Do you know the difference between internally and externally flushed mechanical seals?
In this blog post, we’ll explore the key distinctions between these two types of seals and their applications.
Internally flushed seals use the process fluid to lubricate and cool the seal faces, while externally flushed seals rely on an external fluid source.
Understanding these differences is crucial for selecting the right seal for your specific industrial needs.
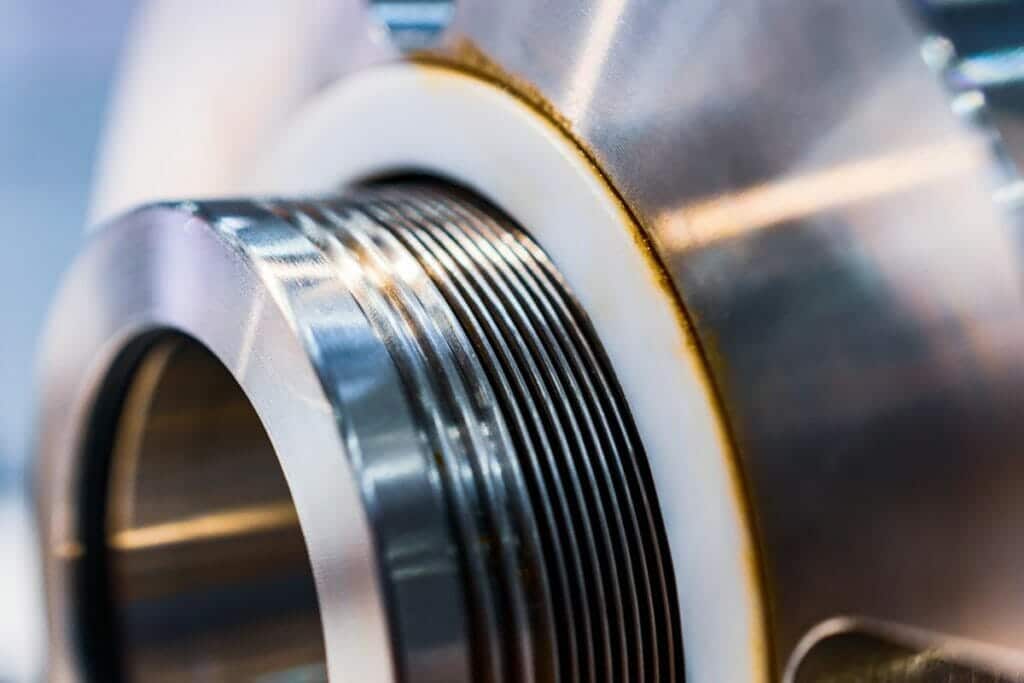
What is Internally Flushed Seals
Internally flushed mechanical seals are designed to circulate the process fluid within the seal chamber to provide cooling and lubrication. This internal circulation is achieved through the use of special features such as internal circulating devices or flow channels incorporated into the seal design.
The process fluid is directed from the high-pressure side of the seal to the low-pressure side, creating a flow path that helps to dissipate heat and prevent the accumulation of solids or contaminants within the seal chamber.
Advantages of Internally Flushed Seals
- Internally flushed seals benefit from effective cooling due to the high velocity of the flushing fluid and efficient heat transfer.
- Since the flushing fluid is sourced from the process itself, there is no dilution of the process fluid. This maintains the integrity of the process and eliminates the need for additional separation or treatment.
- Internally flushed seals are self-contained and do not require any external piping or control systems. This simplifies installation, reduces costs, and minimizes potential points of failure.
Limitations of Internally Flushed Seals
- In internally flushed seals, the seal faces are directly exposed to the process fluid conditions, such as high temperatures, solids content, and aggressive chemicals. This exposure can accelerate seal wear and reduce seal life.
- The presence of debris and abrasive particles in the process fluid poses a risk of seal damage in internally flushed seals. These particles can cause scratching, scoring, or erosion of the seal faces, compromising seal performance and leading to premature failure.
Application of Internally Flushed Seals
Internally flushed seals are well-suited for applications involving low-viscosity fluids such as water, coolants, and light oils.
Internally flushed seals are also ideal for high-speed rotary applications, as the flushing action helps to dissipate heat and maintain optimal sealing performance. This makes them particularly useful in pumps, compressors, and turbines.
API Flush Plans for internal flushing
API Flush Plans offer effective solutions for internal flushing of seals. Plan 11 and Plan 13 are designed to handle smaller seals with precision and efficiency.
For larger and more complex seals, Plan 21 and Plan 23 are the ideal choices. These plans ensure thorough flushing and optimal performance.
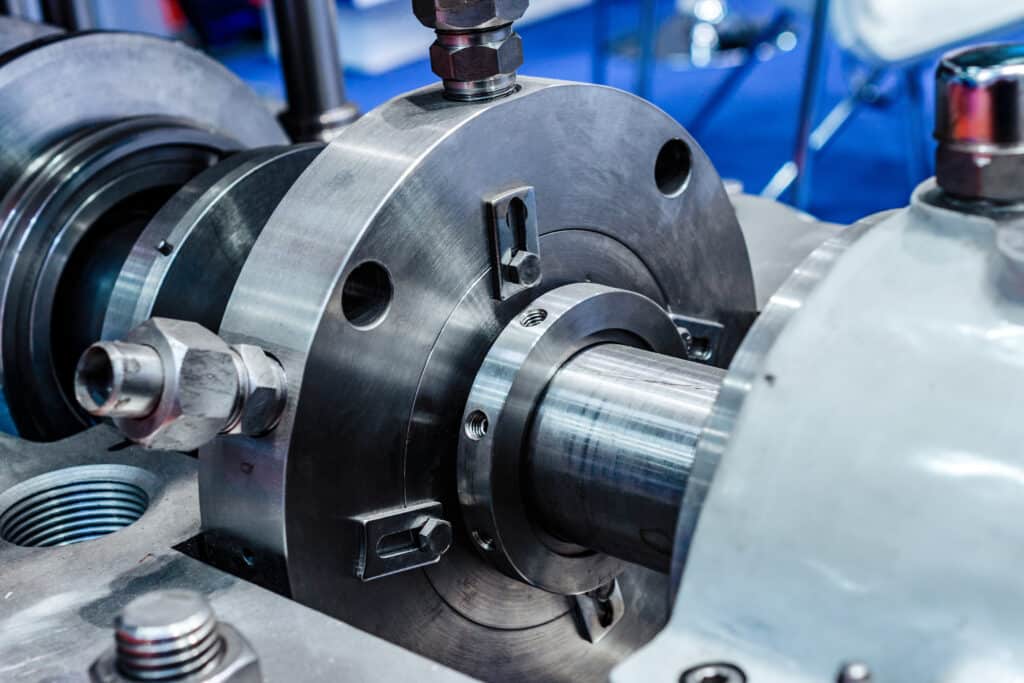
What is Externally Flushed Seals
Externally flushed seals introduce a clean, cool fluid from an external source into the seal cavity. This fluid is at a pressure higher than the product pressure, effectively preventing process fluid from entering the seal cavity.
The external flush is typically controlled by a flow control device, ensuring a consistent and appropriate flow rate to maintain the proper environment within the seal cavity. Externally flushed seals are commonly used in applications involving high temperatures, abrasive particles, or polymerizing fluids that could damage the seal faces without proper flushing.
Advantages of Externally Flushed Seals
- Externally flushed seals isolates the seal from harsh process fluids.
- With externally flushed seals, the flushing fluid can be optimized for compatibility with the seal materials and to provide optimal cooling.
- Monitoring and controlling the flush flow and pressure is easier with externally flushed seals.
Limitations of Externally Flushed Seals
- Externally flushed seals require additional infrastructure, including external flush piping, controls, and monitoring systems. This added complexity increases installation and maintenance costs.
- The introduction of an external flush fluid poses a risk of contaminating the process fluid.
- Pumping and cooling the flush fluid consumes more energy compared to internally flushed seals.
- The reliance on external systems makes externally flushed seals more vulnerable to failures caused by issues with the flush piping, controls, or monitoring components.
Application of Externally Flushed Seals
Externally flushed mechanical seals find extensive use in applications involving abrasive or corrosive fluids. These seals employ a clean, pressurized flush fluid that is introduced from an external source into the seal chamber.
Externally flushed seals are particularly beneficial in applications where the process fluid is prone to crystallization, polymerization, or solidification. The constant flow of clean flush fluid helps to keep the seal faces clean and free from build-up, ensuring optimal sealing performance and prolonging seal life.
API Flush Plans for External Flushing
API flush plans 32, 54, and 55 are designed for externally flushed mechanical seals. These plans specify the piping arrangements and instrumentation required to properly flush and cool the seals.
Plan 32 utilizes a clean external flush fluid, while plans 54 and 55 incorporate a pressurized external barrier fluid reservoir. The barrier fluid maintains a higher pressure than the process fluid, preventing contamination and enhancing seal performance.
In conclusion
Internally and externally flushed mechanical seals each have their own advantages and use cases. The choice between them depends on the specific application and system requirements.
For personalized recommendations on selecting the right mechanical seal for your needs, consult with our experts today.