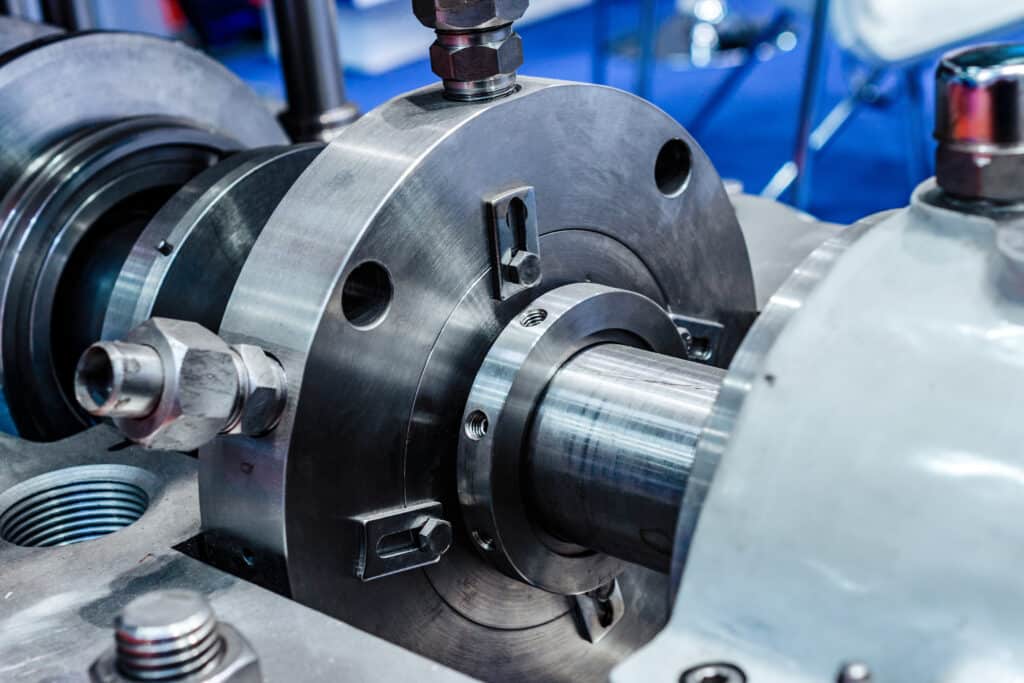
1. Review specifications and instructions
Before starting any mechanical seal installation, you need to check the manufacturer’s specifications. Every seal has specific compression requirements that must be followed exactly.
Look for the recommended compression distance in the technical data sheet. This number tells you how much to compress the seal for proper operation.
Write down important measurements like shaft diameter, seal chamber dimensions, and spring compression values. Having these numbers handy prevents mistakes during installation.
2. Inspect and prepare components
Examining all seal components before installation saves time and prevents failures. Check each part for damage, dirt, or manufacturing defects.
Clean all surfaces that will contact the seal using a lint-free cloth and appropriate solvent. Even tiny particles can cause seal leakage.
Measure the shaft runout with a dial indicator. If runout exceeds 0.003 inches, the seal won’t work properly.
Apply a thin film of compatible lubricant to O-rings and seal faces. This prevents damage during assembly and initial startup.
3. Install stationary member
The stationary seal member mounts in the seal chamber or gland plate. This component stays fixed while the shaft rotates.
Press the stationary seat into place using even pressure. Avoid tilting or cocking the seat during installation.
Check that the seat face sits perpendicular to the shaft centerline. Use a dial indicator to verify alignment within 0.002 inches.
Some designs require adhesive or set screws to secure the stationary member. Follow the manufacturer’s specific method for your seal type.
4. Mount the rotary member on the shaft
The rotary seal member attaches to the shaft and spins with it. This part includes the spring mechanism that provides sealing force.
Slide the rotary unit onto the shaft carefully. Don’t let the seal faces touch or drag across rough surfaces.
Position the rotary member at the approximate location specified in the instructions. You’ll adjust the exact position in the next steps.
For cartridge seals, loosen the centering clips but don’t remove them yet. These clips maintain proper spacing until final installation.
5. Position a setting gauge or plate
A setting gauge ensures accurate seal compression. This tool establishes the correct distance between seal faces.
Place the gauge against the stationary seal face or reference surface. The gauge thickness matches the required compression distance.
Some installations use a setting plate instead of a gauge. This plate bolts to the seal chamber and provides a positive stop for compression.
Mark the shaft at the back of the rotary unit before compression. This reference mark helps verify proper movement during compression.
6. Compress the seal
Compressing the seal activates the spring force needed for sealing. Push the rotary unit toward the stationary face until it contacts the setting gauge.
Apply steady, even pressure during compression. Sudden movements can damage the delicate seal faces.
Watch your reference mark on the shaft. It should move the exact distance specified for compression.
For pusher-type seals, you’ll feel increased resistance as the springs compress. Stop when you reach the gauge or specified compression distance.
7. Tighten the gland evenly
Securing the gland locks in the correct compression setting. Use a cross-pattern tightening sequence for glands with multiple bolts.
Tighten each bolt gradually in stages. First, hand-tighten all bolts, then use a wrench to reach 25% torque, 50% torque, and finally full torque.
Check compression distance after each tightening stage. The seal faces shouldn’t move once properly compressed.
Remove the setting gauge or plate after achieving full torque. For cartridge seals, remove the centering clips at this point.
8. Final checks
Verifying proper installation prevents early seal failure. Rotate the shaft by hand to check for binding or unusual resistance.
Measure the distance from the back of the rotary unit to your reference point. This confirms you achieved the correct compression.
Look for even gaps around the gland plate. Uneven gaps indicate misalignment that needs correction.
Document all measurements and settings for future reference. This information helps troubleshoot any problems that arise during operation.
Check for leaks during initial startup. A few drops during break-in is normal, but steady dripping indicates incorrect installation.