Mechanical seals are critical components in many industrial machines and equipment, preventing fluid leakage and ensuring safe, efficient operation. To guarantee seal performance and reliability, it is essential to thoroughly test mechanical seals before installation. This article will cover the three primary methods for testing mechanical seals: API 682 Air Test, Hydrostatic Test, and Dynamic Test.
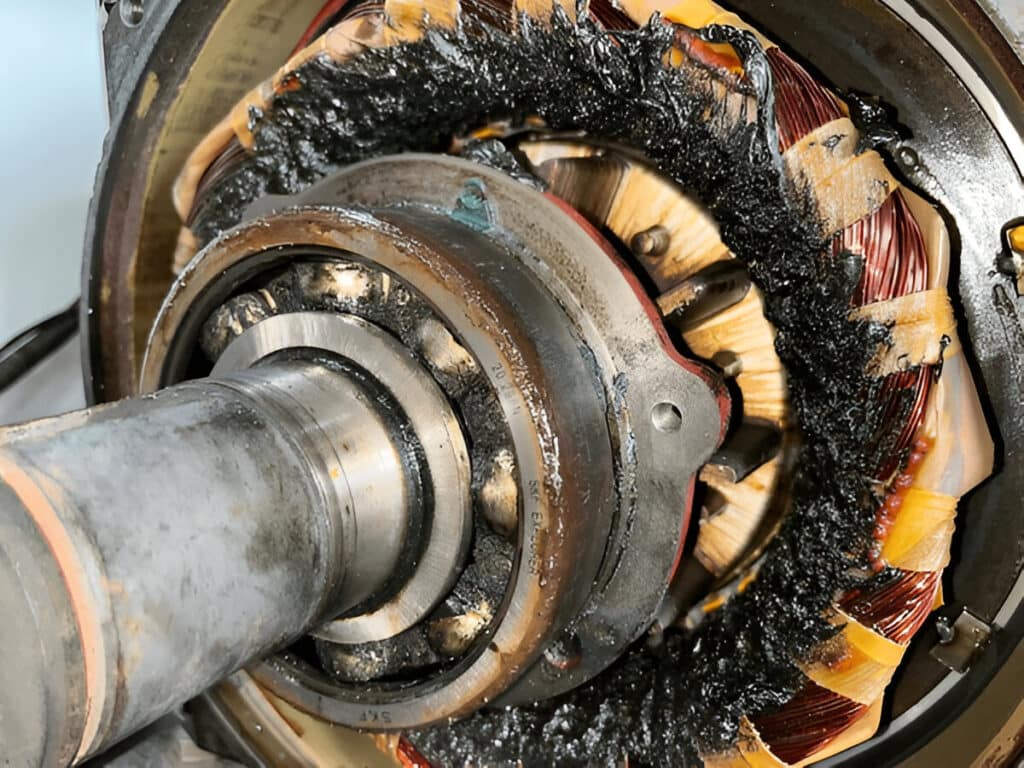
API 682 Air Test
The API 682 Air Test is a non-destructive testing method that checks for leaks in the mechanical seal assembly. Here are the steps to perform this test:
Step 1: Connect Air Supply
Attach a regulated compressed air supply line to the test fixture. Ensure all connections are tight to prevent leaks.
Step 2: Pressurize Seal Cavity
Slowly open the air supply valve to pressurize the seal cavity. Increase pressure gradually to the specified test value, usually in the 15-30 psig range. Monitor the pressure gauge to confirm the desired level is reached and stable. Controlled pressurization stresses the seal components in a manner similar to actual operating conditions.
Step 3: Check for Leaks
With the seal cavity pressurized, use a soap solution or commercial leak detection spray along seal joints, connections, and potential leak paths. Look closely for any bubbles forming, which indicate air leakage. Pay special attention to the seal faces, O-rings, and shaft interface.
Step 4: Depressurize and Evaluate
If no leaks are found after several minutes, slowly depressurize the seal cavity by releasing the air supply. Disassemble the seal from the test fixture and re-inspect the components. Assuming no issues are identified, the seal is verified leak-free and ready for installation. If leaks were detected, disassemble, diagnose and correct the issue, then repeat the air test.
Hydrostatic Test
The Hydrostatic Test evaluates the mechanical seal’s ability to withstand the system’s maximum operating pressure without leakage. Follow these steps:
Step 1: Fill with test fluid
Fill the test fixture with a suitable testing fluid, such as water or the actual process fluid, if compatible with the seal materials.
Step 2: Pressurize the system
Gradually increase the pressure inside the test fixture to the maximum operating pressure specified for the seal application. Maintain this pressure for a predetermined duration.
Step 3: Monitor for leaks
Closely observe the seal faces and gland area for any signs of fluid leakage during the test. Use collection methods to quantify any leakage.
Dynamic Test
The Dynamic Test assesses the mechanical seal’s performance under simulated operating conditions, including shaft rotation and system pressure. Here are the steps:
Step 1: Establish test conditions
Set up the test rig to simulate the system’s operating conditions, such as shaft speed, pressure, and temperature.
Step 2: Start the test
Initiate shaft rotation and gradually increase the speed to the specified operating range. Apply the system pressure and temperature as required.
Step 3: Monitor seal performance
Continuously monitor the seal for leakage, temperature rise, vibration, and other performance indicators during the test. Use appropriate instrumentation to collect data.
Step 4: Evaluate results
Analyze the collected data and compare it with the seal’s performance specifications. Assess factors such as leakage rates, face wear, and temperature stability.