Pump packing is a critical component of industrial machinery, but it doesn’t last forever. As it deteriorates, it can lead to costly leaks, equipment damage, and unexpected downtime.
Ignoring the signs of failing pump packing can result in severe consequences, including increased maintenance costs, reduced productivity, and potential safety hazards.
By recognizing the key indicators that it’s time to replace your pump packing, such as increased leakage, visible wear, and unusual noises, you can proactively maintain your equipment and avoid costly disruptions to your operations.
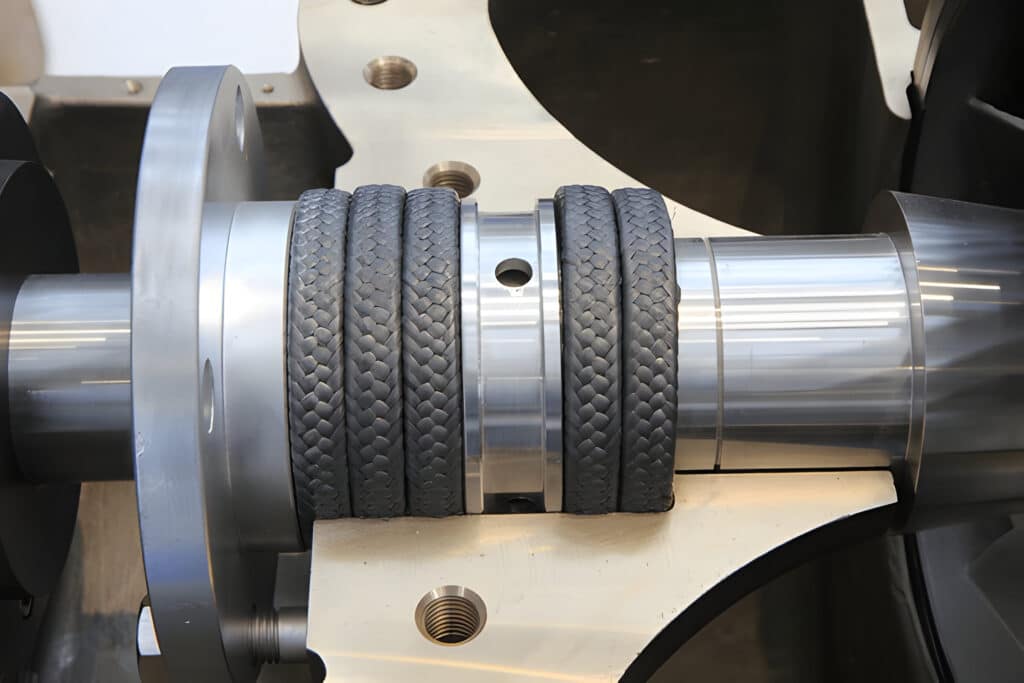
Increased Leakage
One of the clearest signs that it’s time to replace pump packing is increased leakage around the pump shaft. While some leakage is normal and necessary for lubrication and cooling, excessive leaking indicates that the packing has deteriorated and is no longer providing an effective seal.
Visible Wear or Damage
Look for signs of wear, such as fraying, shredding, or uneven compression. Damaged packing may have cracks, breaks, or missing sections. These issues can arise from normal wear and tear, improper installation, or exposure to harsh conditions.
Changes in Temperature
Unusual temperature changes around the pump packing area can indicate a problem. If the packing is too hot, it may be due to insufficient lubrication, excessive friction, or improper installation. Conversely, if the packing is too cold, it could be a sign of inadequate sealing or fluid leakage.
Unusual Noises
Pay attention to any unusual noises coming from the pump, particularly around the packing area. Squealing, grinding, or chattering sounds can indicate that the packing is worn, damaged, or improperly installed. These noises may be accompanied by increased vibration or pulsation.
Loss of Lubrication
If the packing loses lubrication, it can lead to increased friction, heat generation, and accelerated wear. This can happen due to insufficient lubrication during installation, changes in process conditions, or contamination of the lubricant.
Increased Fluid Loss Over Time
While some fluid loss is expected due to normal leakage, a gradual increase in fluid loss over time can indicate deteriorating packing. This can be caused by wear, damage, or changes in process conditions that affect the packing’s ability to seal effectively.
Presence of Solids
The presence of solids in the pumped fluid can accelerate packing wear and necessitate more frequent replacement. Abrasive particles, such as sand, silt, or crystalized products, can cause physical damage to the packing material, leading to increased leakage and reduced sealing efficiency.
Damage from Improper Installation
Improper installation of pump packing can lead to premature failure and the need for early replacement. Common installation issues include over-tightening the gland, using the wrong size or type of packing, or failing to stagger the packing rings correctly.
Excessive Gland Tightening
Over-tightening the packing gland is a common mistake that can lead to accelerated packing wear and damage. When the gland is too tight, it compresses the packing excessively, reducing its ability to lubricate and cool the shaft. This can cause increased friction, heat generation, and premature failure.
Misalignment
Misalignment between the pump shaft and the stuffing box can cause uneven wear on the packing, leading to leakage and premature failure. This can be caused by improper installation, foundation settling, or damage to the pump components.