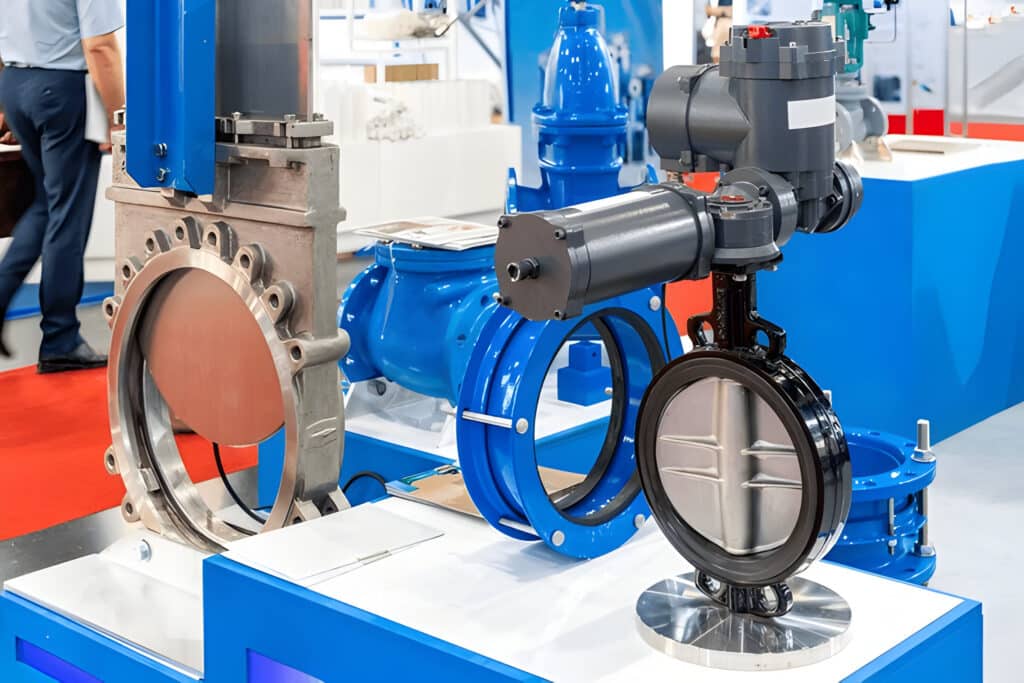
Butterfly valves are essential components in various industrial applications, offering reliable flow control and tight sealing. This article explores the differences between zero offset (concentric), double offset, and triple offset butterfly valves, helping you make an informed decision for your specific needs.
What is Zero Offset (Concentric) Butterfly Valves
Zero offset, or concentric butterfly valves, feature a simple design where the valve disc is centered on the shaft. The disc rotates around an axis that is concentric with the valve body’s centerline. This design is cost-effective and suitable for low-pressure and low-temperature applications.
Concentric butterfly valves have a soft seat, typically made of an elastomeric material, which provides a tight seal when the disc is in the closed position. However, due to the constant contact between the disc and the seat, these valves may experience increased friction and wear during operation, especially in abrasive or high-temperature environments.
Typical applications of Zero Offset (Concentric) Butterfly Valves
- Water treatment and distribution systems
- Heating, ventilation, and air conditioning (HVAC) systems
- Low-pressure gas and liquid pipelines
- Irrigation systems
- Swimming pool and spa equipment
Advantages of Zero Offset (Concentric) Butterfly Valves
- Simple and compact design
- Lightweight and easy to install
- Cost-effective solution for low-pressure applications
- Wide range of materials available for various media
- Suitable for large diameter pipelines
Limitations of Zero Offset (Concentric) Butterfly Valves
- Limited pressure and temperature capabilities
- Higher torque requirements due to disc-to-seat friction
- Potential for seat damage and leakage over time
- Not suitable for high-performance or critical applications
- Reduced throttling capabilities compared to offset designs
What is Double Offset Butterfly Valves
Double offset butterfly valves feature an offset shaft and an eccentric disc design. The valve disc is offset from the center of the valve body, and the seating surface is angled, creating a cam-like action during operation. This design reduces friction between the disc and the seat, resulting in longer service life and improved sealing performance.
The double offset design allows for the use of metal seats, which are more resilient than soft seats in high-temperature and abrasive applications. The eccentric disc design also reduces the torque required to operate the valve, making it easier to control and automate.
Typical applications of Double Offset Butterfly Valves
- Medium-pressure and medium-temperature applications
- Oil and gas processing plants
- Chemical and petrochemical industries
- Power generation plants
- Pulp and paper mills
Advantages of Double Offset Butterfly Valves
- Improved sealing performance compared to concentric designs
- Reduced friction and wear on the valve seat
- Lower torque requirements for actuation
- Suitable for medium-pressure and medium-temperature applications
- Extended valve life and reduced maintenance
Limitations of Double Offset Butterfly Valves
- Higher initial cost compared to concentric butterfly valves
- Not suitable for extremely high-pressure or high-temperature applications
- May require more complex actuation systems
- Limited throttling capabilities compared to triple offset designs
- Potential for leakage in demanding applications
What is Triple Offset Butterfly Valves
Triple offset butterfly valves represent the pinnacle of valve technology, offering superior performance and sealing capabilities in critical applications. This design incorporates three separate offsets: the shaft offset, the disc seat offset, and the seat cone angle.
The first offset moves the shaft away from the center of the valve body, while the second offset creates an eccentric disc that moves away from the seat as the valve opens. The third offset involves a conical seating surface, which ensures uniform sealing and reduces friction during operation.
Triple offset valves provide a bubble-tight seal, even in high-pressure and high-temperature applications. The metal-to-metal seating surfaces are highly durable and resistant to wear, making them ideal for use with abrasive or corrosive media. The triple offset design also allows for a complete 360-degree rotation, enabling precise control and a wide range of flow rates.
Typical applications of Triple Offset Butterfly Valves
- High-pressure and high-temperature applications
- Severe service conditions in oil and gas, chemical, and power generation industries
- Offshore platforms and subsea systems
- Cryogenic and high-temperature gas processing
- Corrosive and abrasive media applications
Advantages of Triple Offset Butterfly Valves
- Excellent sealing performance with bubble-tight shut-off
- Minimal friction and wear on the valve seat
- Low torque requirements for actuation
- Suitable for a wide range of pressures and temperatures
- Extended valve life and reduced maintenance costs
- Precise throttling capabilities
Limitations of Triple Offset Butterfly Valves
- Higher initial investment compared to other butterfly valve types
- Complex design and manufacturing process
- May require specialized actuation systems
- Not cost-effective for low-pressure or general-purpose applications
- Requires precise installation and alignment for optimal performance
Offset Type Comparison (Zero Offset vs. Double Offset vs. Triple Offset Butterfly Valve)
Feature | Zero Offset | Double Offset | Triple Offset |
---|---|---|---|
Sealing ability and leakage rates | Moderate | Good | Excellent |
Pressure and temperature capabilities | Low | Medium | High |
Throttling and flow control | Limited | Moderate | Precise |
Seat friction and wear | High | Moderate | Low |
Torque requirements and actuation | High | Moderate | Low |
Maintenance and service life | Moderate | Good | Excellent |
Cost | Low | Moderate | High |
Conclusion
Selecting the appropriate butterfly valve type depends on your specific application, considering factors such as pressure, temperature, media, and performance requirements.
Zero offset butterfly valves offer a cost-effective solution for low-demand applications, while double offset valves provide improved performance for medium-range needs. For critical and demanding applications, triple offset butterfly valves deliver unmatched sealing performance and reliability.
By understanding the differences between these valve types, you can make an informed decision to optimize your system’s efficiency and longevity.