Shaft tolerance is a critical factor in the proper functioning and longevity of mechanical seals. Ensuring the correct shaft tolerance involves considering various aspects such as typical values, standards, surface finish, materials, alignment, and types of fits.
This article will delve into the key concepts related to shaft tolerance for mechanical seals. It will explore industry standards, factors affecting tolerance, and the differences between clearance and interference fits, providing a comprehensive guide for professionals working with these components.
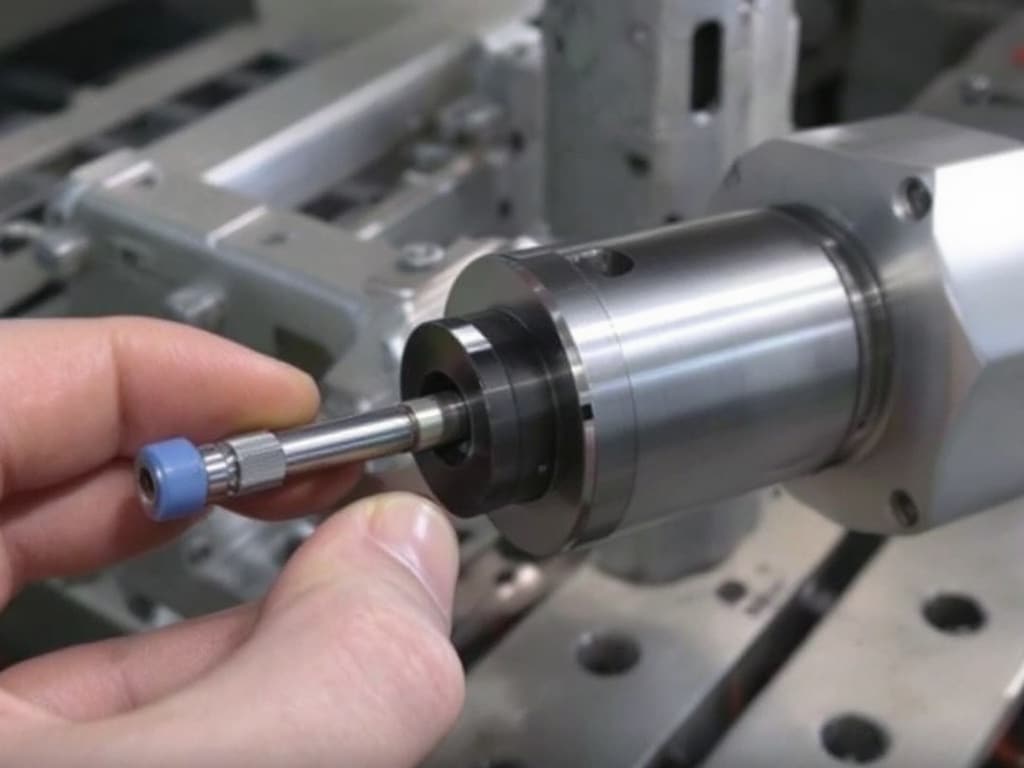
What Is Shaft Tolerances
Shaft tolerances refer to the allowable variations in the dimensions of a shaft, particularly its diameter. These dimensional tolerances are essential for ensuring proper fit, function, and performance of mechanical seals and other components that interact with the shaft.
Tolerances are typically expressed as a range, such as +/- 0.001 inches or +/- 0.025 mm, indicating the acceptable deviation from the nominal or ideal shaft diameter. Tighter tolerances result in more precise fits between the shaft and mating components, while looser tolerances allow for greater variability.
Typical Values and Standards
Nominal Shaft Diameter (mm) | Tolerance (mm) |
---|---|
0 to 18 | +0.000 to -0.011 |
18 to 30 | +0.000 to -0.013 |
30 to 50 | +0.000 to -0.016 |
50 to 80 | +0.000 to -0.019 |
80 to 120 | +0.000 to -0.022 |
120 to 180 | +0.000 to -0.025 |
Note: These values are for reference only and may vary depending on specific standards and applications.
What Is Surface Finish
Surface finish, also known as surface roughness, refers to the characteristics of the shaft’s surface texture. It is a measure of the microscopic irregularities, ridges, and valleys on the surface of the shaft.
Surface finish is quantified using various parameters, such as Ra (arithmetic average roughness), Rz (average maximum height of the profile), and Rmax (maximum individual roughness depth). These parameters are typically expressed in micrometers (μm) or microinches (μin).
The required surface finish for a shaft depends on the specific application and the type of mechanical seal being used. Generally, smoother surface finishes are desirable for applications involving mechanical seals, as they promote better sealing performance and reduce wear on the sealing components.
Common surface finish values for shafts used with mechanical seals range from 0.4 to 0.8 μm Ra (16 to 32 μin Ra). However, some applications may require even smoother finishes, such as 0.2 μm Ra (8 μin Ra) or better, to ensure optimal sealing performance and longevity.
Achieving the desired surface finish involves proper shaft manufacturing processes, such as turning, grinding, or polishing, and adherence to specified surface finish requirements during quality control inspections.
Factors Affecting Shaft Tolerance
Material
The material of the shaft directly impacts the achievable tolerance. Different materials have varying machinability, thermal expansion coefficients, and hardness properties. For instance, stainless steel shafts can be machined to tighter tolerances compared to plastic shafts due to their higher dimensional stability and lower thermal expansion.
The choice of material also affects the shaft’s resistance to wear, corrosion, and deformation under load. These factors must be considered when specifying shaft tolerances to ensure proper functionality and longevity of the mechanical seal.
Shaft Alignment and Run-Out
Misalignment or excessive run-out can cause uneven wear on the shaft and seal faces, leading to premature failure.
Shaft alignment refers to the concentricity between the shaft and the seal chamber. It ensures that the shaft is properly centered within the seal, minimizing radial loads on the seal faces. Proper alignment is typically achieved through precise machining and installation practices.
Run-out, on the other hand, refers to the deviation of the shaft from its true centerline during rotation. Excessive run-out can cause the seal faces to oscillate, resulting in increased wear and leakage. Run-out can be minimized by ensuring proper shaft straightness, balance, and supporting bearings.
Types of Fits
The fit between the shaft and the mechanical seal components is another critical factor in maintaining the desired shaft tolerance. The two primary types of fits are clearance fits and interference fits.
Clearance Fits
Clearance fits allow for a small gap between the shaft and the mating component, such as the seal sleeve or gland. This fit type accommodates minor shaft irregularities and thermal expansion without inducing excessive stress on the components.
Clearance fits are typically specified when easy assembly and disassembly are required or when the shaft and seal components are made from materials with different thermal expansion rates. However, excessive clearance can result in seal movement and leakage.
Interference Fits
Interference fits, also known as press fits, involve a slightly larger mating component than the shaft diameter. This creates a tight, friction-based connection between the shaft and the component.
Interference fits are used when a rigid, non-moving connection is required between the shaft and seal components. This type of fit minimizes relative motion and ensures concentricity between the parts.
However, interference fits can induce high stresses in the components and may require special installation and removal procedures. The amount of interference must be carefully calculated based on the materials, temperatures, and operating conditions to prevent damage to the shaft or seal components.