Calculating the heat generated by mechanical seals is a complex but critical task in the machinery industry. Engineers need to accurately determine seal heat to prevent failures and optimize performance.
Without a clear understanding of the key parameters and formulas involved, costly mistakes can be made leading to reduced efficiency, increased downtime, and even catastrophic seal failures.
In this blog post, we’ll walk through step-by-step how to calculate mechanical seal heat. We’ll cover the essential seal geometry, operating conditions, and material properties to consider. You’ll learn the key formulas including the API 682 heat soak equation and see a practical example calculation.
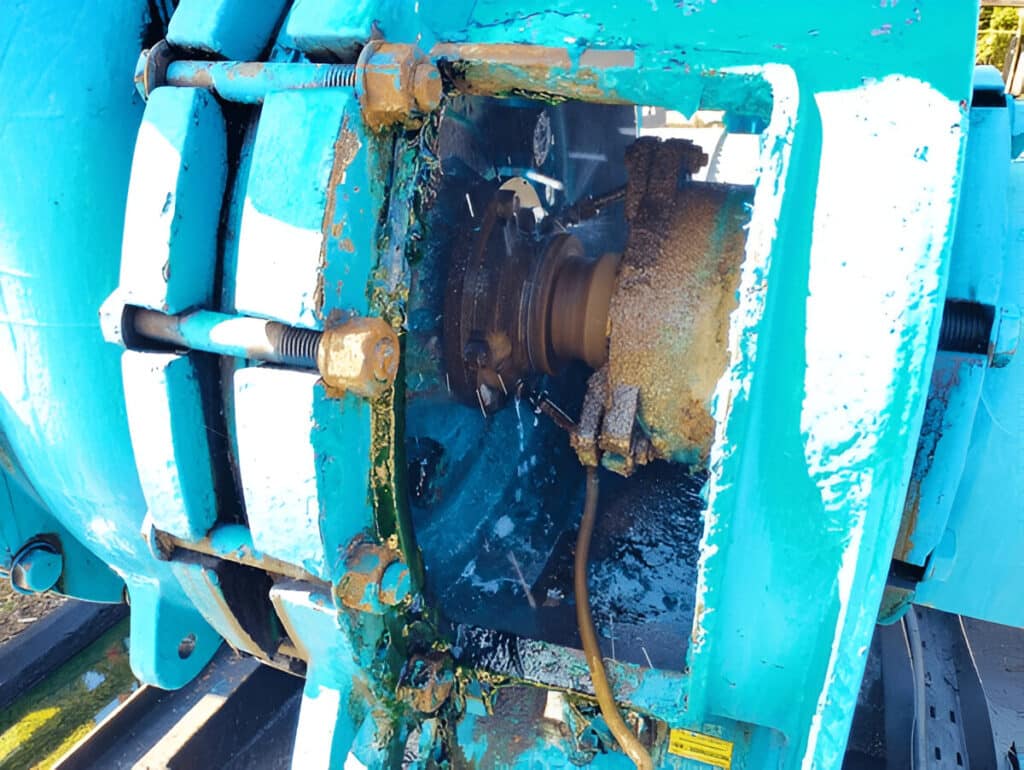
Seal Geometry and Dimensions
- Outer diameters of seal faces: The outside diameters of the rotating and stationary seal faces. These dimensions influence the amount of area exposed to friction and therefore heat generation.
- Inner diameters of seal faces: The inside diameters of the rotating and stationary seal faces. Along with the outer diameters, the inner diameters define the sealing area.
- Mean face diameter: The average of the outer and inner seal face diameters. The mean diameter is used to calculate the linear rubbing velocity based on the rotational speed.
Operating Conditions
- Rotational speed: The speed at which the shaft and rotating seal components spin, typically expressed in revolutions per minute (RPM). Higher speeds generate more frictional heat.
- Pressure differential: The difference in fluid pressure from the high pressure side to the low pressure side of the seal. High pressure differentials increase contact pressure between the seal faces, resulting in greater friction and heat.
- Fluid viscosity: The measure of a fluid’s resistance to flow. Higher viscosity fluids tend to generate more viscous shear and hydrodynamic friction in the seal interface.
- Temperature: The operating temperature impacts fluid properties and thermal expansion of seal components which affects interface geometry and heat generation.
Material Properties
- Thermal conductivity: The ability of the seal face materials to conduct heat. Higher thermal conductivity allows heat to dissipate more efficiently through the seal components.
- Specific heat: The amount of heat required to raise the temperature of the seal materials by one degree. Materials with higher specific heat values absorb more thermal energy.
- Density: The mass per unit volume of the seal materials. Density factors into the calculations for heat capacity and thermal inertia of the seal components.
Formulas for Calculating Heat by Mechanical Seals
Frictional Heat Generation Formula
The frictional heat generation formula is used to calculate the amount of heat generated at the sealing interface due to the relative motion between the seal faces. The formula is as follows:
H = f × P × V
Where:
- H is the frictional heat generation (W)
- f is the coefficient of friction (dimensionless)
- P is the contact pressure between the seal faces (Pa)
- V is the sliding velocity (m/s)
The coefficient of friction depends on various factors, such as the seal face materials, lubricating fluid properties, and surface roughness. The contact pressure is determined by the spring force and the hydraulic pressure acting on the seal faces. The sliding velocity is calculated based on the shaft diameter and rotational speed.
API 682 Heat Soak Equation
The American Petroleum Institute (API) Standard 682 provides a simplified equation for estimating the heat soak of a mechanical seal. The heat soak represents the amount of heat that is absorbed by the sealed fluid and the surrounding components. The API 682 heat soak equation is as follows:
Q = k × D × N
Where:
- Q is the heat soak (W)
- k is the seal factor (W/mm/rpm)
- D is the shaft diameter (mm)
- N is the shaft rotational speed (rpm)
The seal factor (k) is a empirical value that depends on the seal type, size, and operating conditions. API 682 provides recommended seal factor values for various seal arrangements and applications.
Practical Example: Step-by-Step Calculation
Let’s consider a practical example to illustrate the calculation of frictional heat generation and heat soak for a mechanical seal. Suppose we have a single mechanical seal with the following parameters:
- Shaft diameter (D): 50 mm
- Rotational speed (N): 3,000 rpm
- Seal face contact pressure (P): 1 MPa
- Coefficient of friction (f): 0.1
- API 682 seal factor (k): 0.5 W/mm/rpm
Step 1: Calculate the sliding velocity (V)
V = π × D × N / 60,000
V = π × 50 mm × 3,000 rpm / 60,000
V = 7.85 m/s
Step 2: Calculate the frictional heat generation (H)
H = f × P × V
H = 0.1 × 1,000,000 Pa × 7.85 m/s
H = 785 W
Step 3: Calculate the heat soak (Q) using the API 682 equation
Q = k × D × N
Q = 0.5 W/mm/rpm × 50 mm × 3,000 rpm
Q = 75,000 W = 75 kW
In this example, the frictional heat generation is 785 W, and the heat soak is 75 kW. These values provide insights into the thermal load on the sealing system and help in selecting appropriate seal materials, coolants, and heat dissipation methods.