Mechanical seals are critical components in various industrial applications that prevent fluid leakage and ensure efficient equipment operation. To enhance the performance and longevity of mechanical seals, quench systems are often employed. A quench in a mechanical seal refers to a secondary fluid that is introduced to the seal faces to provide cooling, lubrication, and protection against adverse conditions.
This blog post will delve into the intricacies of quench systems in mechanical seals. We will explore the components that make up a quench system, the types of fluids commonly used, and the key functions these systems serve, such as cooling, preventing leakage, and protecting against crystallization. Additionally, we will discuss the diverse applications of quench systems across industries, the design considerations and monitoring practices, and the advantages and potential drawbacks associated with implementing quench systems in mechanical seals.
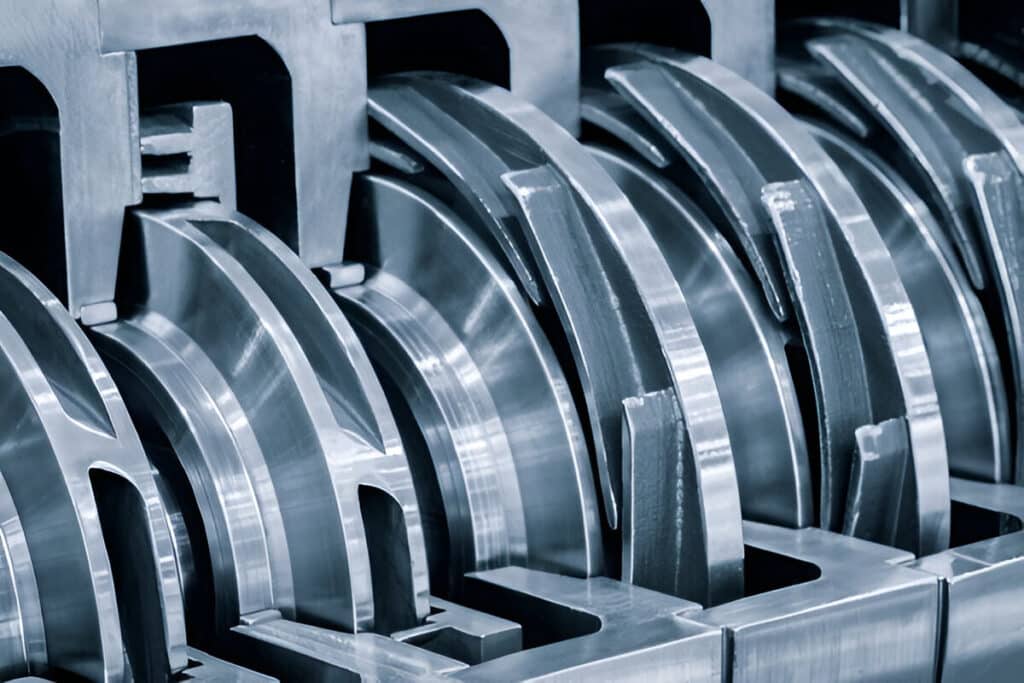
What Is a Quench in a Mechanical Seal
In the context of mechanical seals, a quench refers to a method of cooling and lubricating the seal faces to prevent leakage and extend seal life. Quenching involves introducing a fluid, typically a liquid or gas, into the seal chamber or onto the atmospheric side of the seal faces. This fluid serves to absorb heat generated by friction and dissipate it away from the seal components.
The quench fluid also helps to lubricate the seal faces, reducing wear and tear caused by the constant contact and relative motion between the rotating and stationary faces. By maintaining a thin film of fluid between the faces, the quench reduces direct contact and minimizes friction-related damage.
Components of a Quench System
A typical quench system comprises several key components that work together to achieve the desired objectives:
- Quench fluid reservoir: This is a container that holds the quench fluid, which can be a liquid or a gas, depending on the application requirements. The reservoir should have sufficient capacity to ensure an adequate supply of the quench fluid.
- Circulation pump or compressor: Depending on whether the quench fluid is a liquid or a gas, a pump or compressor is used to circulate the fluid through the system. This ensures a continuous flow of the quench fluid to the seal faces.
- Piping and valves: A network of pipes and valves is used to transport the quench fluid from the reservoir to the seal and back. The piping should be designed to minimize pressure drops and ensure uniform flow distribution.
- Flow control devices: These include components such as flow meters, pressure regulators, and throttling valves, which help maintain the desired flow rate and pressure of the quench fluid at the seal faces.
- Heat exchanger (optional): In some cases, a heat exchanger may be incorporated into the quench system to remove excess heat from the quench fluid, especially if the process fluid generates significant heat or if the quench fluid needs to be maintained at a specific temperature.
Types of Fluids Used
The selection of the quench fluid depends on various factors, such as the process fluid properties, operating conditions, and environmental considerations. Some common types of quench fluids include:
- Water: Water is a widely used quench fluid due to its excellent cooling and lubricating properties, as well as its abundance and low cost. However, it may not be suitable for applications involving water-reactive or water-soluble process fluids.
- Glycol-based solutions: Glycol-based fluids, such as ethylene glycol or propylene glycol, are often used as quench fluids because of their good heat transfer characteristics and low freezing points. They are particularly useful in applications where the process fluid may crystallize or solidify at lower temperatures.
- Oils: Various types of oils, including mineral oils, synthetic oils, and vegetable oils, can be used as quench fluids. They provide good lubrication and are suitable for applications involving high temperatures or chemically aggressive process fluids.
- Gases: In some cases, gases such as nitrogen, air, or steam can be used as quench fluids. Gaseous quench systems are typically used when the process fluid is sensitive to contamination or when a non-reactive environment is required.
Functions of Quench Systems
Cooling and Lubrication of the Seal
One of the primary functions of a quench system in a mechanical seal is to provide cooling and lubrication to the seal faces. The constant flow of the quench fluid helps dissipate heat generated by the friction between the rotating and stationary faces of the seal.
Additionally, the quench fluid acts as a lubricant between the seal faces, reducing friction and wear. By maintaining a thin film of fluid between the faces, the quench system minimizes direct contact and helps extend the seal’s service life.
Prevention of Leakage to the Atmosphere and Contamination
Another key function of quench systems is to prevent leakage of the sealed fluid to the atmosphere and to protect the sealed fluid from external contamination.
By maintaining a higher pressure in the quench chamber compared to the atmospheric pressure, the quench system ensures that any leakage that may occur is directed back into the quench fluid rather than escaping to the atmosphere. This positive pressure differential also prevents the ingress of atmospheric contaminants, such as moisture or dust, into the sealed fluid, maintaining its purity and integrity.
Protection Against Crystallization and Reaction with Atmospheric Conditions
In certain applications, the sealed fluid may be prone to crystallization or adverse reactions when exposed to atmospheric conditions. For example, some fluids may solidify, precipitate, or form deposits when they come into contact with air or moisture. These phenomena can lead to the build-up of solids on the seal faces, causing increased friction, wear, and eventually seal failure.
The quench system mitigates these issues by isolating the sealed fluid from the atmosphere and maintaining a controlled environment within the quench chamber. The quench fluid is carefully selected to be compatible with the sealed fluid and to prevent any unwanted reactions. By keeping the sealed fluid submerged in the quench fluid, the system prevents direct exposure to atmospheric conditions, minimizing the risk of crystallization or other detrimental reactions.
Applications of Quench Systems
High-Temperature Applications
Quench systems are commonly employed in high-temperature applications where the sealed fluid is at an elevated temperature. In these cases, the quench fluid serves as a cooling medium, absorbing and dissipating the heat generated by the sealing process. By maintaining a lower temperature at the seal faces, the quench system prevents thermal damage to the seal components and ensures reliable operation in demanding high-temperature environments.
Hazardous and Toxic Fluid Sealing
In industries such as chemical processing, petroleum refining, and pharmaceuticals, mechanical seals are often used to contain hazardous or toxic fluids. Quench systems play a vital role in these applications by providing an additional layer of protection against leakage. The quench fluid acts as a barrier, preventing the escape of dangerous substances into the atmosphere and minimizing the risk of environmental contamination or personnel exposure.
Crystallizing and Solidifying Fluids
Some process fluids have a tendency to crystallize or solidify when exposed to certain conditions, such as changes in temperature or pressure. These fluids can pose challenges for mechanical seals, as the formation of solids on the seal faces can lead to increased friction, wear, and premature failure. Quench systems are employed in these applications to maintain a stable environment around the seal, preventing crystallization and ensuring smooth operation.
Advantages of Quench Systems
Extended Seal Life
One of the primary advantages of quench systems is their ability to extend the service life of mechanical seals. By providing effective cooling, lubrication, and protection against adverse conditions, quench systems reduce wear and tear on the seal faces. The consistent flow of the quench fluid helps maintain a stable sealing environment, minimizing thermal and mechanical stresses on the seal components.
Enhanced Process Safety
Quench systems contribute significantly to enhancing process safety by mitigating the risks associated with leakage and contamination. By preventing the escape of hazardous or toxic fluids to the atmosphere, quench systems help protect personnel, equipment, and the environment from potential harm.
Improved Process Reliability
The use of quench systems can greatly improve the reliability of mechanical seals and the processes they serve. By maintaining optimal sealing conditions and preventing premature seal failures, quench systems minimize unplanned downtime and production interruptions.
Disadvantages of Quench Systems
Increased Complexity and Cost
Implementing a quench system adds complexity to the sealing arrangement, requiring additional components, piping, and instrumentation. This increased complexity can translate into higher initial costs for equipment, installation, and commissioning. The need for regular monitoring, maintenance, and potential repairs of the quench system also contributes to increased operational expenses over the life of the equipment.
Potential for Quench Fluid Contamination
While quench systems are designed to prevent contamination of the sealed fluid, there is a potential risk of the quench fluid itself becoming contaminated. Ingress of process fluid, atmospheric contaminants, or degradation of the quench fluid over time can compromise its effectiveness and lead to adverse effects on the sealing performance.
Additional Maintenance Requirements
The presence of a quench system introduces additional maintenance requirements compared to simpler sealing arrangements. The quench fluid needs to be periodically checked for contamination, degradation, and compatibility with the sealed fluid and seal materials. The piping, pumps, and instrumentation associated with the quench system also require regular inspection, cleaning, and calibration to ensure optimal performance.