Thermosyphon systems are widely used in the machinery industry to support the proper functioning of mechanical seals. These systems leverage natural convection to circulate a sealing fluid, typically oil, between a seal chamber and a reservoir.
In this post, we will dive into the specifics of how thermosyphon systems work and the key functions they serve, including cooling, lubrication, pressure regulation and leak prevention. We’ll also explore the advantages and disadvantages of using thermosyphon systems and some common applications across various industries.
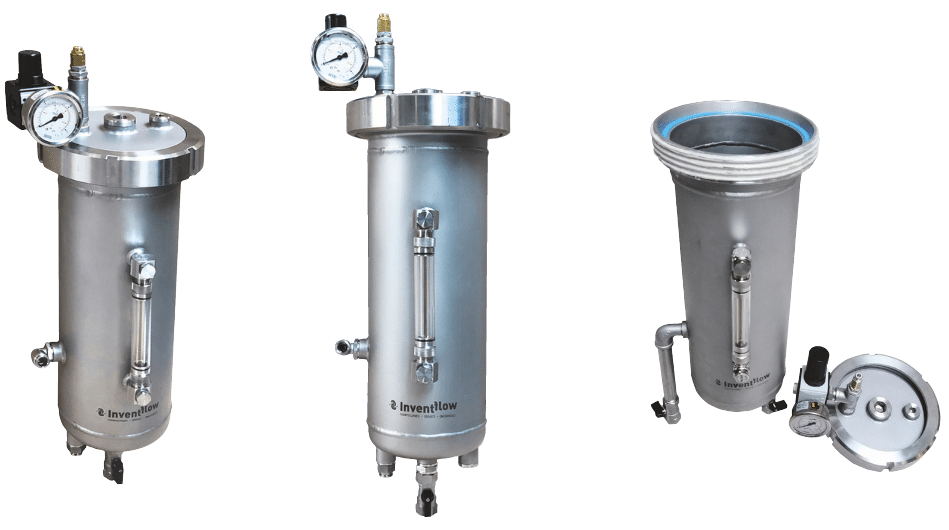
What Is Thermosyphon System for Mechanical Seal
A thermosyphon system is a cooling and lubrication system designed specifically for mechanical seals. It utilizes the natural convection circulation of a fluid, typically oil, to transfer heat away from the mechanical seal and maintain optimal operating conditions.
The system consists of a reservoir or tank that holds the cooling fluid, a heat exchanger, and piping that connects the mechanical seal to the reservoir. The fluid circulates through the system without the need for a pump, relying on the principles of thermal expansion and density differences.
In a thermosyphon system, the hot fluid from the mechanical seal rises due to its lower density, while the cooler fluid from the reservoir sinks, creating a continuous circulation loop. This circulation helps to dissipate heat generated by the mechanical seal, preventing overheating and potential seal failure.
Functions of Thermosyphon System
The thermosyphon system performs several critical functions to ensure the proper operation of mechanical seals:
Cooling
The primary function of the thermosyphon system is to remove excess heat generated by the mechanical seal during operation. As the fluid circulates through the heat exchanger, it dissipates heat, maintaining a stable temperature within the seal chamber. This cooling effect prevents thermal damage to the seal faces and other components.
Lubrication
The circulating fluid in the thermosyphon system also acts as a lubricant for the mechanical seal faces. Proper lubrication reduces friction and wear between the rotating and stationary faces, minimizing the risk of seal failure due to excessive heat generation or material degradation.
Pressure Regulation
The thermosyphon system helps maintain a consistent pressure within the seal chamber. As the fluid expands and contracts due to temperature changes, the system allows for pressure equalization, preventing excessive pressure buildup that could damage the seal or cause leakage.
Leak Prevention
By maintaining optimal temperature, lubrication, and pressure conditions, the thermosyphon system helps prevent leaks from the mechanical seal. Leaks can occur due to seal face damage, improper installation, or adverse operating conditions. The thermosyphon system mitigates these risks by ensuring the seal operates within its designed parameters.
How Thermosyphon System Works
The thermosyphon system relies on the principle of natural convection to circulate the fluid between the seal chamber and the heat exchanger. The system consists of a seal pot, which is connected to the seal chamber, and a finned tube heat exchanger located above the seal pot.
As the mechanical seal generates heat during operation, the fluid in the seal chamber absorbs this heat and expands. The heated fluid rises through the piping connecting the seal chamber to the seal pot due to its lower density. Once in the seal pot, the fluid continues to rise through the piping leading to the heat exchanger.
As the fluid passes through the heat exchanger, it releases heat to the surrounding environment, cooling down in the process. The cooled fluid, now denser, flows back down through the piping and into the seal chamber, where it absorbs heat from the mechanical seal once again. This continuous cycle of fluid circulation maintains stable temperature and lubrication conditions for the mechanical seal.
Advantages of Thermosyphon System
Simple and Reliable
Thermosyphon systems for mechanical seals are simple in design and construction, making them highly reliable. They do not require any moving parts or external power sources, reducing the likelihood of failure and minimizing maintenance requirements.
Efficient Cooling
Thermosyphon systems efficiently remove heat from the mechanical seal, ensuring optimal performance and extended seal life. The natural convection process effectively transfers heat from the seal to the cooling fluid, maintaining stable operating temperatures.
Cost-effective
Compared to other cooling and lubrication methods, thermosyphon systems are cost-effective. They do not require expensive components or complex control systems, making them an economical choice for many applications.
Environmentally Friendly
Thermosyphon systems typically use non-hazardous, environmentally friendly fluids, such as water or glycol solutions. This reduces the risk of environmental contamination and complies with increasingly stringent regulations.
Disadvantages of Thermosyphon System
Limited Heat Dissipation Capacity
Thermosyphon systems rely on natural convection for heat transfer, which may limit their heat dissipation capacity. In applications with high heat generation rates, the system may not be able to maintain adequate cooling, potentially leading to seal failure.
Sensitivity to Installation
The performance of a thermosyphon system depends on proper installation. Incorrect piping layout, insufficient insulation, or improper component sizing can negatively impact the system’s effectiveness, leading to reduced cooling efficiency and potential seal damage.
Not Suitable for All Applications
Thermosyphon systems may not be suitable for all applications, particularly those involving high-pressure differentials or extreme temperature ranges. In such cases, alternative cooling and lubrication methods may be required to ensure reliable mechanical seal performance.
Applications of Thermosyphon System
Pumps
Thermosyphon systems are commonly used in pumps to cool and lubricate mechanical seals. They are particularly effective in centrifugal pumps handling liquids at moderate temperatures and pressures, such as water, oils, and chemical solutions.
Compressors
In compressor applications, thermosyphon systems help maintain proper lubrication and cooling of mechanical seals. They are often employed in rotary screw compressors, reciprocating compressors, and centrifugal compressors handling gases at moderate pressures and temperatures.
Mixers and Agitators
Thermosyphon systems are used in mixers and agitators to ensure reliable mechanical seal performance. They provide effective cooling and lubrication, preventing seal failure and extending equipment life in applications involving the mixing and blending of various materials.
Reactors and Pressure Vessels
In reactors and pressure vessels, thermosyphon systems help maintain the integrity of mechanical seals by providing adequate cooling and lubrication. They are particularly useful in applications involving chemical reactions, high-temperature processes, and pressure-sensitive operations.