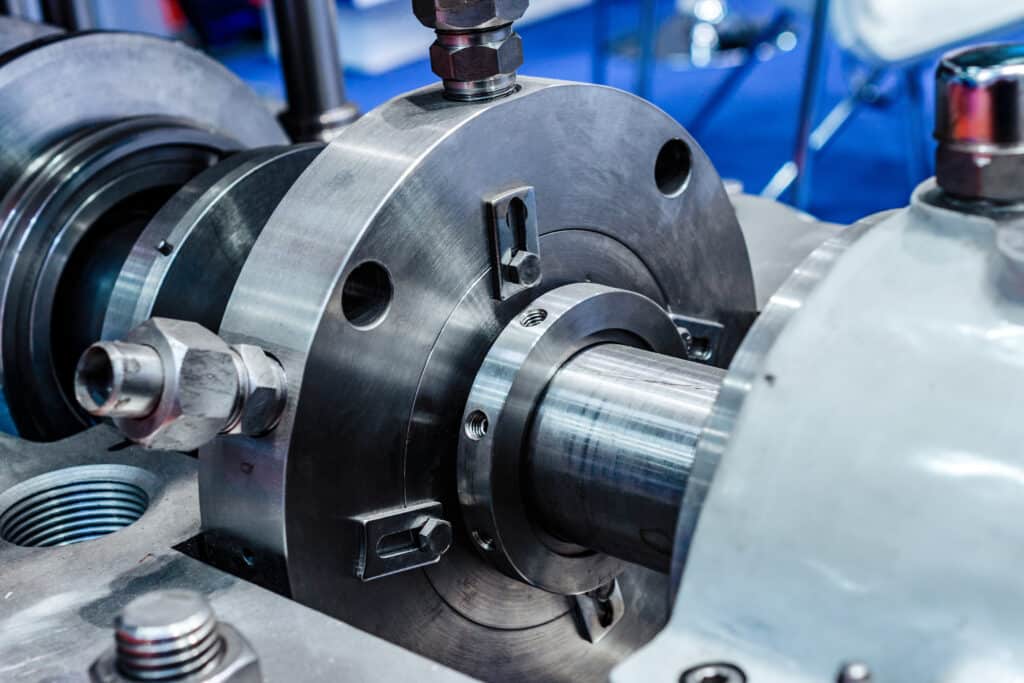
Double mechanical seal arrangements come in three main types: back-to-back, tandem, and face-to-face.
Back-to-Back Arrangement
Back-to-Back Arrangement Working Principle
Back-to-back mechanical seal arrangements position two seals facing away from each other, with primary sealing surfaces on the outer sides. This configuration creates a barrier fluid chamber between the seals, pressurized higher than the process fluid. The barrier fluid lubricates seal faces, removes heat, and prevents process fluid leakage to the atmosphere.
The higher pressure in the barrier fluid chamber forces both seals against their stationary seats. This pressure differential ensures inward leakage from the barrier fluid to the process fluid, not outward.
Advantages of Back-to-Back Arrangement
Superior Protection and Design
Back-to-back mechanical seal arrangements provide superior protection against seal failure and product leakage. The balanced design ensures optimal operating conditions for both seals, reducing wear and extending seal life.
Improved Pressure Distribution and Heat Dissipation
This configuration offers improved pressure distribution. The barrier fluid between the seals is pressurized higher than the process fluid, preventing contamination if the inner seal fails. It also allows better heat dissipation, keeping the seals cooler and more efficient.
Simplified Installation and Maintenance
Installation and maintenance of back-to-back seals are simplified. The cartridge design facilitates replacement, reducing downtime and labor costs. Monitoring the barrier fluid pressure enables early detection of seal wear or failure, preventing unexpected shutdowns.
Excellence in Handling Challenging Fluids
Back-to-back arrangements excel in handling volatile, hazardous, or expensive fluids. They offer an extra layer of protection against leaks, ensuring safer operation and minimizing product loss. This configuration adapts well to applications with varying pressure conditions, accommodating fluctuations more effectively than other seal types.
Disadvantages of Back-to-Back Arrangement
Maintenance and Installation Challenges
Back-to-back mechanical seal arrangements require higher maintenance due to their complexity. Installation and alignment challenges can increase downtime during repairs or replacements. Seal face damage may occur if barrier fluid pressure drops below process fluid pressure, leading to contamination and seal failure.
Cost Considerations
These configurations are more expensive than single seals or tandem arrangements due to intricate design and additional components. Spare parts and maintenance costs accumulate over time. Back-to-back seals occupy more axial space, limiting their use in certain pump types or constrained environments.
Sensitivity to Shaft Alignment
Sensitivity to shaft deflection and misalignment is a concern for back-to-back seals. Proper shaft support and alignment are crucial to prevent premature wear and failure of seal faces. The complex design and additional components contribute to higher initial costs and ongoing maintenance expenses.
Barrier Fluid System Management
Pressure fluctuations or inadequate fluid supply can compromise seal integrity and lead to system failures.
Applications of Back-to-Back Arrangement
Applications in Chemical and Pharmaceutical Industries
Back-to-back mechanical seal arrangements excel in applications requiring stringent process fluid containment. These seals are prevalent in industries handling hazardous, toxic, or expensive fluids. Chemical processing plants employ them for reactors and mixers dealing with corrosive substances. Pharmaceutical manufacturers use back-to-back seals to protect sensitive drug compounds from contamination during production.
Use in Oil, Gas, Food, and Paper Industries
Oil and gas refineries implement these arrangements in pumps processing volatile hydrocarbons, enhancing safety and preventing product loss. Food and beverage production facilities utilize back-to-back seals to maintain hygiene standards and prevent product contamination. Pulp and paper mills rely on these seals to handle abrasive slurries while minimizing leakage.
Applications in Power Generation, Water Treatment, and Aerospace
The power generation sector incorporates back-to-back seals in boiler feed pumps and turbine applications, where high pressures and temperatures are common. Water treatment facilities use these arrangements to seal pumps handling various chemicals and wastewater. The aerospace industry employs back-to-back seals in fuel pumps and hydraulic systems, ensuring reliable performance under extreme conditions.
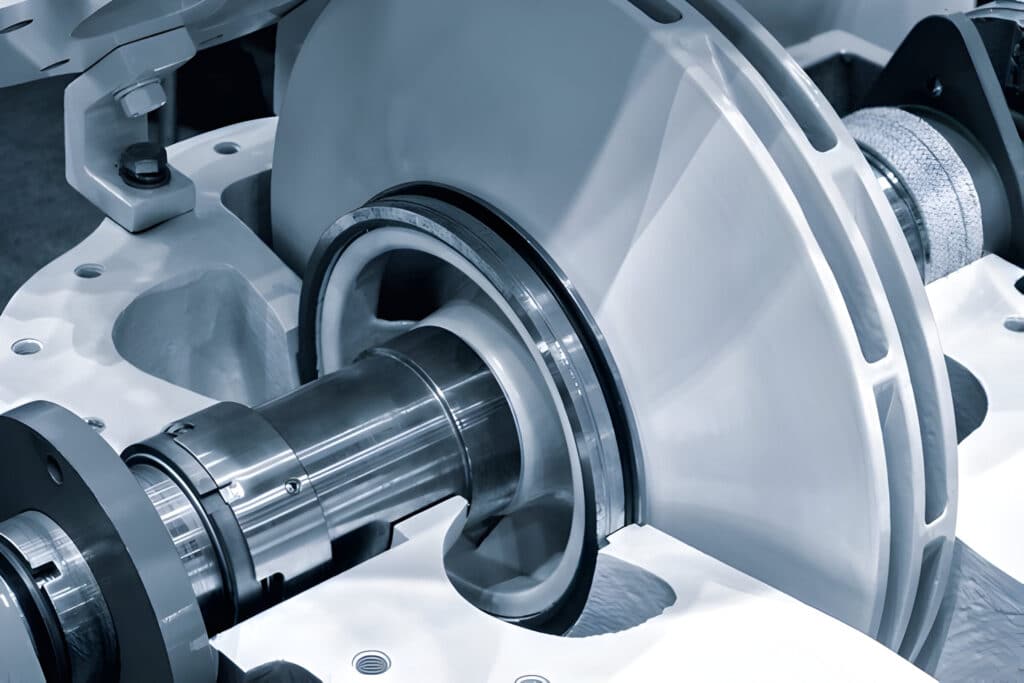
Tandem (Face-to-Back) Arrangement
Tandem (Face-to-Back) Arrangement Working Principle
Tandem (face-to-back) arrangements employ two seals for enhanced leak protection. The primary seal contacts the process fluid, while the secondary seal faces the atmosphere. A buffer fluid occupies the space between these seals, maintained at a pressure slightly below that of the process fluid.
The rotating shaft activates the primary seal, containing the process fluid and preventing its entry into the buffer chamber. Any minor leakage is absorbed by the buffer fluid. The secondary seal then blocks the buffer fluid from atmospheric release. This configuration creates a controlled environment, minimizing process fluid contamination and reducing emissions.
Buffer fluid serves multiple functions in this arrangement. It lubricates and cools both seals, extending their operational life. It also acts as a protective barrier, shielding the secondary seal from direct contact with potentially harmful process fluids. In the event of primary seal failure, the lower pressure of the buffer fluid allows for a controlled leak into the buffer chamber. This triggers alarms and enables maintenance before catastrophic failure occurs.
Advantages of Tandem (Face-to-Back) Arrangement
Pressure Handling and Durability
Tandem arrangements handle higher pressures compared to single seals, making them suitable for demanding applications. They better tolerate shaft misalignment and vibration, reducing wear and extending seal life. The design allows for easier maintenance, as the primary seal can be replaced without disturbing the secondary seal or removing the entire assembly.
Heat Dissipation and Material Flexibility
The buffer fluid between the seals in a tandem arrangement improves heat dissipation, cooling the primary seal and preventing overheating. This extends the seal’s lifespan. The configuration also offers flexibility in seal material selection, allowing different materials for each seal to optimize performance based on specific process conditions.
Versatility and Robustness
Tandem (face-to-back) arrangements provide robust and versatile sealing solutions for various industrial applications. Their ability to handle high pressures, improve reliability, and facilitate maintenance.
Disadvantages of Tandem (Face-to-Back) Arrangement
Space and Design Challenges
Tandem (face-to-back) arrangements require more axial space, posing challenges in compact machinery designs. The increased length can lead to shaft deflection issues, potentially compromising seal performance and longevity. These configurations involve two separate seal assemblies, increasing system complexity and resulting in higher installation and maintenance costs compared to single seals or other double seal arrangements.
Limited Containment and Pressure Capabilities
Tandem arrangements are less effective in containing process fluids than other double seal configurations. In the event of inner seal failure, the outer seal becomes the sole barrier against leakage, providing less containment than a back-to-back arrangement. These systems have limited pressure capabilities, typically handling lower differential pressures than back-to-back configurations. This restriction may limit their use in high-pressure applications.
Thermal Management Limitations
Heat dissipation is less efficient in tandem arrangements, affecting seal performance in temperature-sensitive processes. The design’s inherent limitations in thermal management can impact overall system reliability and efficiency.
Applications of Tandem (Face-to-Back) Arrangement
Applications in Light Hydrocarbons and VOCs
Tandem arrangements excel in processes handling light hydrocarbons, volatile organic compounds (VOCs), and fluids with low viscosity and specific gravity. These seals minimize product contamination by preventing buffer fluid in the outer seal from mixing with process fluid.
Varying Pressure Conditions
Tandem seals perform well in varying pressure conditions. The outer seal accommodates pressure fluctuations without compromising inner seal performance. This makes them suitable for equipment with frequent start-stops or intermittent operation.
High-Speed Applications
High-speed applications benefit from tandem arrangements’ effective heat dissipation capabilities. In environments where occasional leakage is acceptable but containment necessary, these seals provide an effective solution.
Pharmaceutical and Food Processing
Tandem arrangements find application in pharmaceutical and food processing industries. Their ability to maintain product purity and prevent contamination aligns with strict hygiene requirements in these sectors.
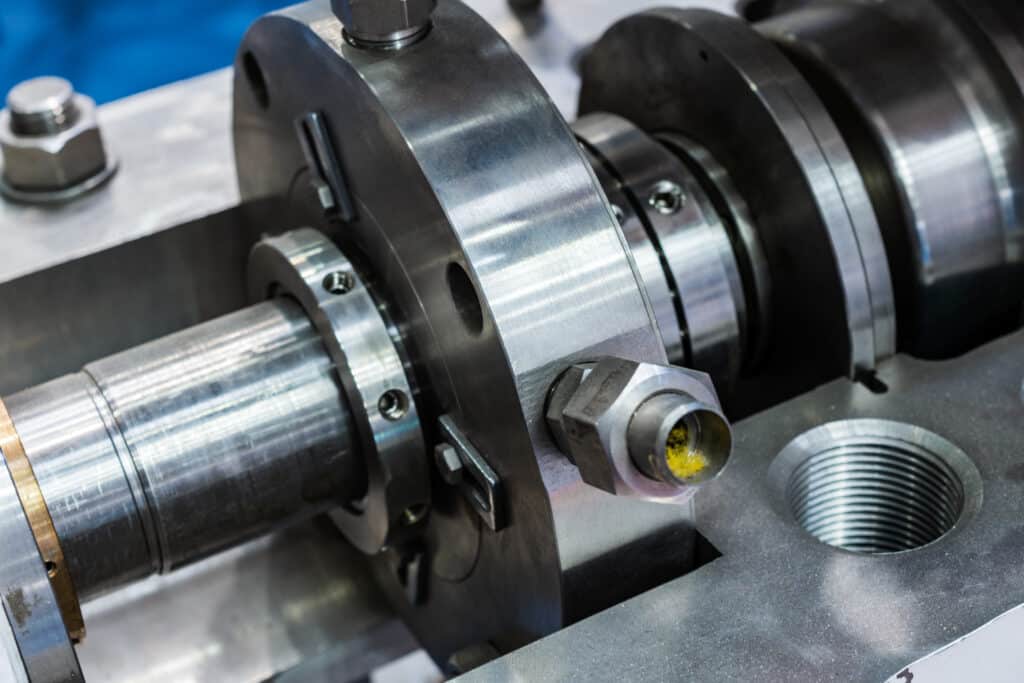
Face-to-Face Arrangement
Face-to-Face Arrangement Working Principle
Face-to-face double mechanical seal arrangements feature two seals positioned with opposing faces, creating a sealed chamber between them. This chamber contains a barrier fluid, integral to the seal’s operation.
During shaft rotation, both seals collaborate to prevent leakage. The inner seal contacts the process fluid, while the outer seal interfaces with the atmosphere or secondary containment system. The barrier fluid lubricates seal faces, dissipates heat, and maintains higher pressure than the process fluid. This pressure differential ensures inward leakage, safeguarding against product loss and environmental contamination.
Face-to-face arrangements offer protection against dry running. If barrier fluid pressure drops, both seals can function independently, providing a failsafe mechanism. This design facilitates easy installation and maintenance, allowing seal replacement without disturbing the other.
The arrangement’s working principle relies on the interaction between seal faces, barrier fluid, and pressure differentials. As the shaft rotates, the seal faces create a thin fluid film, minimizing friction and wear. The barrier fluid’s higher pressure forces it into the gap between seal faces, forming a stable liquid seal. This liquid seal prevents process fluid from escaping and external contaminants from entering.
Advantages of Face-to-Face Arrangement
Protection Against Shaft Deflection
Face-to-face double mechanical seal arrangements protect against shaft deflection. The proximity of seal faces maintains alignment under challenging operating conditions. This configuration simplifies installation and maintenance, reducing downtime and easing seal servicing without disturbing equipment alignment.
Improved Heat Dissipation
Heat dissipation improves with face-to-face arrangements. Barrier fluid between seals removes heat generated by seal face friction, extending seal life and enhancing performance. This configuration tolerates reverse pressure scenarios, making it suitable for applications with frequent pressure fluctuations.
Compact Design
Face-to-face seals feature a compact design, requiring less axial space than other arrangements. This characteristic makes them ideal for equipment with limited installation space. The reduced overall seal weight benefits certain applications where minimizing mass is crucial.
Increased Longevity and Reliability
The arrangement’s efficiency in heat management and pressure handling contributes to increased seal longevity and reliability. This translates to reduced maintenance frequency and operational costs for industrial processes employing face-to-face double mechanical seals.
Disadvantages of Face-to-Face Arrangement
Thermal Distortion and Pressure Limitations
Thermal distortion susceptibility increases, leading to seal face damage and heightened leakage. Lower pressure capability compared to back-to-back configurations limits use in high-pressure applications.
Installation and Maintenance Challenges
Installation and maintenance challenges arise due to reduced accessibility of inner seal faces. This complicates inspection and replacement, potentially increasing downtime and maintenance costs. Trapped fluid between seal faces can cause hydraulic lock, impeding seal opening and risking face damage during startup.
Sensitivity to Shaft Deflection and Misalignment
Sensitivity to shaft deflection and misalignment affects seal performance and lifespan in face-to-face arrangements. The required axial space may restrict use in compact equipment designs, limiting application in space-constrained environments.
Applications of Face-to-Face Arrangement
Low-Pressure and Thermal Expansion Benefits
Low-pressure differential applications benefit from face-to-face arrangements. They effectively manage thermal expansion by accommodating axial shaft movement. Corrosive or abrasive media applications favor this arrangement, as it shields the vulnerable outboard seal from direct exposure to harsh process fluids.
Vertical Pumps and Light Hydrocarbons
Vertical pumps handling light hydrocarbons or volatile organic compounds often utilize face-to-face seals. These seals maintain face lubrication even when the pump is idle, preventing dry running and extending seal life. Equipment undergoing frequent cycling benefits from face-to-face arrangements, as they minimize seal face wear during startup and shutdown procedures.
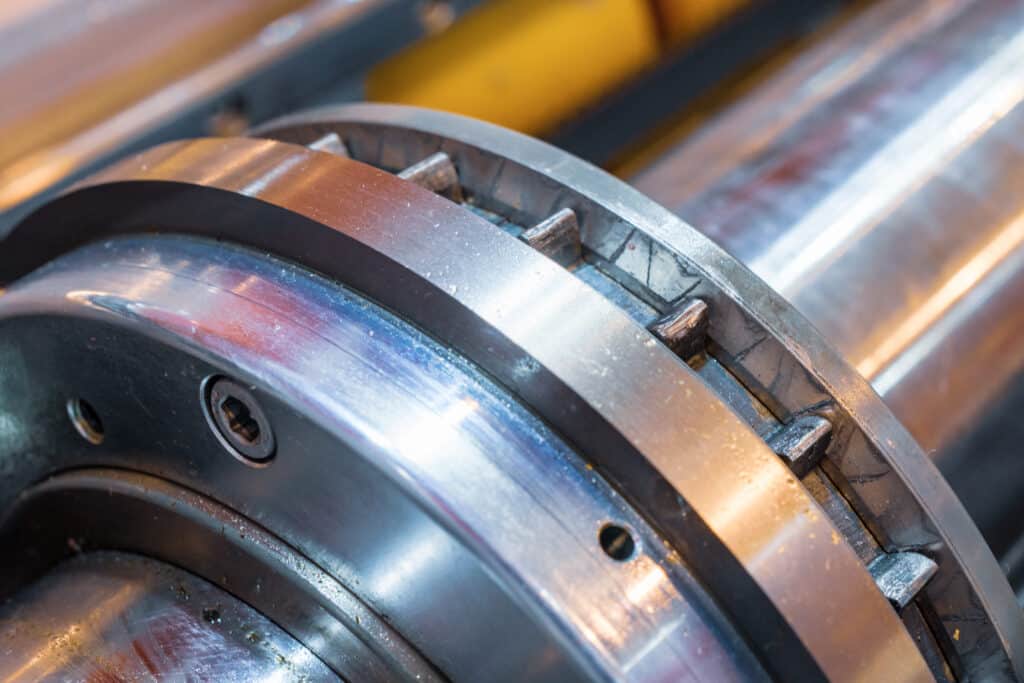
Selecting the Optimal Double Seal Arrangement
Fluid Properties
Fluid properties significantly influence double mechanical seal arrangement selection. Viscosity affects the seal’s ability to maintain a stable fluid film. Higher viscosity fluids require wider seal faces and deeper grooves for proper lubrication.
Temperature impacts seal material performance and fluid viscosity. Seal materials must withstand the operating temperature range without degradation or excessive thermal expansion.
Fluid corrosiveness dictates seal face and elastomer material selection. Materials resistant to chemical attack prevent premature seal failure.
Fluid crystallization or polymerization tendencies can affect seal performance. Special seal designs or barrier fluid systems may be necessary to prevent build-up on seal faces.
Abrasive fluids may require harder seal face materials or special seal designs to minimize wear and extend seal life.
Pressure
Process pressure and barrier fluid pressure influence the selection of double mechanical seal arrangements. High-pressure applications require tandem seals, which withstand increased stress better than face-to-face configurations. Extremely high pressures necessitate back-to-back arrangements for optimal pressure resistance.
Low-pressure scenarios offer more flexibility. Face-to-face arrangements prove cost-effective and easier to maintain, making them suitable for various industries.
Temperature
Process fluid and seal chamber temperatures influence the choice. High temperatures impact seal materials, lubricants, and overall performance.
Tandem arrangements with cooler buffer fluid suit high-temperature applications. This configuration dissipates heat and shields the outer seal from thermal stress. Back-to-back arrangements with pressurized barrier fluid excel in extreme temperature conditions, offering enhanced cooling and lubrication for both seal faces.
Temperature fluctuations require consideration. Rapid changes cause thermal shock, potentially damaging seal components. Face-to-back configurations with flexible mounting accommodate thermal cycling effectively.
Speed
High-speed applications above 3,600 RPM require balanced seal designs to mitigate centrifugal forces and maintain stability. These designs minimize heat generation and wear.
Low-speed operations below 1,000 RPM allow simpler seal arrangements due to reduced dynamic forces. Adequate lubrication and cooling are essential, as slower speeds may limit fluid circulation in the seal chamber.
Medium-speed applications between 1,000 and 3,600 RPM offer more flexibility in seal arrangement choices. Consider pressure, temperature, and fluid properties alongside speed when selecting.
Match seal face materials and spring loads to operating speed. Higher speeds may necessitate harder face materials and adjusted spring tension to maintain proper seal contact without excessive wear.
Space Constraints
Face-to-face configurations occupy less axial space, suiting compact machinery but requiring more radial space for seal components. Back-to-back arrangements need more axial space but offer advantages in radial space requirements, making them suitable for limited radial space scenarios. Tandem arrangements demand the most axial space, unsuitable for equipment with tight axial constraints.
Consider space for auxiliary systems, including piping and barrier fluid circulation reservoirs. Some arrangements require extensive support systems, affecting overall space needs. Ensure sufficient room for seal replacement and maintenance tasks.
Cost
Initial investment must be balanced against long-term operational expenses. Face-to-face arrangements often have lower upfront costs but require more frequent maintenance. Back-to-back configurations may have higher initial costs but offer better performance and longevity, potentially reducing overall costs over time.
FAQs
How Often Should Double Mechanical Seals Be Inspected and Maintained?
Double mechanical seals should be inspected every 3-6 months and maintained annually. However, manufacturers’ recommendations should be followed, as inspection frequency may vary based on usage and operating conditions.
What Are the Typical Costs Associated With Installing Double Mechanical Seals?
Double mechanical seal installation costs typically range from $1,000 to $10,000+. Prices vary based on seal size, materials, complexity, and labor.
Can Double Mechanical Seals Be Retrofitted to Existing Equipment?
Double mechanical seals can be retrofitted to existing equipment, subject to compatibility factors like shaft size, housing dimensions, and available space. Professional assessment is recommended to determine feasibility for specific machinery.