Cost analysis of mechanical seals involves evaluating various factors throughout their lifecycle. These include initial purchase and installation costs, ongoing operational expenses, maintenance and repair costs, and potential production losses due to failures. The analysis also considers environmental and safety aspects, as well as decommissioning and disposal costs.
By comparing different sealing solutions, such as mechanical seals versus compression packing or single versus dual mechanical seals, businesses can make informed decisions to optimize their operations and reduce overall expenses.
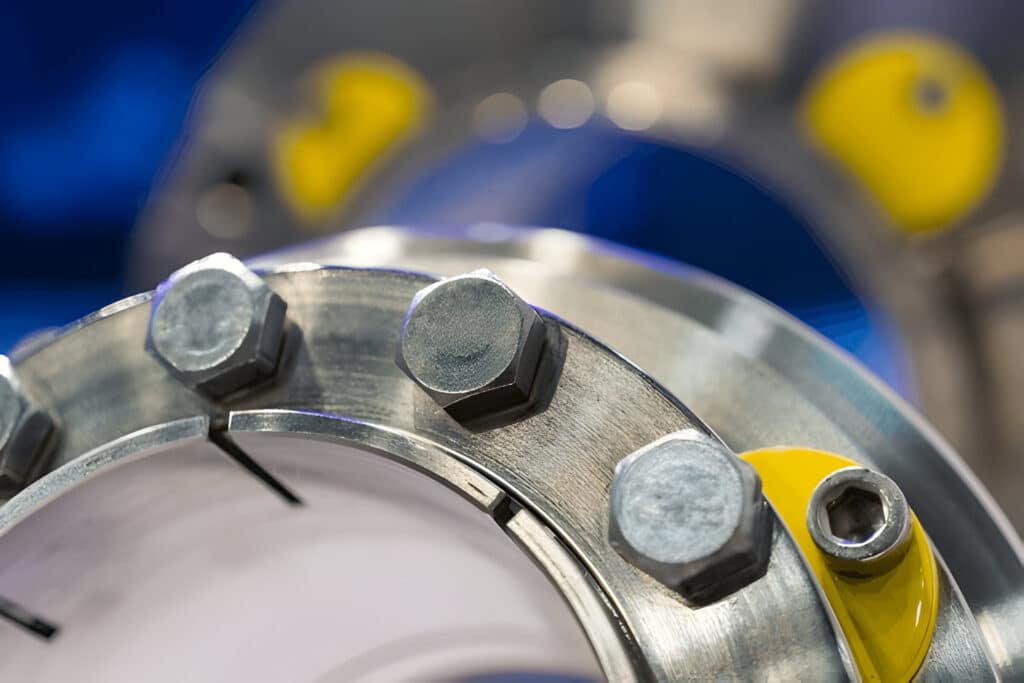
Components of Mechanical Seal Lifecycle Costs
Initial Purchase and Installation Costs
The initial purchase and installation costs can vary widely depending on several factors:
- Seal type and complexity: Single mechanical seals are generally less expensive than dual seals, while cartridge seals often command a premium due to their pre-assembled nature.
- Size and materials: Larger seals and those made from specialized materials (e.g., silicon carbide or tungsten carbide) typically cost more than smaller, standard material seals.
- Application requirements: Seals designed for high-pressure, high-temperature, or corrosive environments often come with higher price tags due to their advanced engineering and materials.
Installation costs can also contribute significantly to the initial investment. Factors affecting installation expenses include:
- Labor costs: Skilled technicians are required for proper seal installation, with rates varying by region and expertise level.
- Auxiliary systems: Some mechanical seals require support systems like flush plans or barrier fluid systems, adding to the overall installation cost.
It’s important to note that while initial costs may seem high, they often represent only 10-20% of the total lifecycle cost of a mechanical seal.
Operating Costs
Most mechanical seals require a constant flow of cool water to maintain optimal performance and prevent overheating. The volume of water needed can range from 1 to 5 gallons per minute.
Flush fluids typically consisting of clean product or a compatible buffer fluid, help lubricate seal faces and remove heat. The cost of flush fluids varies widely based on the type and quality required. For example, high-purity fluids used in pharmaceutical applications can cost up to 10 times more than standard industrial fluids.
Energy consumption is another significant factor in mechanical seal operating costs. The friction between seal faces generates heat, which requires additional energy to dissipate. Studies have shown that mechanical seals can account for up to 25% of a pump’s total power consumption. This energy loss translates directly into increased electricity costs for the facility.
Equipment Maintenance and Repair
When equipment repairs are necessary, it’s essential to consider the impact on mechanical seals. Improper handling or reassembly can damage seals or create conditions that lead to premature failure.
Seal Maintenance and Repair
Repair costs vary depending on seal complexity and damage extent. Simple repairs, like replacing O-rings or gaskets, may cost 10-20% of the seal’s initial price. More extensive repairs, involving face replacement or shaft sleeve refurbishment, can reach 40-60% of the original seal cost.
Specialized tools and expertise are often required for seal maintenance and repair. Many organizations opt for outsourcing these services to OEMs or authorized service centers, which can increase costs but ensure quality work. In-house maintenance teams may require additional training and equipment investments.
Production Losses from Seal Failures
These losses stem from unplanned downtime, reduced equipment efficiency, and potential contamination of products or processes.
Investing in high-quality seals and proper installation can significantly reduce the frequency of failures. While premium seals may have higher upfront costs, they often provide a lower total cost of ownership when considering potential production losses from failures.
Environmental and Safety
Proper seal selection and maintenance can significantly reduce emissions, prevent leakage of hazardous materials, and improve overall plant safety.
Investing in high-quality mechanical seals may have higher upfront costs but can lead to significant long-term savings through reduced environmental liabilities, improved safety records, and lower operational risks.
Decommissioning and Disposal
Decommissioning costs vary depending on the seal’s materials and operating conditions. Seals exposed to hazardous chemicals may require specialized handling, increasing disposal expenses.
Some manufacturers offer take-back programs for used mechanical seals, which can reduce disposal costs for end-users. These programs typically involve returning the used seal to the manufacturer for proper disposal or recycling, potentially lowering disposal expenses by 10-20% compared to independent disposal methods.
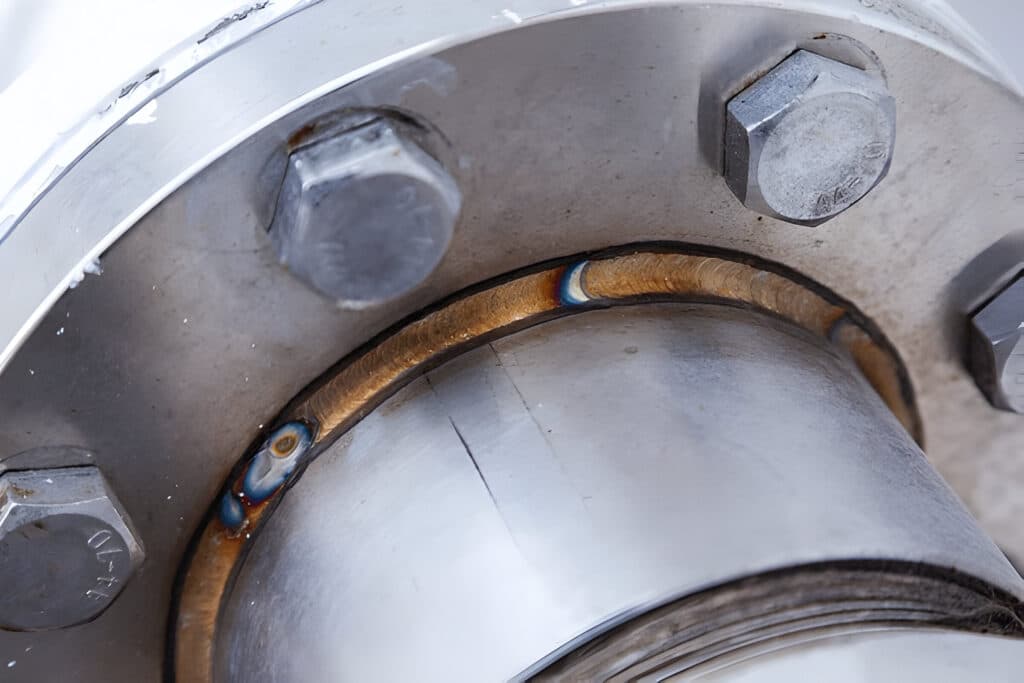
Costs of Different Sealing Solutions
Mechanical Seals Vs. Compression Packing
Initial investment for mechanical seals is significantly higher, often 5-10 times more expensive than compression packing. However, this upfront cost is offset by reduced operational expenses over time.
Compression packing requires frequent adjustments and replacements, leading to higher maintenance costs and increased downtime. On average, packing needs adjustment every 3-6 months and replacement every 12-18 months, whereas mechanical seals can operate for 3-5 years without intervention.
Energy consumption is another critical factor. Mechanical seals reduce friction, resulting in 2-3% lower power consumption compared to compression packing. This translates to substantial energy savings over the equipment’s lifetime.
Leakage rates differ significantly between the two options. Mechanical seals typically leak at rates of 0.1-0.5 gallons per hour, while compression packing can leak 1-5 gallons per hour. This difference impacts product loss, environmental compliance, and safety considerations.
Single Vs. Dual Mechanical Seals
Single mechanical seals are generally less expensive upfront. However, they may require more frequent maintenance and replacement, potentially increasing long-term expenses. Single seals typically consume less power, resulting in lower energy costs, but they offer less protection against leakage.
Dual mechanical seals, while more expensive initially ($1,500 to $5,000), often provide better reliability and longevity. They offer superior leak prevention, reducing potential environmental and safety risks.
Maintenance frequency differs significantly between the two types:
- Single seals typically require maintenance every 12-18 months
- Dual seals can often operate for 3-5 years before needing service
Cartridge Mechanical Seal
Cartridge mechanical seals offer significant cost advantages over component seals in various industrial applications. These pre-assembled units reduce installation time by up to 50%, minimizing labor costs and potential errors during assembly.
The initial purchase cost of cartridge seals is typically 15-25% higher than component seals. However, this investment is often offset by reduced maintenance expenses and improved reliability. Cartridge seals require less frequent adjustments, with mean time between maintenance (MTBM) rates 40% longer than component seals.
Maintenance and repair costs for cartridge seals are substantially lower than component seals. The modular design allows for quick replacement of the entire unit, reducing maintenance time by up to 60%. This efficiency can result in savings of $1000-$2000 per seal change-out in labor costs alone.