Mechanical seals are critical components in centrifugal pumps that prevent leakage of the pumped fluid. When these seals fail, it can lead to a range of problems that impact the performance, reliability and longevity of the pump. This article will examine in detail the various consequences that can occur due to the failure of mechanical seals in centrifugal pumps.
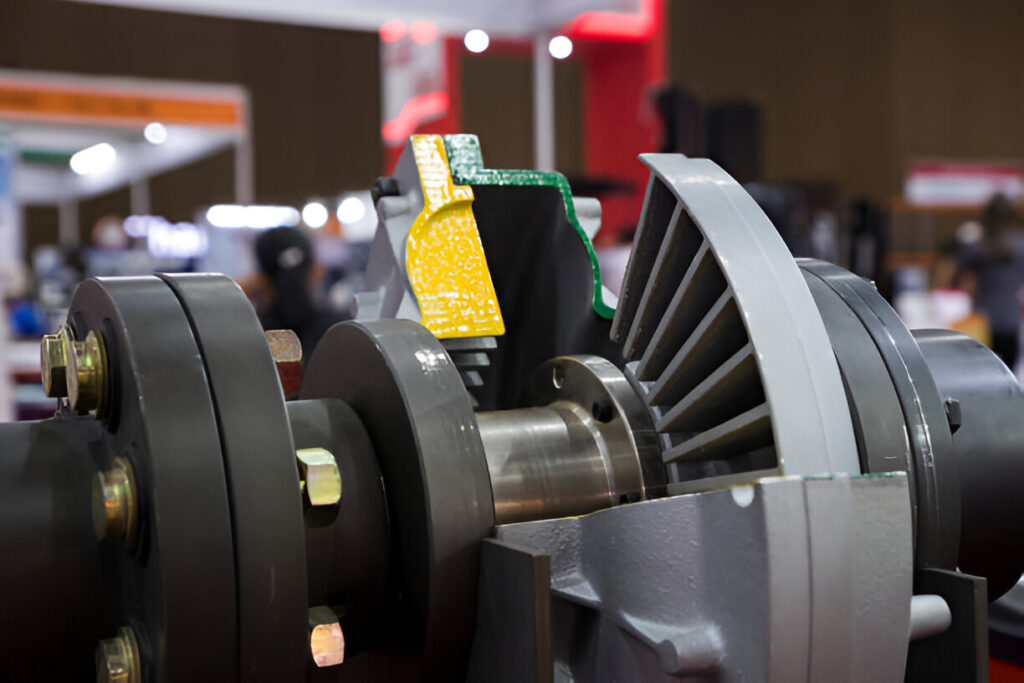
Leakage of Pumped Fluid
Leakage is the most common problem associated with mechanical seal failure, accounting for over 40% of all seal failures.
The primary function of a mechanical seal is to prevent leakage of the pumped fluid from the pump casing. When a seal fails, it allows the pumped fluid to escape, leading to reduced pumping efficiency and potential safety hazards. Depending on the nature of the fluid being pumped, leakage can also cause environmental damage or violate regulations.
Impeller Erosion
Leaking fluid from a failed mechanical seal can cause erosion of the impeller vanes. As the fluid escapes through the damaged seal, it often contains abrasive particles that wear away the impeller material over time. This erosion reduces the hydraulic efficiency of the impeller, leading to decreased pump performance.
Impeller erosion is particularly problematic when pumping slurries or liquids with suspended solids. Studies have found that even a small increase in the clearance between the impeller and the casing due to erosion can reduce pump efficiency by 2-5%. In severe cases, impeller erosion can lead to complete failure of the impeller, requiring costly replacement.
Sleeve / Shaft Wear
In addition to impacting the impeller, leaking fluid from a failed seal can also cause wear on the pump shaft or sleeve. As the fluid escapes, it can carry debris and contaminants that act as abrasives, gradually wearing away the surface of the shaft or sleeve. This wear can create grooves, scratches, or other irregularities that damage the sealing surfaces.
Gouging, Denting, Scratching of Shaft
Beyond gradual wear, seal failure can also result in more severe damage to the pump shaft, such as gouging, denting, or deep scratches. This typically occurs when the seal faces become misaligned or damaged, allowing hard particles to become trapped between the seal faces and the shaft.
As the shaft rotates, these trapped particles can create deep scratches or gouge marks in the shaft surface. Dents can also form if larger debris impacts the shaft with sufficient force. This type of damage can quickly lead to seal failure, as the scratches and dents provide leak paths for the pumped fluid.
Corrosion of Seal Shaft
Mechanical seal failure can expose the pump shaft to corrosive fluids, leading to accelerated corrosion and degradation of the shaft material. Many pumped fluids contain chemicals that can react with the metallurgy of the shaft, weakening it over time.
Corrosion is particularly detrimental because it can extend beyond the immediate sealing area, affecting a larger portion of the shaft. This widespread damage can complicate shaft repair and may necessitate complete replacement. Corrosion can also increase the surface roughness of the shaft, preventing the mechanical seal from achieving a tight seal even if the visible damage is machined away.
Flashing or Etching
For fluids with low boiling points, mechanical seal leakage can cause the fluid to vaporize rapidly as it experiences a pressure drop after escaping the pump. This rapid vaporization, known as flashing or etching, can wear away the seal faces and heat up the seal components, leading to premature failure. Flashing can also create localized high temperatures that cause thermal distortion of the seal faces, resulting in further leakage.
Fretting
Fretting occurs when there is relative motion between the mechanical seal components, often due to improper installation, poor lubrication, or distortion of the seal faces. This relative motion causes small-amplitude slip and friction between the surfaces, leading to wear and fatigue.
Fretting can create weakened areas in the seal faces that are prone to cracking and breakage. It can also generate small particles that contaminate the sealing surfaces, increasing abrasion and leakage.
Excessive Vibration and Noise
A failing mechanical seal can generate excessive vibration and noise, often indicating more severe underlying issues. As the seal faces wear down or become damaged, they may lose their smooth, flat surface, creating an imbalance that causes the shaft to vibrate. Leaking fluid can also cause cavitation, where rapid formation and collapse of vapor bubbles generate vibration and noise.
Pump Shutdown and Downtime
Ultimately, mechanical seal failure can lead to complete pump shutdown and unplanned downtime. When a seal fails catastrophically, it can cause secondary damage to other pump components, requiring extensive repairs. In some cases, the cost of repairing a severely damaged pump may exceed the cost of replacement.