Bellows are essential components in various industrial applications, enabling flexibility and precision in machinery systems. However, not all bellows are created equal – welded and formed bellows have distinct characteristics that impact their suitability for different use cases.
This article will explore the key differences between welded and formed bellows, including their manufacturing processes, material options, performance characteristics, cost considerations, and typical applications.
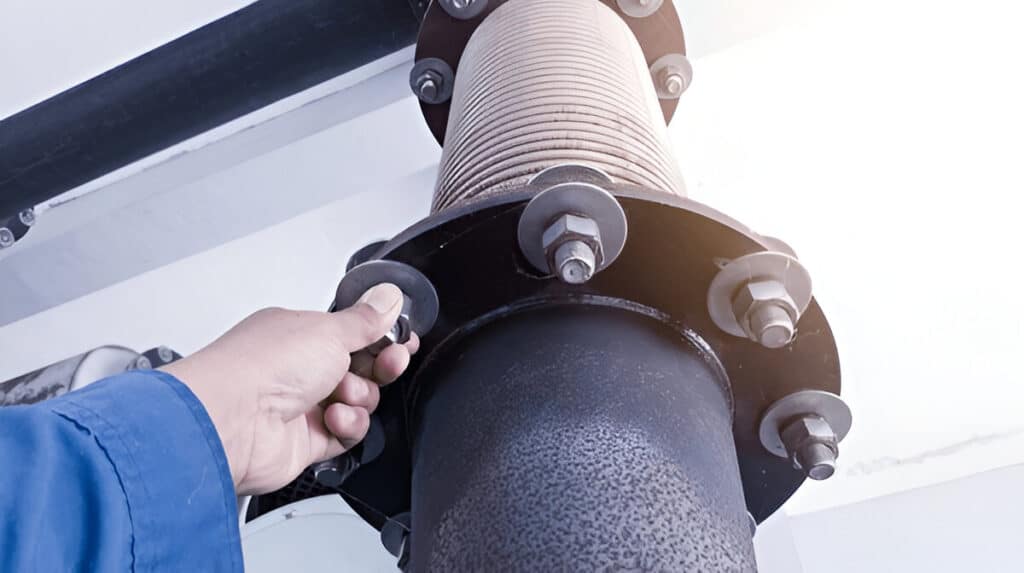
What is a Welded Bellow
A welded bellow is a type of metal bellow that is manufactured by welding together individual diaphragms or discs. The diaphragms are typically stamped from thin metal sheets and then stacked together with a slight gap between each layer. The edges of the diaphragms are then welded, either by laser, electron beam, or TIG welding processes, to form a sealed, flexible bellow.
The welding process fuses the diaphragms together into a strong, homogenous structure. This allows welded bellows to be made from materials as thin as 0.002 inches, enabling very high flexibility. The stacked construction also gives welded bellows their characteristic accordion-like appearance.
What is a Formed Bellow
Formed bellows, also known as hydroformed or hydraulically-formed bellows, are created from a single piece of thicker-walled tubing. The tubing, which can range from around 0.005 to over 0.040 inches thick, is placed in a forming die. High pressure hydraulic fluid is then pumped into the tube, causing it to expand and conform to the shape of the surrounding die.
The hydroforming process introduces circumferential corrugations along the length of the tube, giving it the bellow shape. The depth, quantity, and overall shape of the corrugations is determined by the forming die design. Once formed, the ends of the bellow are typically trimmed and finished by welding on end fittings or flanges.
Key Difference Between Welded and Formed Bellows
Manufacturing Processes
Welded bellows are constructed by welding individual diaphragms together to form the bellows. This process involves precision welding techniques such as laser welding, TIG welding, or resistance welding. The diaphragms are typically stamped or hydroformed from thin metal sheets before being welded together.
Formed bellows are created through a process called roll forming or hydro forming. A thin-walled tube is placed over a mandrel and then pressurized internally, causing the tube to expand and form convolutions. This process is repeated until the desired number of convolutions is achieved. The ends of the formed bellows are then trimmed and finished.
Material Options
Welded bellows offer a wider range of material options compared to formed bellows. They can be manufactured from various metals, including stainless steel, Inconel, Hastelloy, titanium, and other exotic alloys.
Formed bellows are more limited in terms of material options. They are typically made from ductile metals that can withstand the forming process without cracking or tearing. The most common materials for formed bellows are stainless steel, brass, and bronze.
Performance Characteristics
Welded bellows generally offer superior performance characteristics compared to formed bellows. They can withstand higher pressures and temperatures due to their multi-ply construction and the strength of the welded joints. Welded bellows also provide greater flexibility and motion capability, as the individual diaphragms can flex independently.
Formed bellows, while not as robust as welded bellows, still offer good performance within their design limits. They are suitable for applications with moderate pressure and temperature requirements. Formed bellows have a lower spring rate compared to welded bellows, which means they require less force to compress or extend.
Cost
The cost of welded bellows is typically higher than formed bellows due to the more complex manufacturing process and the use of high-performance materials. The precision welding techniques and the need for skilled labor contribute to the higher cost of welded bellows.
Formed bellows are generally less expensive to manufacture. The roll forming or hydro forming process is more automated and requires less skilled labor compared to welding. Additionally, the materials used for formed bellows are often less costly than those used for welded bellows.
Applications
Welded bellows are commonly used in aerospace, oil and gas, cryogenics, and vacuum systems. Welded bellows are ideal for applications that involve extreme temperatures, high pressures, or corrosive media.
Formed bellows are suitable for a wide range of general-purpose applications where the performance requirements are less demanding. They are often used in HVAC systems, automotive exhaust systems, and industrial equipment. Formed bellows are also commonly found in mechanical seals, expansion joints, and flexible couplings.