Metal bellows are essential components for applications requiring flexible seals, motion accommodation, and pressure sensing. The range of manufacturing processes and geometries for metal bellows provide unique capabilities but also add complexity for designers and engineers.
In this post, we’ll explore the five main types of metal bellows – formed, welded, electroformed, multi-ply, and edge-welded – detailing their distinct characteristics, advantages and limitations. By understanding the nuances of each type, you can confidently specify the optimal metal bellows for your application.
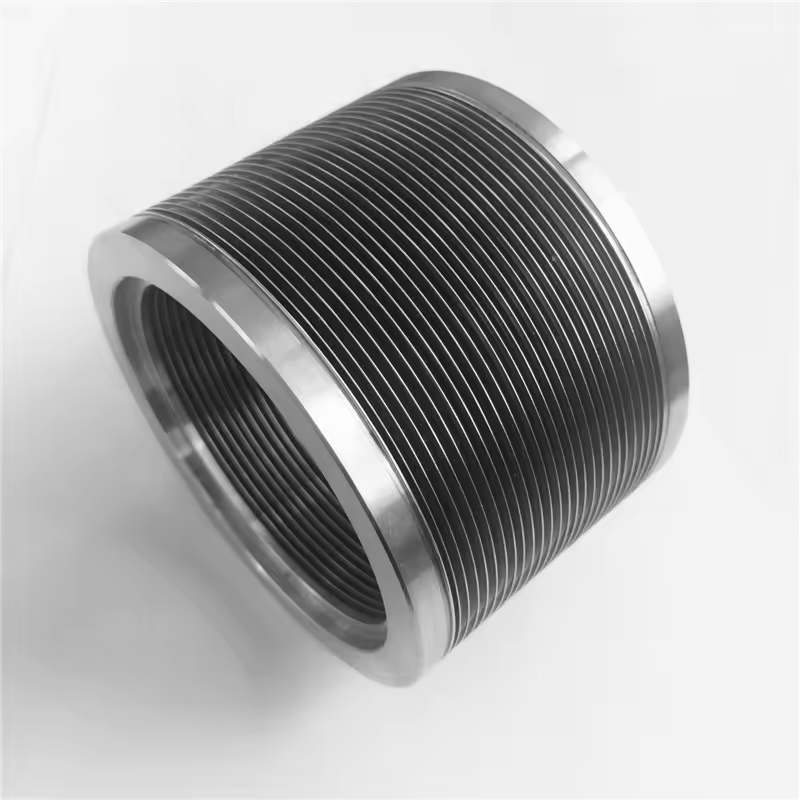
What Are Metal Bellows
Metal bellows are flexible, thin-walled metal components that can be compressed, extended, or bent to accommodate motion or vibration. They are designed to contain pressure, vacuum, or mechanical forces in a variety of applications. Metal bellows are made from ductile metals such as stainless steel, nickel alloys, titanium, or copper and feature a series of convolutions or corrugations that allow for flexibility.
Types of Metal Bellows
Formed Bellows
Formed bellows are manufactured through hydroforming or deep drawing processes. In hydroforming, a metal tube is placed inside a mold and then subjected to high-pressure fluid, causing the metal to conform to the shape of the mold. Deep drawing, on the other hand, involves pressing a flat metal sheet into a die to create the desired shape. These manufacturing methods make formed bellows cost-effective for high-volume production runs.
One advantage of formed bellows is their moderate flexibility, which allows them to accommodate axial, lateral, and angular movements. However, they have lower mechanical strength compared to other types of bellows, which may limit their use in high-pressure or high-stress applications.
Welded Bellows
Welded bellows are created by welding individual diaphragms together. The diaphragms are typically stamped or formed from metal sheets and then joined using various welding techniques, such as laser, electron beam, or resistance welding. This manufacturing process enables the production of bellows with high precision and durability.
The strength of welded bellows makes them suitable for demanding environments, such as those involving high temperatures, pressures, or corrosive media. However, the welding process can introduce potential weak points at the weld joints, which may be susceptible to fatigue or corrosion.
Electroformed Bellows
Electroformed bellows are produced by electroplating metal onto a precision-machined mandrel or mold. The electroplating process involves depositing thin layers of metal, such as nickel or copper, onto the mandrel until the desired thickness is achieved. The mandrel is then removed, leaving a seamless, thin-walled bellows.
The thin walls of electroformed bellows provide extreme flexibility, making them ideal for applications requiring high levels of movement or vibration isolation. They are also lightweight and can be manufactured with high precision. However, the electroforming process limits the material options available, and the resulting bellows may have lower durability compared to welded designs.
Multi-Ply Bellows
Multi-ply bellows consist of multiple layers of thin metal sheets stacked together. The layers are typically joined using adhesives or brazing. The number of layers and the thickness of each layer can be varied to achieve the desired strength and flexibility.
The multi-layer construction enhances the strength and flexibility of these bellows, making them suitable for high-pressure or cyclic loading applications. The multiple layers also provide redundancy, reducing the risk of failure if one layer is damaged.
Edge-Welded Bellows
Edge-welded bellows are constructed by welding thin metal diaphragms along their edges to create convolutions. This process results in bellows with a high number of convolutions and a small pitch, providing exceptional flexibility.
The edge-welding process allows for the creation of leak-tight seals, making these bellows ideal for applications involving vacuum or high-purity gases. The high flexibility of edge-welded bellows also enables them to accommodate significant axial, lateral, and angular displacements.