lubricating oil within a specific area while preventing the ingress of contaminants, such as dust, dirt, or moisture.
What is Grease Seal
A grease seal, also known as a bearing seal or lip seal, is a type of mechanical seal designed to retain grease within a bearing housing or similar application. Grease seals are typically made from elastomeric materials, such as nitrile rubber (NBR) or polyurethane (PU), and feature a flexible sealing lip that contacts a rotating shaft or other moving component. The primary function of a grease seal is to prevent the escape of grease from the bearing cavity while also preventing the ingress of contaminants, such as dust, dirt, or moisture.
Difference Between Oil Seal and Grease Seal
Primary Function
The primary function of an oil seal is to retain oil or other low-viscosity lubricants within a machine while allowing a rotating shaft to pass through.
The primary function of a grease seal is to retain grease within a bearing housing or similar assembly.
Structural Differentiation
Oil seals typically consist of a metal casing with an elastomeric sealing lip. The sealing lip is designed to maintain contact with a rotating shaft, preventing oil from escaping.
Grease seals often have a more complex structure, featuring multiple sealing lips or labyrinth designs to retain grease and exclude contaminants.
Viscosity of Lubricant
Oil seals are designed to work with lower viscosity lubricants, such as oil, which can easily flow and leak if not properly contained.
Grease seals, on the other hand, are intended for use with higher viscosity, semi-solid lubricants, such as grease, which are less likely to leak due to their thicker consistency.
Fit on Shaft
Oil seals require a smooth, precision-machined shaft surface or wear sleeve to function properly. The sealing lip must maintain circumferential contact with the shaft to prevent leakage.
Grease seals are more forgiving in terms of shaft surface finish and can tolerate some degree of shaft misalignment or runout.
Speed
Oil seals are typically better suited for high-speed applications, as they are designed to maintain a tight seal against low-viscosity lubricants even at elevated shaft speeds.
Grease seals, while capable of handling moderate speeds, may not perform as well as oil seals in high-speed applications due to the thicker nature of grease and its tendency to churn and heat up at high speeds.
Temperature
Most oil seals are made from synthetic elastomers such as nitrile, polyacrylate, silicone, or fluoroelastomers that can withstand temperatures from -40°F to 400°F (-40°C to 204°C).
Grease seals are usually made from similar materials but may have a more limited temperature range due to the thermal stability of the grease.