What is API Plan 32
API Plan 32 is a type of mechanical seal support system that is used to help keep seals working properly in certain kinds of pumps and other rotating equipment. This system is designed to make sure that the seal always has clean liquid around it to keep it cool and lubricated.
How Does API Plan 32 Work
In API Plan 32, a clean, cool liquid (usually water) is injected into the seal chamber from an external source. This liquid is called the flush fluid. The flush fluid enters the seal chamber through a special port or connection.
Once inside the seal chamber, the flush fluid mixes with the process fluid that the pump is handling. The flush fluid helps to cool down the mechanical seal and prevents the process fluid from getting too hot.
By constantly injecting clean flush fluid, API Plan 32 helps keep the seal faces clean and free of debris.
The mixture of flush fluid and process fluid then exits the seal chamber through another port. This port is connected to a drain or collection system. The used flush fluid is safely removed and disposed of, while the process fluid continues on its way through the pump.
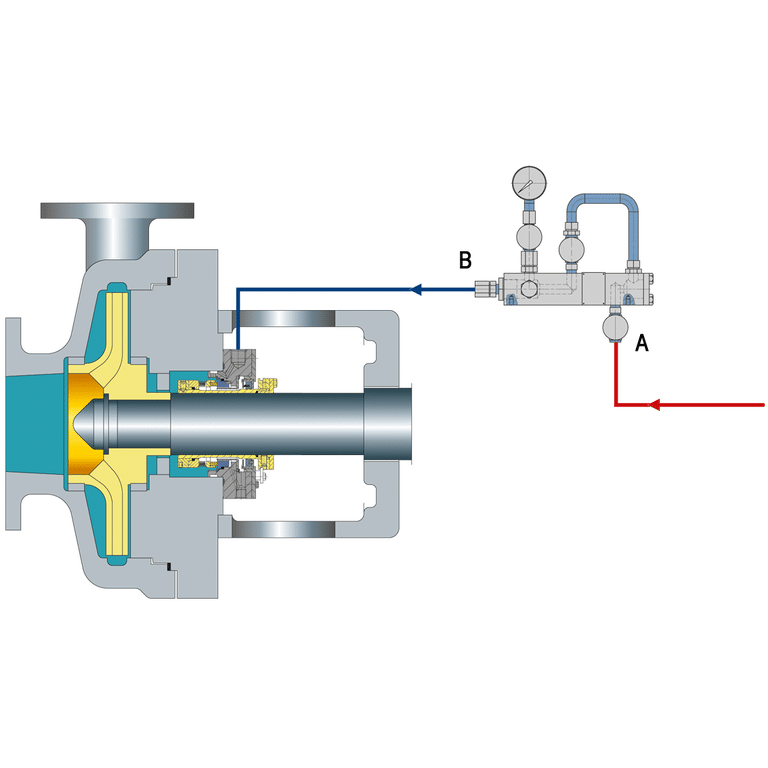
Design of API Plan 32
- External fluid reservoir: A separate tank or vessel is used to store the flush fluid, which is typically a clean, compatible liquid with good lubricating and cooling properties.
- Fluid circulation system: A small pump, often called a seal support pump, is used to circulate the flush fluid from the reservoir to the seal chamber and back to the reservoir. The circulation system maintains a constant flow of clean, cool fluid to the seal faces.
- Heat exchanger (optional): In some cases, a heat exchanger may be included to cool the flush fluid before it enters the seal chamber, especially if the process fluid is hot or if the seal generates significant heat due to friction.
- Pressure control: A pressure regulator is used to maintain the flush fluid pressure slightly higher than the pressure in the seal chamber. This ensures that the clean flush fluid flows into the seal chamber and prevents the process fluid from entering and contaminating the seal faces.
- Filtration: A filter is often included in the circulation system to remove any contaminants from the flush fluid, maintaining a clean environment for the seal faces.
- Instrumentation: Pressure gauges, flow meters, and temperature sensors may be included to monitor the performance of the API Plan 32 system and ensure that it is operating within the desired parameters.
Advantages of API Plan 32
- Effective cooling: API Plan 32 directs clean flush fluid through a heat exchanger, maintaining optimal seal temperature and preventing premature failure due to heat.
- Increased seal reliability: This plan ensures stable temperatures and clean fluid, reducing unplanned shutdowns and maintenance, and enhancing equipment availability.
- Compatibility with various fluids: API Plan 32 suits a wide range of process fluids, with adaptable heat exchangers for different properties like viscosity and corrosiveness.
Disadvantages of API Plan 32
- Higher initial costs: Additional equipment like a heat exchanger raises installation expenses, though long-term benefits include better seal performance.
- Increased complexity: Adding a heat exchanger and piping complicates both installation and maintenance, possibly necessitating extra training for personnel.
- Potential for fouling: If the process fluid contains particles, the heat exchanger might foul, decreasing heat transfer efficiency and requiring regular cleaning.
Applications
- Refineries and petrochemical plants: API Plan 32 ensures proper seal temperature, preventing failure in pumps handling hydrocarbons.
- Chemical processing: API Plan 32 maintains seal temperature for pumps handling reactive fluids, minimizing premature failure.
- Power generation: API Plan 32 in power plants ensures optimal seal temperature, minimizing downtime.
- Pulp and paper mills: API Plan 32 extends seal life in pumps handling abrasive fluids.