The gap between the faces of a mechanical seal, known as the sealing gap, is a critical aspect of seal design and operation. This minuscule space, typically measured in micrometers, plays a vital role in ensuring the proper functioning and longevity of mechanical seals in various industrial applications.
In this blog post, we will delve into the intricacies of the sealing gap, exploring its functions, the factors that influence its dimensions, and the challenges associated with maintaining an optimal sealing gap. By understanding these key aspects, engineers and maintenance professionals can make informed decisions to optimize seal performance and prevent costly failures.
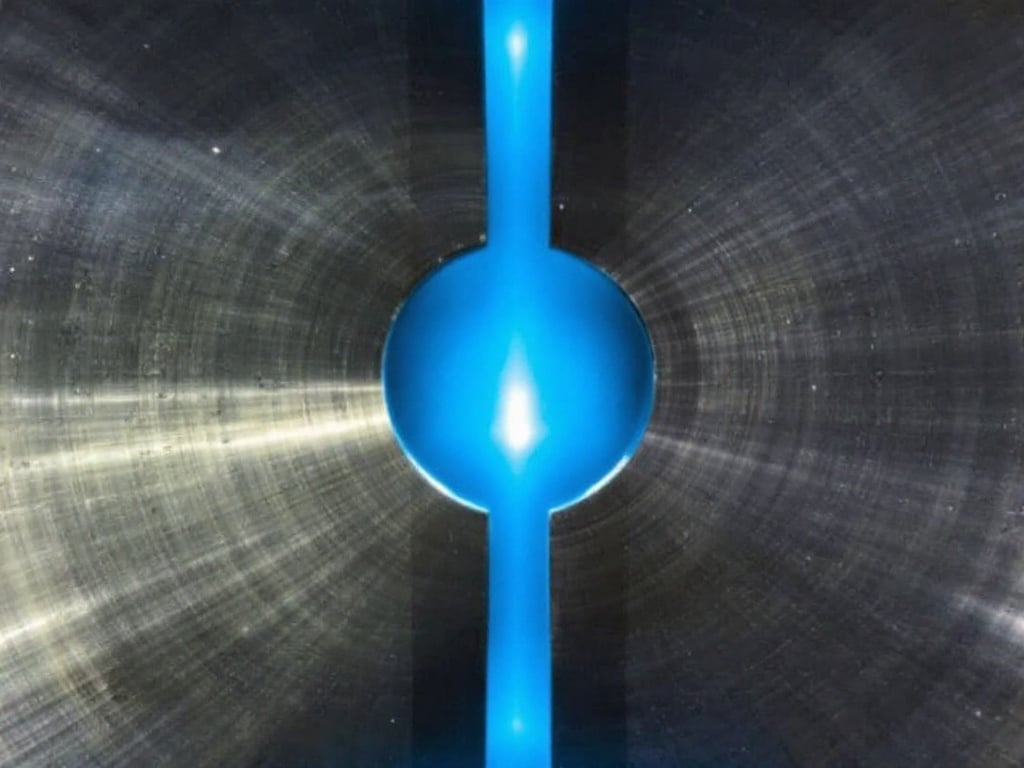
What Is the Sealing Gap
In mechanical seals, the sealing gap refers to the small space between the stationary and rotating faces of the seal. This gap is typically measured in microns (μm) and its size depends on various factors such as the seal design, materials used, operating conditions, and the fluid being sealed. Maintaining the optimal sealing gap is critical for the proper functioning and longevity of the mechanical seal.
The sealing gap is filled with a thin film of fluid, which can be the process fluid itself or an external barrier fluid in case of double seals. This fluid film helps to lubricate the seal faces, reduce friction and heat generation, and prevent direct contact between the faces, which would lead to rapid wear and seal failure.
Functions of Sealing Gap
The sealing gap serves several important functions in a mechanical seal:
- Lubrication: The fluid film in the sealing gap lubricates the seal faces, reducing friction and wear. Proper lubrication is essential for smooth operation and extended seal life.
- Heat dissipation: The fluid in the gap helps to dissipate heat generated by friction between the seal faces. This prevents overheating and thermal distortions that could compromise sealing performance.
- Pressure distribution: The sealing gap allows for even distribution of pressure across the seal faces. This balanced pressure helps to maintain the optimal gap size and prevents fluid leakage.
- Contaminant exclusion: The narrow sealing gap, along with the fluid film, helps to prevent solid contaminants from entering the space between the seal faces. This reduces wear and extends seal life.
- Fluid containment: The sealing gap, in conjunction with the seal faces and secondary seals, contains the process fluid and prevents leakage to the environment.
Factors Influencing the Sealing Gap
Material
The materials used for the seal faces and other components directly affect the sealing gap. Different materials have varying thermal expansion rates, hardness, and wear resistance properties. Proper material selection ensures that the sealing gap remains consistent and within the desired range under operating conditions.
Pressure
The fluid pressure acting on the seal faces influences the sealing gap. Higher pressures tend to close the gap, while lower pressures allow for a wider gap. Seal designers must account for the expected pressure range to maintain an optimal sealing gap throughout operation.
Temperature
Temperature variations can cause thermal expansion or contraction of seal components, altering the sealing gap. High temperatures may cause materials to expand, reducing the gap, while low temperatures can lead to contraction and an increased gap. Thermal management and material selection are important considerations for maintaining a consistent sealing gap.
Speed of Rotation
The rotational speed of the shaft affects the hydrodynamic lubrication between the seal faces. Higher speeds generate more lift, which can increase the sealing gap. Designers must balance the speed of rotation with other factors to ensure proper lubrication and minimize wear.
Fluid Viscosity
The viscosity of the sealed fluid plays a significant role in the lubrication of the sealing gap. Higher viscosity fluids provide better lubrication and can help maintain a thicker fluid film between the seal faces. Lower viscosity fluids may require a narrower sealing gap to achieve adequate lubrication.
Design
The overall design of the mechanical seal, including the geometry of the seal faces, balance ratio, and spring loading, influences the sealing gap. Designers must carefully consider these parameters to create a seal that maintains an optimal gap under various operating conditions.
Challenges Related to the Sealing Gap
Maintaining an optimal sealing gap is critical for the reliable operation of a mechanical seal. However, several challenges can arise that may compromise the sealing gap and lead to seal failure.
Lubrication Failures
Inadequate lubrication of the sealing gap can result in increased friction, heat generation, and wear of the seal faces. This can occur due to insufficient fluid film thickness, poor fluid viscosity, or contamination. Lubrication failures can cause the sealing gap to collapse, leading to leakage and seal damage.
Contamination
Contamination of the sealed fluid with particles, debris, or chemical impurities can adversely affect the sealing gap. Contaminants can cause abrasive wear, clogging, or damage to the seal faces, disrupting the precise sealing gap.
Thermal Distortions
Uneven thermal expansion or contraction of seal components can distort the sealing gap. Thermal distortions may occur due to temperature gradients, transient conditions, or improper heat dissipation. These distortions can cause the sealing gap to deviate from its optimal range, leading to increased leakage or face contact.
Operator Errors
Improper installation, handling, or operation of the mechanical seal can compromise the sealing gap. Operator errors, such as incorrect assembly, over-tightening, or exposure to unintended conditions, can damage the seal faces or alter the sealing gap.