Gleitringdichtungen sind kritische Komponenten in Kreiselpumpen die ein Austreten der gepumpten Flüssigkeit verhindern. Ein Ausfall dieser Dichtungen kann zu verschiedenen Problemen führen, die die Leistung, Zuverlässigkeit und Lebensdauer der Pumpe beeinträchtigen. Dieser Artikel untersucht detailliert die verschiedenen Folgen, die durch den Ausfall von Gleitringdichtungen in Kreiselpumpen entstehen können.
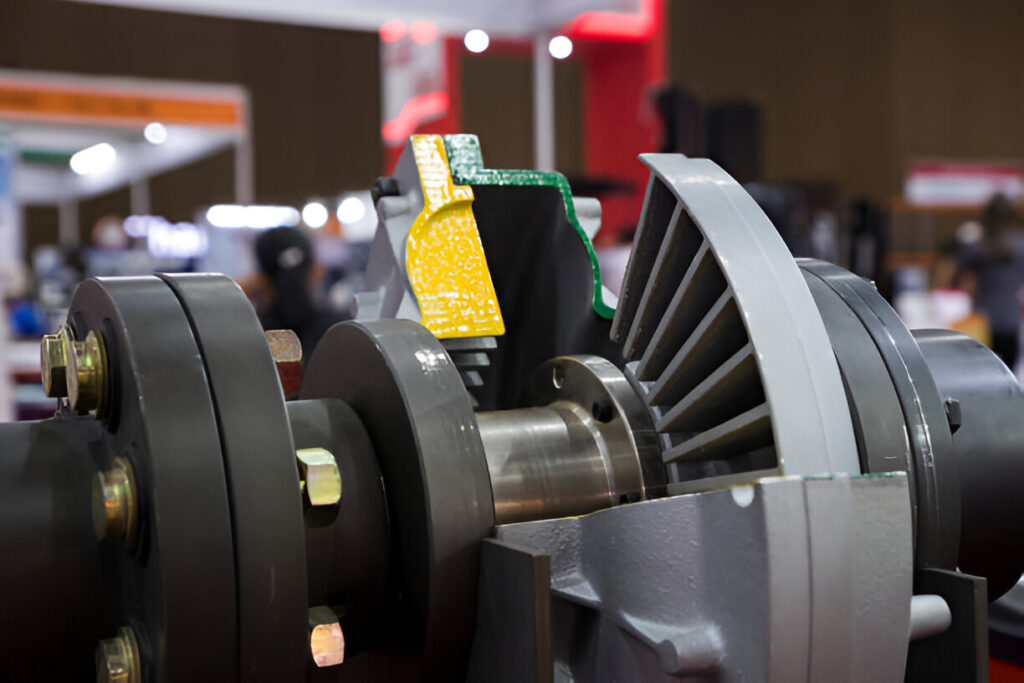
Leckage der gepumpten Flüssigkeit
Leckagen sind das häufigste Problem bei Gleitringdichtung Dies ist für über 40% aller Dichtungsfehler verantwortlich.
Die Hauptfunktion einer Gleitringdichtung besteht darin, ein Austreten der gepumpten Flüssigkeit aus dem Pumpengehäuse zu verhindern. Wenn eine Dichtung versagt, kann die gepumpte Flüssigkeit entweichen, was zu einer verringerten Pumpleistung und potenziellen Sicherheitsrisiken führt. Je nach Art der gepumpten Flüssigkeit kann ein Austreten auch Umweltschäden verursachen oder gegen Vorschriften verstoßen.
Laufraderosion
Austretende Flüssigkeit aus einer defekten Gleitringdichtung kann zur Erosion der Laufradschaufeln führen. Wenn die Flüssigkeit durch die beschädigte Dichtung austritt, enthält sie häufig abrasive Partikel, die das Laufradmaterial mit der Zeit abnutzen. Diese Erosion verringert die hydraulische Effizienz des Laufrads und führt zu einer verringerten Pumpenleistung.
Laufraderosion ist besonders problematisch beim Pumpen von Schlämmen oder Flüssigkeiten mit Schwebstoffen. Studien haben ergeben, dass selbst eine geringe Vergrößerung des Abstands zwischen Laufrad und Gehäuse aufgrund von Erosion die Pumpeneffizienz um 2-5% verringern kann. In schweren Fällen kann Laufraderosion zum vollständigen Ausfall des Laufrads führen, was einen kostspieligen Austausch erforderlich macht.
Hülsen-/Wellenverschleiß
Austretende Flüssigkeit aus einer defekten Dichtung kann nicht nur das Laufrad beeinträchtigen, sondern auch Verschleiß an der Pumpenwelle oder -hülse verursachen. Wenn die Flüssigkeit austritt, kann sie Schmutz und Verunreinigungen mit sich führen, die wie Schleifmittel wirken und die Oberfläche der Welle oder Hülse allmählich abnutzen. Dieser Verschleiß kann Rillen, Kratzer oder andere Unregelmäßigkeiten verursachen, die die Dichtungsoberflächen beschädigen.
Aushöhlung, Dellen, Kratzer am Schaft
Über die allmähliche Abnutzung hinaus Dichtungsfehler kann auch zu schwerwiegenderen Schäden an der Pumpenwelle führen, wie z. B. Aushöhlungen, Dellen oder tiefe Kratzer. Dies tritt typischerweise auf, wenn die Dichtflächen Die Dichtungen können verstellt oder beschädigt werden, sodass harte Partikel zwischen den Dichtungsflächen und der Welle eingeschlossen werden können.
Wenn sich die Welle dreht, können diese eingefangenen Partikel tiefe Kratzer oder Kerben in der Wellenoberfläche hinterlassen. Es können auch Dellen entstehen, wenn größere Fremdkörper mit ausreichender Kraft auf die Welle treffen. Diese Art von Schaden kann schnell zu einem Dichtungsversagen führen, da die Kratzer und Dellen Leckagewege für die gepumpte Flüssigkeit darstellen.
Korrosion der Dichtungswelle
Ein Ausfall der Gleitringdichtung kann dazu führen, dass die Pumpenwelle korrosiven Flüssigkeiten ausgesetzt wird, was zu beschleunigter Korrosion und Verschlechterung des Wellenmaterials führt. Viele gepumpte Flüssigkeiten enthalten Chemikalien, die mit der Metallurgie der Welle reagieren und sie im Laufe der Zeit schwächen können.
Korrosion ist besonders schädlich, da sie sich über den unmittelbaren Dichtungsbereich hinaus ausdehnen und einen größeren Teil der Welle beeinträchtigen kann. Dieser großflächige Schaden kann die Wellenreparatur erschweren und einen vollständigen Austausch erforderlich machen. Korrosion kann auch die Oberflächenrauheit der Welle erhöhen, wodurch die mechanische Dichtung selbst dann nicht mehr dicht abdichtet, wenn der sichtbare Schaden weggearbeitet wird.
Blitzen oder Ätzen
Bei Flüssigkeiten mit niedrigem Siedepunkt kann eine Leckage der Gleitringdichtung dazu führen, dass die Flüssigkeit schnell verdampft, da sie nach dem Austreten aus der Pumpe einen Druckabfall erfährt. Diese schnelle Verdampfung, auch als Verdampfen oder Ätzen bekannt, kann die Dichtungsflächen abnutzen und die Flüssigkeit erhitzen. Dichtungskomponenten, was zu vorzeitigem Versagen führt. Durch Gratbildung können auch örtlich hohe Temperaturen entstehen, die eine thermische Verformung der Dichtungsflächen verursachen, was zu weiteren Leckagen führt.
Reiben
Reibkorrosion tritt auf, wenn es zu einer Relativbewegung zwischen den Gleitringdichtungskomponenten kommt. Dies ist häufig auf unsachgemäße Installation, mangelhafte Schmierung oder Verformung der Dichtungsflächen zurückzuführen. Diese Relativbewegung verursacht Gleiten und Reibung mit geringer Amplitude zwischen den Oberflächen, was zu Verschleiß und Ermüdung führt.
Durch Reibkorrosion können geschwächte Bereiche in den Dichtungsflächen entstehen, die anfällig für Risse und Brüche sind. Außerdem können kleine Partikel entstehen, die die Dichtungsflächen verunreinigen und so Abrieb und Leckagen erhöhen.
Übermäßige Vibrationen und Lärm
Eine defekte Gleitringdichtung kann übermäßige Vibrationen und Lärm verursachen, was häufig auf schwerwiegendere zugrunde liegende Probleme hinweist. Wenn die Dichtungsflächen verschleißen oder beschädigt werden, können sie ihre glatte, flache Oberfläche verlieren, wodurch eine Unwucht entsteht, die die Welle zum Vibrieren bringt. Austretende Flüssigkeit kann auch Kavitation verursachen, bei der die schnelle Bildung und der Zusammenbruch von Dampfblasen Vibrationen und Lärm verursachen.
Pumpenabschaltung und Ausfallzeiten
Letztendlich kann ein Ausfall der Gleitringdichtung zu einem vollständigen Ausfall der Pumpe und ungeplanten Ausfallzeiten führen. Wenn eine Dichtung katastrophal versagt, kann dies zu Folgeschäden an anderen Pumpenkomponenten führen, die umfangreiche Reparaturen erforderlich machen. In einigen Fällen können die Kosten für die Reparatur einer schwer beschädigten Pumpe die Kosten für den Austausch übersteigen.