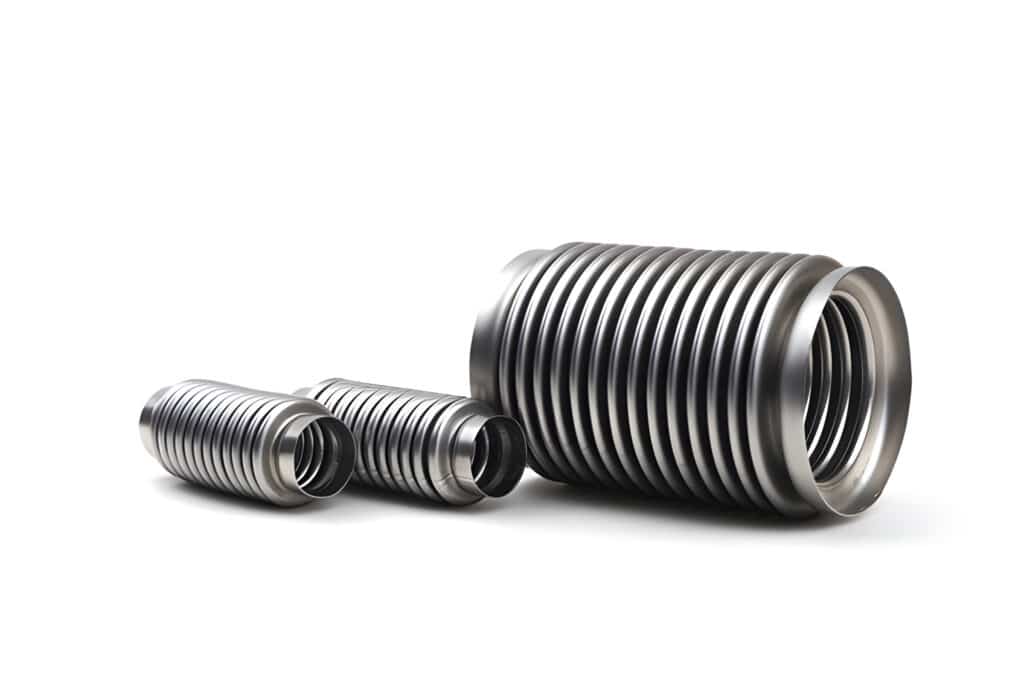
What Are the Different Types of Metal Bellows
Metal bellows are flexible, mechanical seals that consist of thin, corrugated metal sheets welded together to form a leak-tight joint. They are designed to compensate for axial movement, misalignment, and thermal expansion in various applications.
There are three main types of metal bellows:
Formed
Formed metal bellows are created by cold-forming or hydroforming thin metal sheets into a corrugated shape. This process is suitable for producing bellows with smaller diameters and shorter lengths, typically using materials such as stainless steel, brass, or bronze.
Welded
Welded metal bellows are manufactured by welding individual diaphragms or convolutions together to form a flexible, leak-tight assembly. This method allows for the production of bellows with larger diameters, greater lengths, and a wider range of materials, including high-strength alloys and exotic metals.
Electroformed
Electroformed metal bellows are produced by electrodepositing metal onto a mandrel or form, creating a seamless, high-precision bellows with thin walls and complex geometries. This process is often used for miniature bellows or those requiring exceptional strength and durability.
What are Edge Welded Metal Bellows
Edge welded metal bellows are a type of welded bellows that offer superior performance and flexibility compared to formed bellows. They are constructed by welding the inner and outer edges of individual diaphragms, creating a series of nested convolutions that can accommodate significant axial displacement, offset motion, and angular rotation.
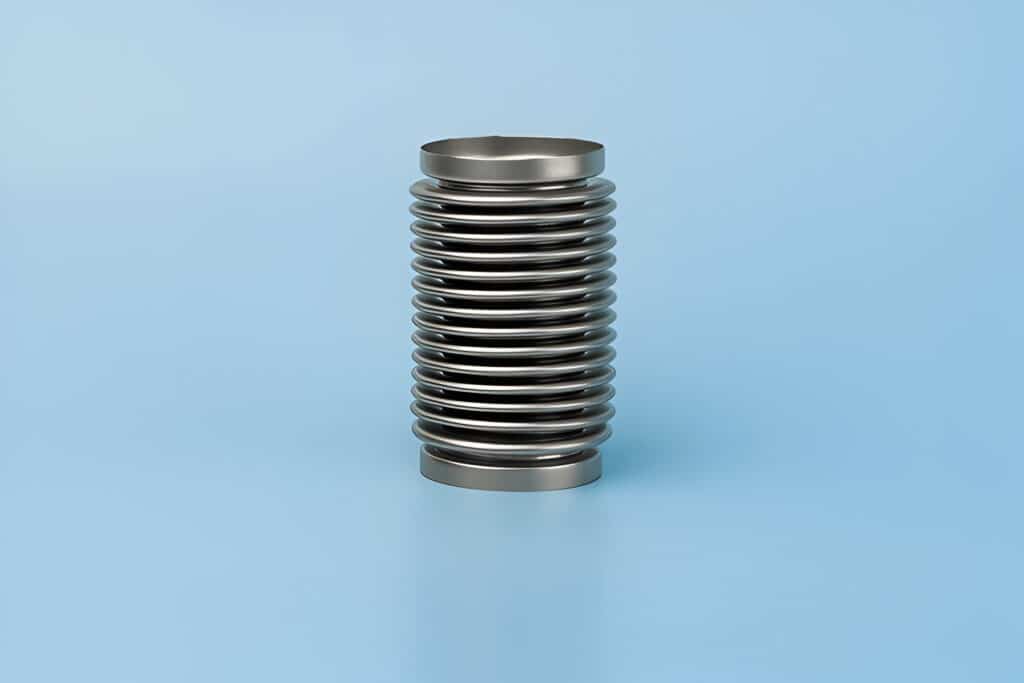
Advantages of Edge Welded Metal Bellows
- Superior stroke capabilities compared to formed bellows
- Greater flexibility and lower spring rates
- Wide range of construction materials beyond high-elongation metals
- Eliminates dynamic sealing elements prone to failure
- Excellent leak-tight performance in vacuum and pressure environments
- Withstands cryogenic to high temperatures
- Resistant to corrosive media and harsh environments
- Customizable designs for specific application requirements
Applications for Edge Welded Metal Bellows
- Aerospace and defense industries
- Semiconductor manufacturing equipment
- Medical devices and instrumentation
- Cryogenic systems and liquid nitrogen handling
- Ultra-high vacuum chambers and beamlines
- Automotive exhaust gas recirculation (EGR) valves
- Oil and gas exploration and processing
- Industrial automation and motion control systems
Materials of Construction for Edge Welded Metal Bellows
- Stainless steels (304L, 316L, 321, 347)
- High-strength alloys (Inconel, Hastelloy, Monel)
- Titanium and titanium alloys
- Copper and copper alloys (Beryllium Copper, Phosphor Bronze)
- Nickel and nickel alloys
- Aluminum alloys
- Exotic metals (Zirconium, Tantalum, Molybdenum)
How Edge Welded Metal Bellows Are Manufactured
The manufacturing process for edge welded metal bellows involves precise stamping, forming, and welding techniques to create a flexible, leak-tight assembly. The process typically includes the following steps:
- Material selection based on application requirements
- Stamping individual diaphragms with the desired profile and thickness
- Cleaning and preparing diaphragms for welding
- Assembling diaphragms in a nested configuration
- Welding inner and outer edges of diaphragms using advanced techniques such as laser, electron beam, or micro-plasma welding
- Inspecting welds for integrity and leak-tightness
- Performing additional treatments, such as heat treating, passivation, or plating, as required
- Final inspection, testing, and packaging in a cleanroom environment
What Is the Difference Between Formed and Welded Bellows
- Manufacturing process: Formed bellows are cold-formed or hydroformed from a single piece of metal, while welded bellows are assembled from individually stamped diaphragms that are welded together.
- Size and length limitations: Formed bellows are typically limited to smaller diameters and shorter lengths due to the forming process, while welded bellows can be produced in much larger sizes and lengths.
- Material options: Formed bellows are usually made from high-elongation metals like brass or bronze, while welded bellows can be constructed from a wide variety of materials, including stainless steels, high-strength alloys, and exotic metals.
- Flexibility and spring rates: Welded bellows, particularly edge welded bellows, offer greater flexibility and lower spring rates compared to formed bellows, making them suitable for applications requiring significant axial displacement or angular movement.
- Pressure and vacuum capabilities: Welded bellows can withstand higher internal and external pressures, as well as deeper vacuum levels, compared to formed bellows due to their robust construction and leak-tight welds.
- Cost and lead times: Formed bellows are generally less expensive and have shorter lead times than welded bellows, as the forming process is simpler and more automated. However, the cost difference narrows for larger quantities or custom designs.